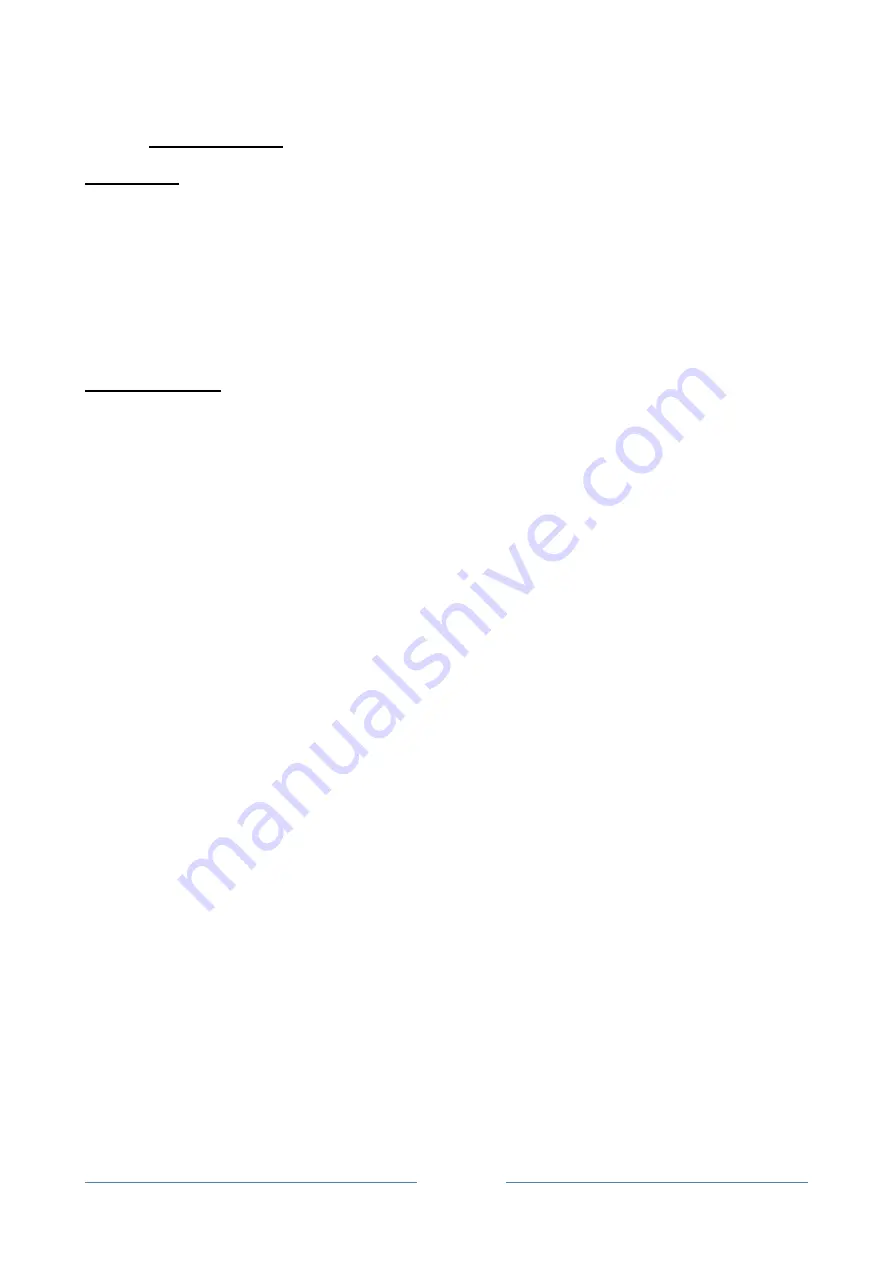
GM · CONVERTING UNIT
51
19.
Spot varnish guide.
Introduction
The spot varnish function of the converting unit enables the system to put down print in register. This can
be used for various applications; spot varnish effects (only part of the web varnished), Cold foil (a glue is
printed in patterns to make silver/gold effects) and single color printing. The most common option is the
spot varnish effect where only a part of the web is varnished. The spot varnish only has one parameter –
the “Z” count –the number of teeth on the tooth wheel of the print cylinder. The Z unit is 1/8 of an inch or
3.175mm pr. Tooth. A 10” plate cylinder has a Z count of 10*8= 80Z and a plate size of 10”*25,4mm =
254mm.
Working principle
When equipped with a spot varnish option the print plate cylinder in the flexo graphic station is driven by
an independent motor. This means that the print plates cylinder can be synchronized with the web using a
print mark reader located next to the station. To make sure printing starts in the same position every time a
job is setup the system makes a “homing” when a new cylinder is loaded. The print plate cylinder is
“homed”by turning until a small hole in the tooth wheel passes a sensor located in the frame of the flexo
station. This hole is only once (at the startup of the job). The cylinder will make a quick rotation and find
the hole. When the system is synchronized it will start to look for a mark on the web. When found the plate
cylinder is moved into a position in reference to the mark. This position can be altered by turning the “offset
knob” on the side of the station or pressing the “offset” button on the touch screen. The offset determines
the distance between the printed mark on the web and the zero hole on the cylinder.
The print plate cylinder can be lifted up and down on the touch screen of the machine. This is done by
pressing the cylinder symbol. When the print cylinder is “down” only small (+/-1mm corrections are
possible). This is done to protect the print plate cylinder from rapid movements when pressed against the
web (this could cause web break). When the cylinder is up the cylinder can make a ½ rotation of the
cylinder. This is enables the system to go quickly in register. Important: Due to the small corrections
possible in print mode the print must match the circumsphere of the cylinder with a tolerance of +/- 0.1mm.
If the print is “out” of size the gab between the repeats will be incorrect and in bad cases the machine will
not be able to synchronize (the register will “slide” out ).
To determine if the system is “locked” on the print mark monitor the “deviation” field on the touch screen.
The deviation is a feedback from the register system that constantly tells the operator how far the print is
out. When “locked” on the target this field is normally jumping in the range +-0.3mm. If it is close to 1
mm there is a risk that the system will “slide out” of register and the number will steady increase or decline;
example print is 1.1 mm out. Deviation values will be 1.1 – 1.2 – 1.3 – 1.4 constantly sliding 0,1mm out
because the machine is not able to correct the full amount needed to be in register with a misprinted web.
The machine also provides the operator with a 2. Feedback – the “measured print length” on the touch
screen. This is a measurement of how much web has passed between two marks. It will give a very quick
indication if the plate size and the distance between the print marks are not equivalent.
If the system fails to synchronize the machine has an option to compensate. This is done from the run
screen (with RED start button) by pressing the tool icon on the touch screen. Here there is an option called
“spot scaling”. Spot scaling can force the cylinder to run quicker or slower relative to the web. This will
allow a misprinted web to work (be locked in register), but the price to pay is poor print quality. To adjust
the scaling press the + or – until the deviation number stabilizes around 0.