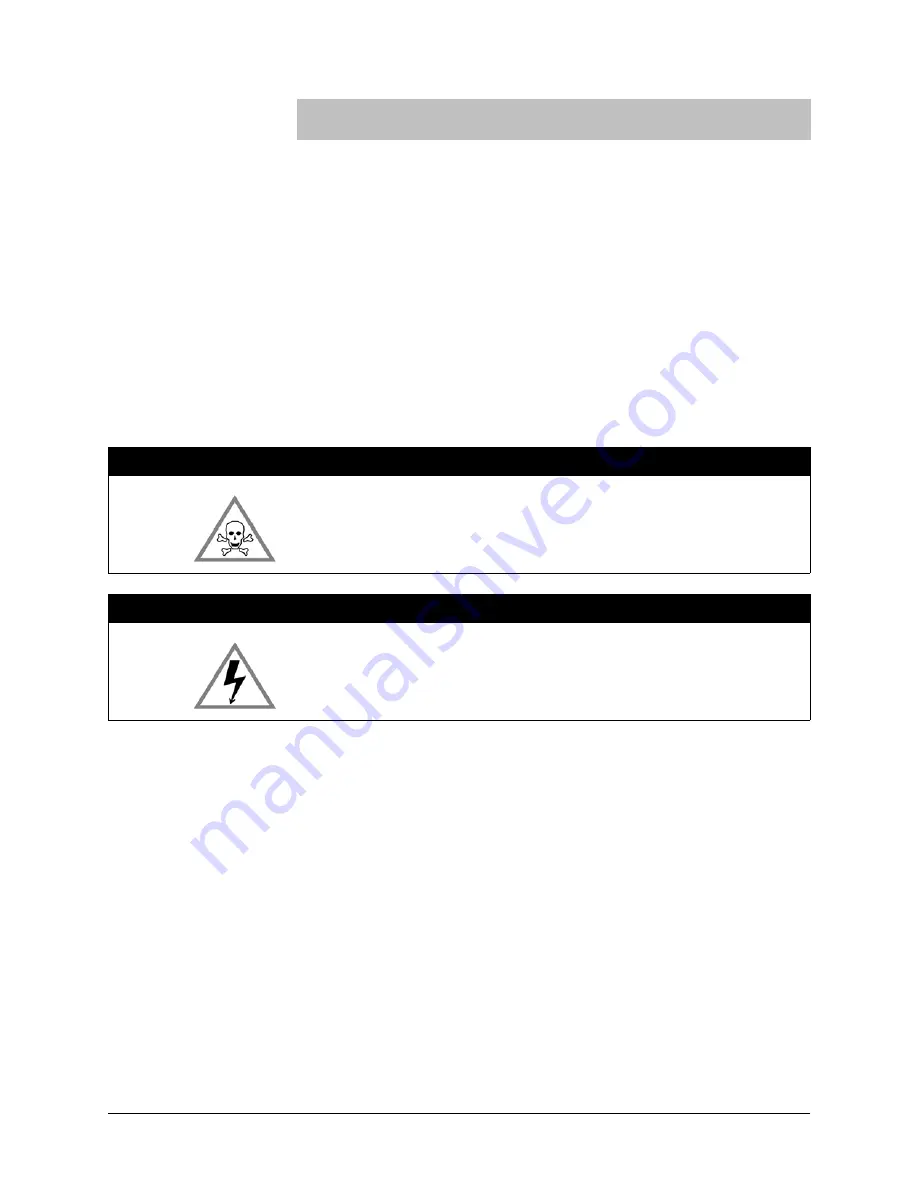
Mini-Convectron
®
Module with DeviceNet
®
Digital Interface
37
Chapter 6 Service
6.1
Introduction
The procedures in this section provide instructions for normal service issues
that may be required during use of the 275 Mini-Convectron
Vacuum Gauge
Module.
Phone customer service at
1–303–652–4400
or
1–800–776–6543
if there
are questions pertaining to the service of the 275 Mini-Convectron Vacuum
Gauge Module.
6.2
Mini-Convectron
Gauge Tube
Cleaning
When the fine sensor wire within the gauge tube is severely contaminated
with oil or other films, its emissivity or diameter can be altered causing a
change in gauge tube calibration.
Cleaning the internal components of the gauge tube with trichloroethelyne,
perchloroethelyne, toluene, or acetone is possible but must be done
carefully to prevent damage to the sensor wire.
Use the following procedure to clean the internal components of the gauge
tube.
1. Disconnect the DeviceNet and Trip Point cable connectors.
2. Remove the eight screws holding the two end plates of the module as
3. Remove the one side, front and rear cover plates from the PC board/
gauge tube assembly as shown in Figure 6-1.
WARNING
Follow all product safety precautions for the solvent being used to prevent
personal injury.
WARNING
To prevent electrical shock, shut down electrical power before servicing
the
275
Mini-Convectron Vacuum Gauge Module. Do not touch any
gauge pins while the gauge tube is under vacuum or connected to a
controller.
Summary of Contents for Mini-Convectron 275 Series
Page 2: ......
Page 4: ......
Page 8: ...iv Mini Convectron Module with DeviceNet Digital Interface...
Page 22: ...14 Mini Convectron Module with DeviceNet Digital Interface...
Page 44: ...36 Mini Convectron Module with DeviceNet Digital Interface...
Page 51: ......