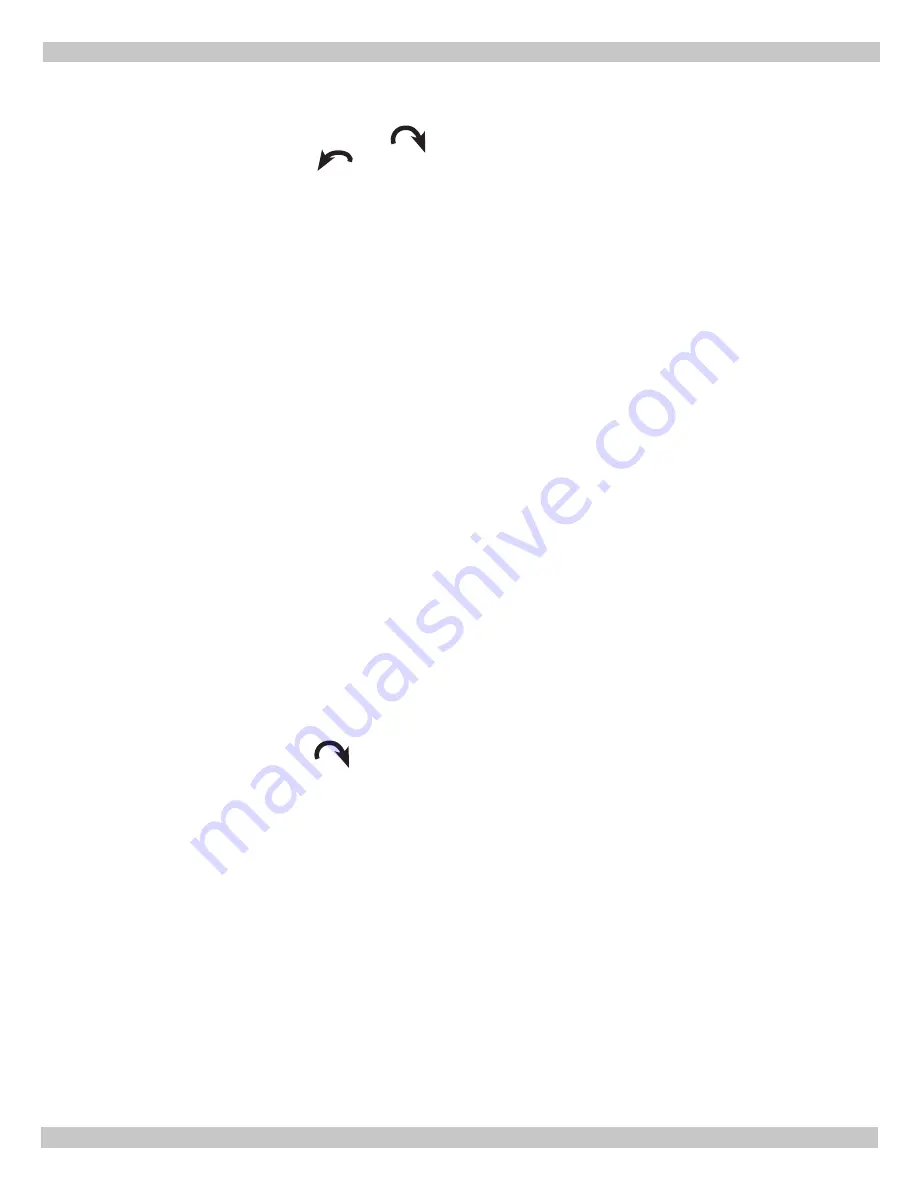
31
1.
Adjust gas input to boiler by removing protective cap on
pressure regulator
,
and turning screw clockwise
to
increase input and counterclockwise
to decrease
input. See Figure 12-1 page 27.
2.
Manifold pressures are taken at outlet side of gas valve.
See page 23 for proper pressure recommendations.
3.
To check for proper flow of natural gas to boiler, divide
input rate shown on rating plate by heating value of
gas obtained from local gas company. This determines
number of cubic feet of gas required per hour.
4.
Determine flow of gas through meter for two minutes
and multiply by 30 to get hourly rate with all other gas
appliances off.
5.
Make minor adjustments to gas input as described
above. See Figure 12-1 page 27.
6.
Change burner orifices if final manifold pressure varies
more than plus or minus 0.3 inches water column from
specified pressure listed on boiler rating plate.
7.
Primary air adjustment is not necessary, therefore air
shutters are not furnished.
CHECK SAFETY CONTROL CIRCUIT. Test ignition
system safety shutoff device after placing boiler in
operation.
Test ignition
system safety shutoff device
after placing boiler in operation. Blocked vent switch
and rollout switch can be tested by removing one of
the wires. See Figure 13-1 page 28.
8.
Intermittent Pilot: With main burner operating, turn
pilot gas adjusting screw clockwise
until pilot
gas is turned off. Within 90 seconds main gas control
closes, shutting off gas to main burner.
9.
High Limit Control
: Remove front cover and
note temperature setting. Refer to appendix A for
adjustment procedure. Decrease setting to minimum
and operate boiler. When boiler water temperature
exceeds control temperature setting, control will open
circuit, closing automatic main gas valve.
14.4 Adjusting Gas Input
14 - GENERAL MAINTENANCE AND CARE INSTRUCTIONS
PN 240012807, Rev. C [11/15/2020]