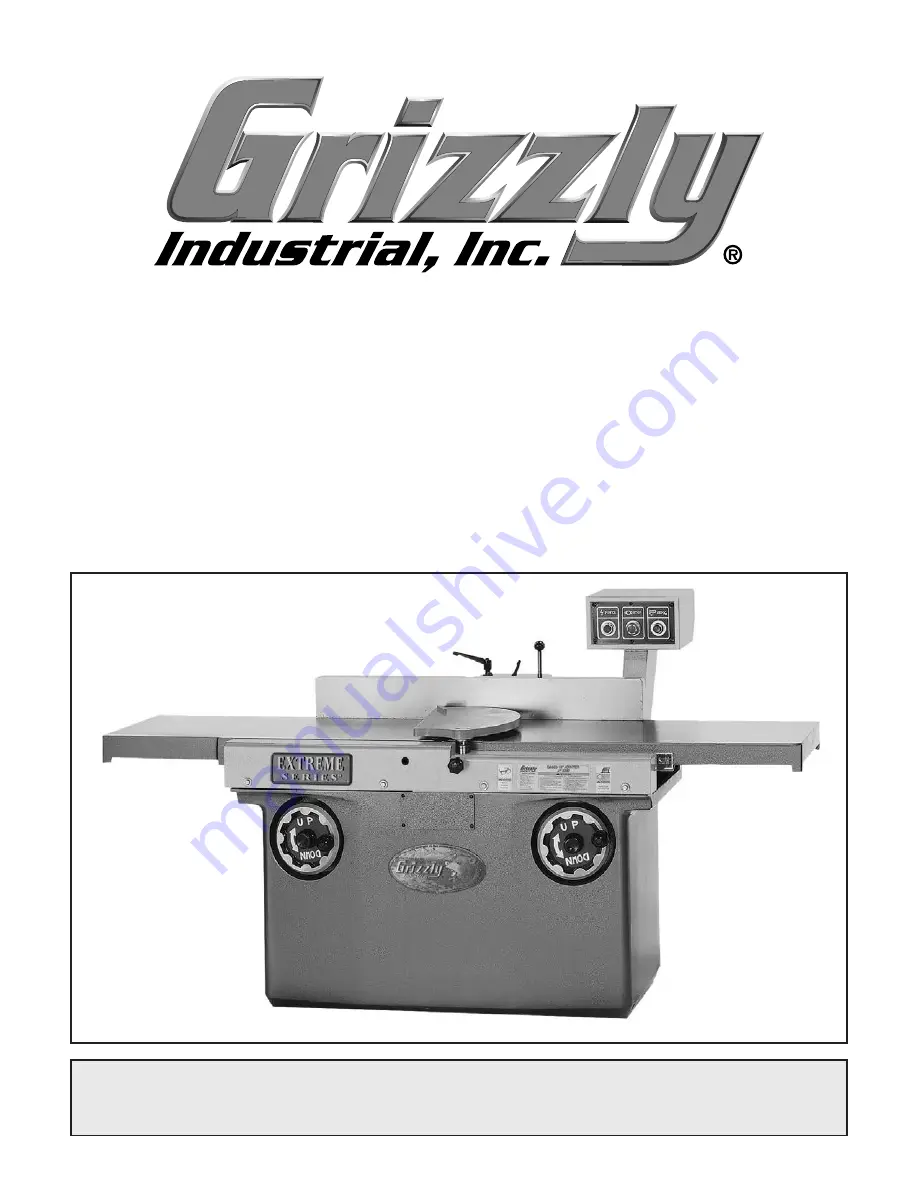
MODEL G9860, G9860ZX,
G9953ZX, & G9953ZXF
EXTREME SERIES JOINTER
OWNER'S MANUAL
(For models manufactured since 10/20)
COPYRIGHT © NOVEMBER, 2008 BY GRIZZLY INDUSTRIAL, INC., REVISED OCTOBER, 2020 (KS)
WARNING: NO PORTION OF THIS MANUAL MAY BE REPRODUCED IN ANY SHAPE
OR FORM WITHOUT THE WRITTEN APPROVAL OF GRIZZLY INDUSTRIAL, INC.
#TS11249 PRINTED IN TAIWAN
V6.10.20
Summary of Contents for EXTREME G9860
Page 72: ......