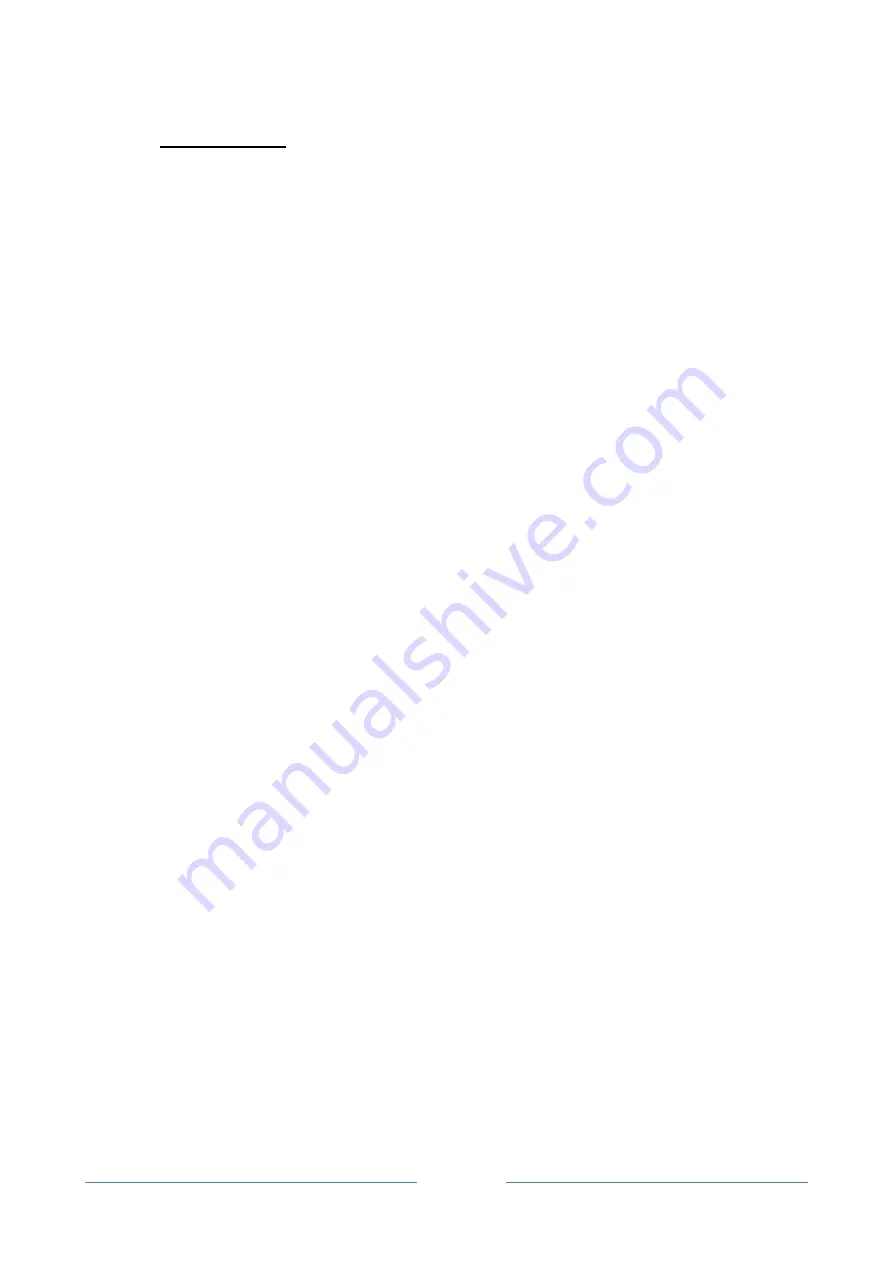
GM · CONVERTING UNIT
52
19.1.
Step by step guide
•
To startup spot printing follow the steps below. Please see picture section in the back of this guide
when there are references to buttons or menus.
•
Enter the Z size of the plate cylinder in the parameters menu of the touch screen. Always use the Z
size, never enter in mm. The Z count is engraved into the tooth wheel of the plate cylinder. Please
note that the system has a “slow run” feature. This feature will allow the plate cylinder to rotate at
stand still to avoid dry out of water varnish. If UV varnish is used turn off this feature in the
parameters menu.
•
Mount the print plate on the plate cylinder. Make sure to use the correct tape and plate thickness
for specific cylinder. This most common tape thickness is 0.38mm. The standard plate size
thickness is 1.7mm. If tape and plate thickness does not match the circumsphere of the cylinder
will be wrong. This will lead to a gap between the rotations (where the plate is put together on the
print plate) and misprint (print will not fit the preprinted web).
•
Important: Make sure the cylinder is only “loosely” in grip with the tooth wheels. When the
cylinder is engaged later in the process air pressure will make the cylinder move further down.
•
Adjust the print station. Use the guide the main manual for the machine. This step is normally not
needed, but if the station is completely out (startup after install), has been cleaned down or the here
is a big difference in print plate cylinder size it may be needed. The adjustment assures that all
rollers in the unit are parallel and a correct distance between the cylinders has been set. Remember
that the anvil cylinder is the reference in the station
•
Turn on UV lamp. Start running the web slowly with the plate cylinder up. Adjust the mark reader
next to the flexo station. Make sure it reads one mark pr. Rotation of the plate cylinder. Look at the
RED light of the mark reader. Only one blink pr. rotation of the plate cylinder. Using more marks
may lead to problems synchronizing (the system may lock on to a wrong mark) and is generally
not recommended. Look at the deviation field for the spot varnish. When the field is dropping
below (plate cylinder synchronized) drop the cylinder down by pressing it.
•
Adjust print quality by turning the two adjusters on the top of the flexo station station. Look at the
sides – you must have an even print quality on each side of the print plate. There are typically
support lines on each side of the print plate.
•
Move the station into register across the web. This is done by turning the side adjustment block to
the left or right.
•
Move the station into register in the web direction. This is done by turning the offset knob on the
side of the station. Please note that the system will move slowly. This can also be done from the
touch screen.
•
Increase speed and monitor print quality. Fine adjustment of pressure on print plate cylinder may
be needed as speed increases.