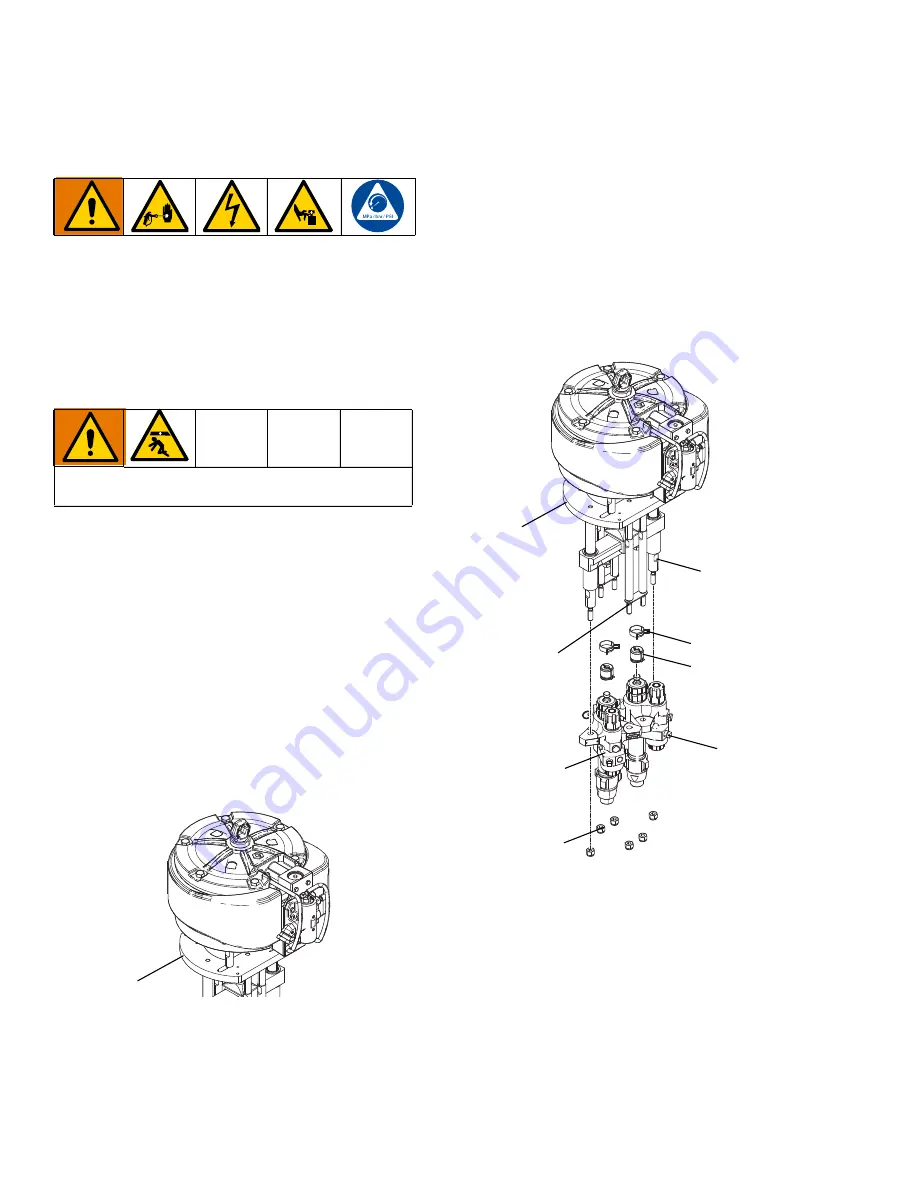
Repair
56
3A6283F
Repair
Follow the complete
procedure starting on
page 44, which includes pressure relief and full system
flushing if service time may exceed pot life time before
servicing fluid components and before transporting the
system to a service area.
Pump Assembly Repair
The displacement pumps and air motor may be
removed and serviced separately or the entire pump
and motor assembly can be removed with a hoist.
Pump Assembly Removal
1. Flush all system components. Follow the complete
procedure starting on page 44.
2. Disconnect all hoses from the pump assembly.
3. Disconnect the hopper fluid lines from the pump
fluid inlet (228).
4. Remove screws (6) and washers (5) under the tie
plate (901). For additional parts identification, see
5. Use hoist to remove the pump assembly by the lift
ring and carefully lift out of stand (1).
Remove XP Displacement Pump
1. Flush all system components. Follow the complete
procedure starting on page 44.
2. Disconnect the hopper fluid lines from the pump
fluid inlet (228).
3. Disconnects the outlet hose (12 or 24). For parts
identification, see
4. Remove the spring clamp (930) and coupling (919).
5. Use a wrench to hold the tie rod (902) flats to keep
the rods from turning. Unscrew the nuts (908) from
the tie rods and carefully remove the displacement
pump (917 or 918) and lower straps (935).
6. Refer to the Xtreme Displacement Pump manual to
service or repair the displacement pump.
7. Follow the steps in reverse order to reinstall the
displacement pump.
NOTE:
Torque nuts (908) to 95-105 ft-lb (129-142 N•m).
To avoid serious injury due to the pump assembly
falling, secure a hoist to the lift ring.
901
WLD
930
919
918
917
908
902
935
901
Summary of Contents for XP50s-hf
Page 61: ...Parts 3A6283F 61 XP50s hf and XP70s hf Proportioners Continued WL F ...
Page 64: ...Parts 64 3A6283F Water Jacketed Heated Hose Packages WL D 2 2 2 247 246 245 ...
Page 66: ...Parts 66 3A6283F Non Heated Hose Packages WL D 2 2 ...
Page 68: ...Parts 68 3A6283F Non Hazardous Location Electric Heated Hose Packages WL D 480V 240V ...
Page 69: ...Parts 3A6283F 69 Hazardous Location Electric Heated Hose Packages WL D 9 9 ...
Page 82: ...Dimensions 82 3A6283F Dimensions System Dimensions WL D LQ FP LQ FP LQ FP Top View Side View ...