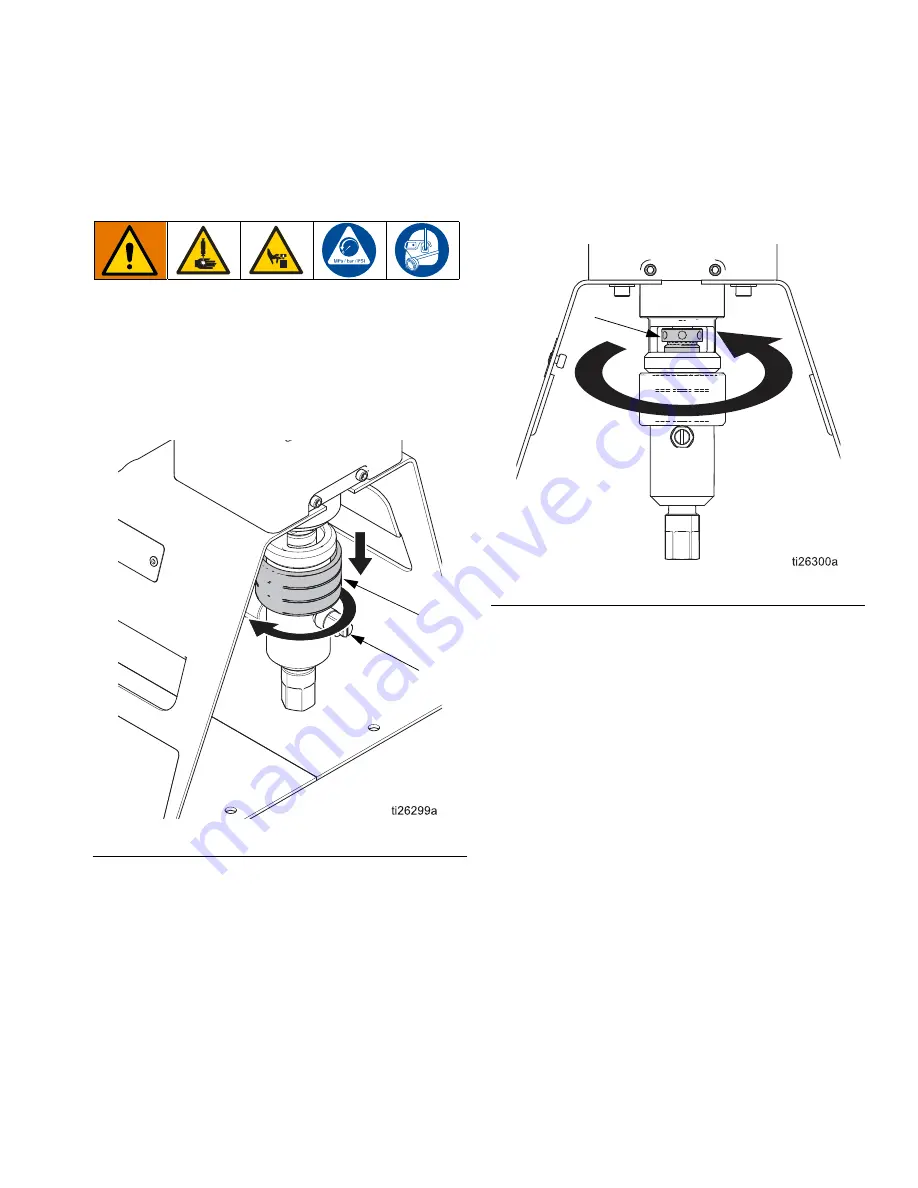
Repair
334513A
29
Repair
Wolverine Basic Pump Repair
Disconnect Pump
1.
2.
Expose the packing nut (37) by rotating the dust
cover (15) clockwise and sliding down when loose.
3.
Loosen, but do not remove, the packing nut (37).
4.
Expose the cam (8) by loosening the cap screws
(27) and removing the molded guard (26). The cap
screws will remain with the molded guard.
F
IG
. 7 Expose packing nut
21
15
2
1
F
IG
. 8 Loosen packing nut
37