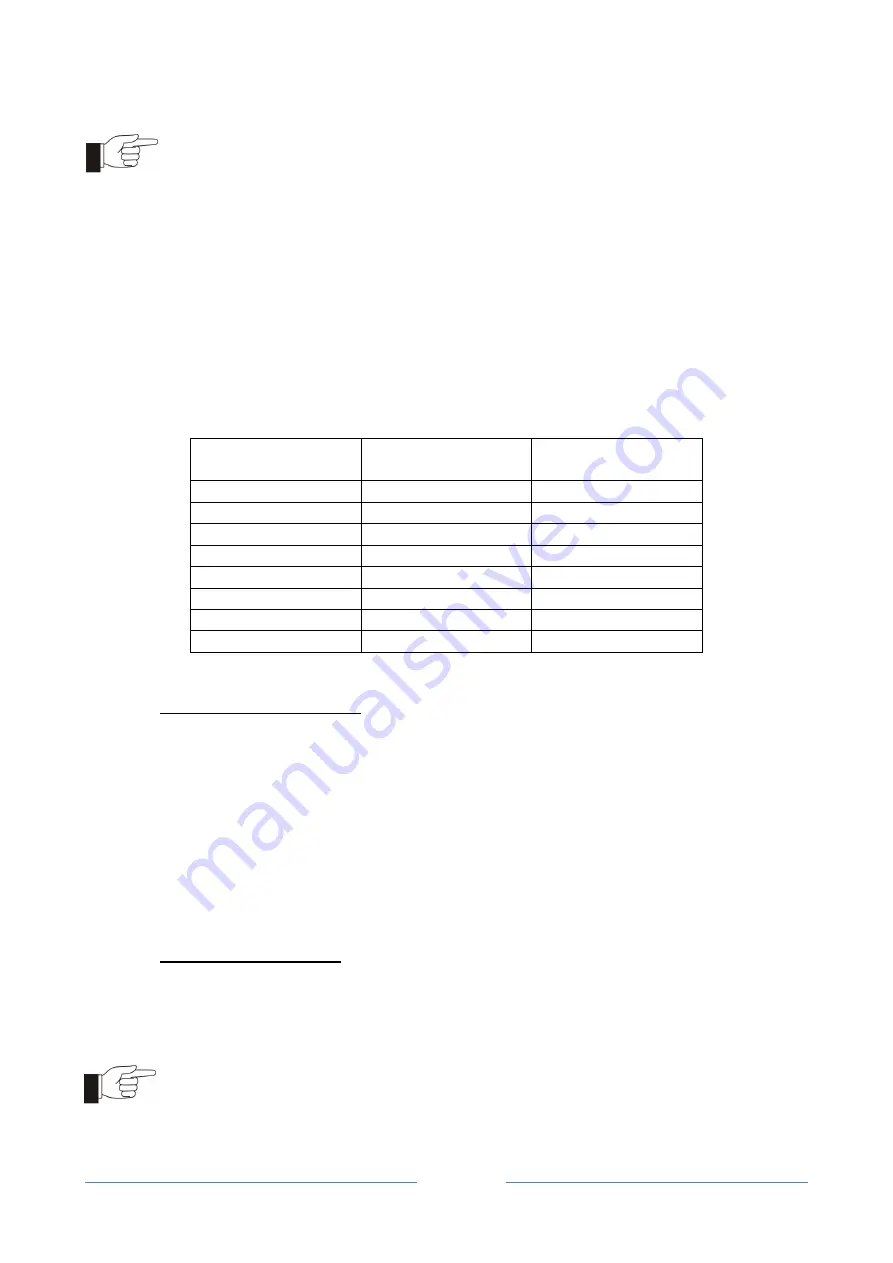
GM · CONVERTING UNIT
44
60 lines per cm.
Used for full inking up/varnishing on highly absorbent paper qualities. This coarse
screen is best suited for special inking-up rollers.
70 - 80 lines per cm.
For full inking-up/varnishing with full solids on finer paper such as e.g. High Gloss
qualities.
100 - 140 lines per cm.
For mixed printing, smaller printing surfaces and text, etc.
120 - 240 lines per cm
.
For screen and process printing (see below).
Lines per cm
Cell depth
micron
Theoretical ink transfer
grms/m
2
80
15
10
100
15
8
120
13
6,5
140
15
7
140
11
6
140
7
4,5
160
6
3,5
220
7
2
18.3.
Mounting of the anilox roller
Pull out the inking roller by loosening the two mounting handles. Carefully slide out the inking roller.
Loosen the two handles for mounting of anilox roller and carefully slide in the anilox roller. Tighten the
handles and make sure the anilox is correctly aligned towards the varnish roller/printing roller. Slide in the
inking roller and make sure its aligned towards the anilox roller.
An anilox roller is a precious piece of tool and ought to be handled with care. Especially the ceramic
covering at the end of the roller can be damaged by a stroke or a loss on the floor.
The surface must be cleaned after use, so that the roller can transfer an even and uniform layer of ink to the
plate cylinder. Dried-up ink or dirt in the cups of the surface will reduce the quantity of ink and produce an
uneven image.
18.4.
Mounting of the ink roller
The roller is placed in the same way as the anilox roller and locked with the bearing housing. Levers for
the ink roller's pressure on the anilox roller must be disengaged (down) on insertion and removal. The ink
rollers must be stored suspended in the shaft ends so that the rubber covering will not be deformed.
NOTE!
When the press is not in use fold down the levers, so that the ink roller's
rubber is not squeezed against the anilox roller.