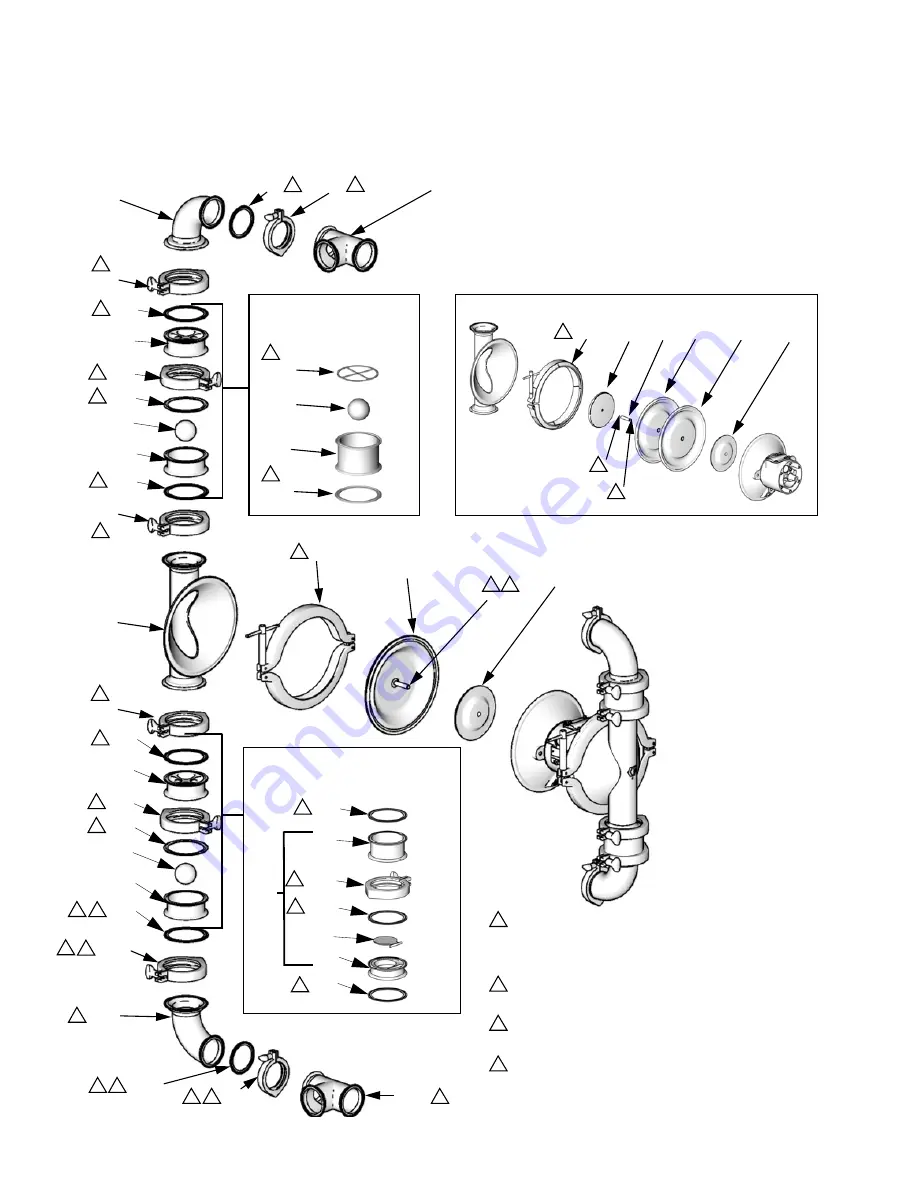
Parts Drawing, Fluid Section
32
310622ZAL
Parts Drawing, Fluid Section
3A Pump Shown
128
132
*242
*541
233
*240
234
128
*129
130
*331
129*
130
135
446*
Flapper Check Valve
Assembly
ti17272a
339*
445
Apply a high-strength thread locker to attach
the screw to the diaphragm plate (sanitary
pump) or to the diaphragm (3A pump), if
needed.
Apply a medium strength thread locker to
shaft side of screw threads.
Apply a waterproof sanitary lubricant to
clamps, clamping surfaces, and gaskets.
Parts not included on BES/ram models (Part
Numbers 24xxxx).
1
2
3
4
3
3
3
3
3
3
3
3
2
Sanitary Ball Check
Valve Assembly
*240
*240
2XA
132
2XB
*240
541
3
3
3
3
132
3
132
3
*240
*240
2XA
132
2XB
*240
541
3
3
3
3
132
3
TI7644a
446*
444 143
445
135
1
2
3
TI4729c
Sanitary Diaphragm Assembly
447*
*240
*240
252
132
248
*240
251
200
3
3
3
3
TI4683a
4
4
4
4
4
4
446a*
1
Tri-Clamp
Model Shown
Summary of Contents for SaniForce 1590 3A
Page 5: ...Models 310622ZAL 5...