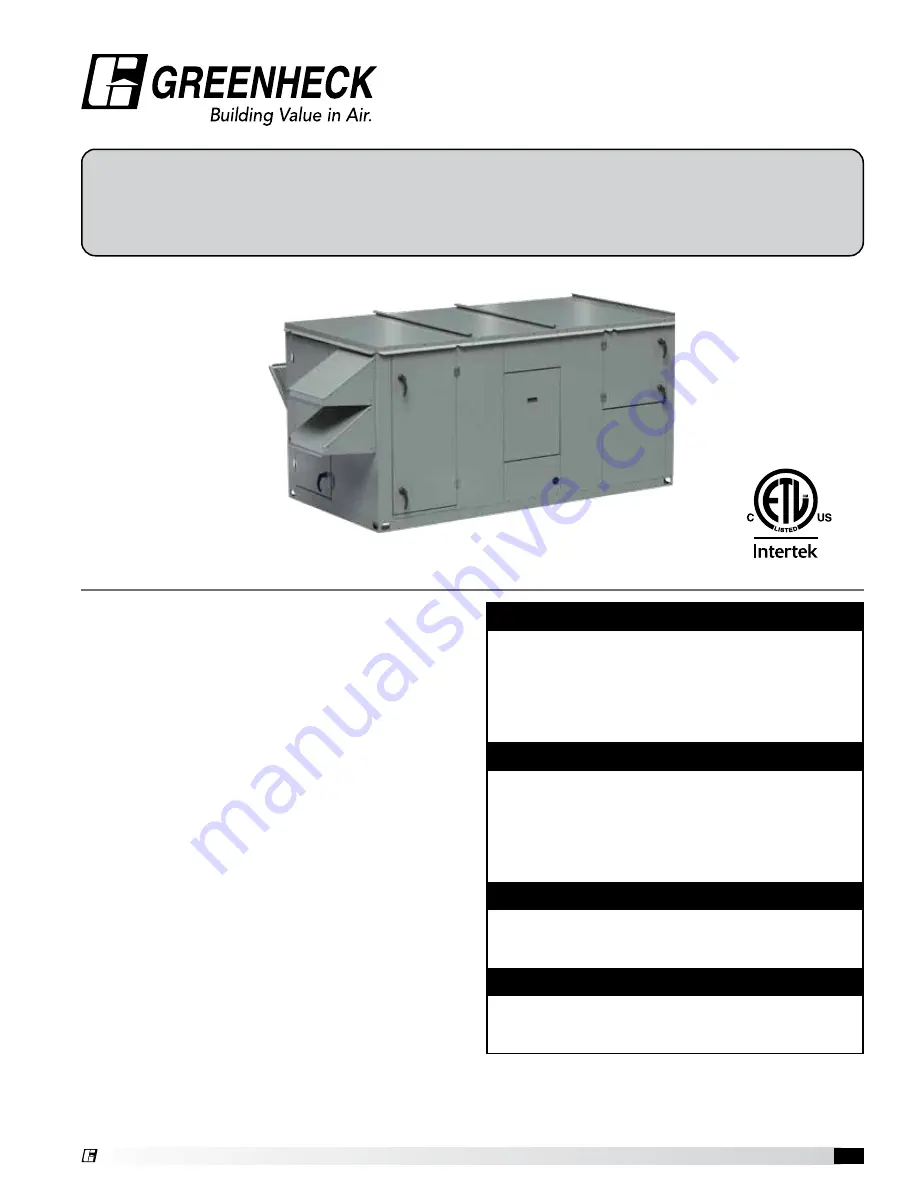
®
Installation, Operation and Maintenance Manual
Please read and save these instructions for future reference. Read carefully before attempting to assemble, install,
operate or maintain the product described. Protect yourself and others by observing all safety information. Failure
to comply with instructions could result in personal injury and/or property damage!
Energy Recovery Ventilator with Heating and Cooling
1
®
Only qualified personnel should install this system.
Personnel should have a clear understanding of these
instructions and should be aware of general safety
precautions. Improper installation can result in electric
shock, possible injury due to coming in contact with
moving parts, as well as other potential hazards,
including environmental. Other considerations may be
required if high winds or seismic activity are present.
If more information is needed, contact a licensed
professional engineer before moving forward.
1
. Follow all local electrical and safety codes, as well as
the National Electrical Code (NEC), the National Fire
Protection Agency (NFPA), where applicable. Follow
the Canadian Electrical Code (CE) in Canada.
2. All moving parts must be free to rotate without
striking or rubbing any stationary objects.
3. Unit must be securely and adequately grounded.
4. Do not spin fan wheel faster than maximum
cataloged fan RPM. Adjustments to fan speed
significantly affect motor load. If the fan RPM is
changed, the motor current should be checked to
make sure it is not exceeding the motor nameplate
amps.
5. Verify that the power source is compatible with the
equipment.
6. Never open access doors to the unit while it is
running.
General Safety Information
DANGER
• Always disconnect power before working on or near
this equipment. Lock and tag the disconnect switch
or breaker to prevent accidental power up.
• If this unit is equipped with optional gas
accessories, turn off gas supply whenever power is
disconnected.
CAUTION
This unit may be equipped with a compressed
refrigerant system. If a leak in the system should
occur, immediately evacuate and ventilate the area.
An EPA Certified Technician must be engaged to
make repairs or corrections. Refrigerant leaks may
also cause bodily harm.
CAUTION
When servicing the unit, the internal components may
be hot enough to cause pain or injury. Allow time for
cooling before servicing.
WARNING
The roof lining contains high voltage wiring. To
prevent electrocution, do not puncture the interior or
exterior panels of the roof.
Document 476054
Model ERCH
Energy Recovery Ventilator
with Heating and Cooling