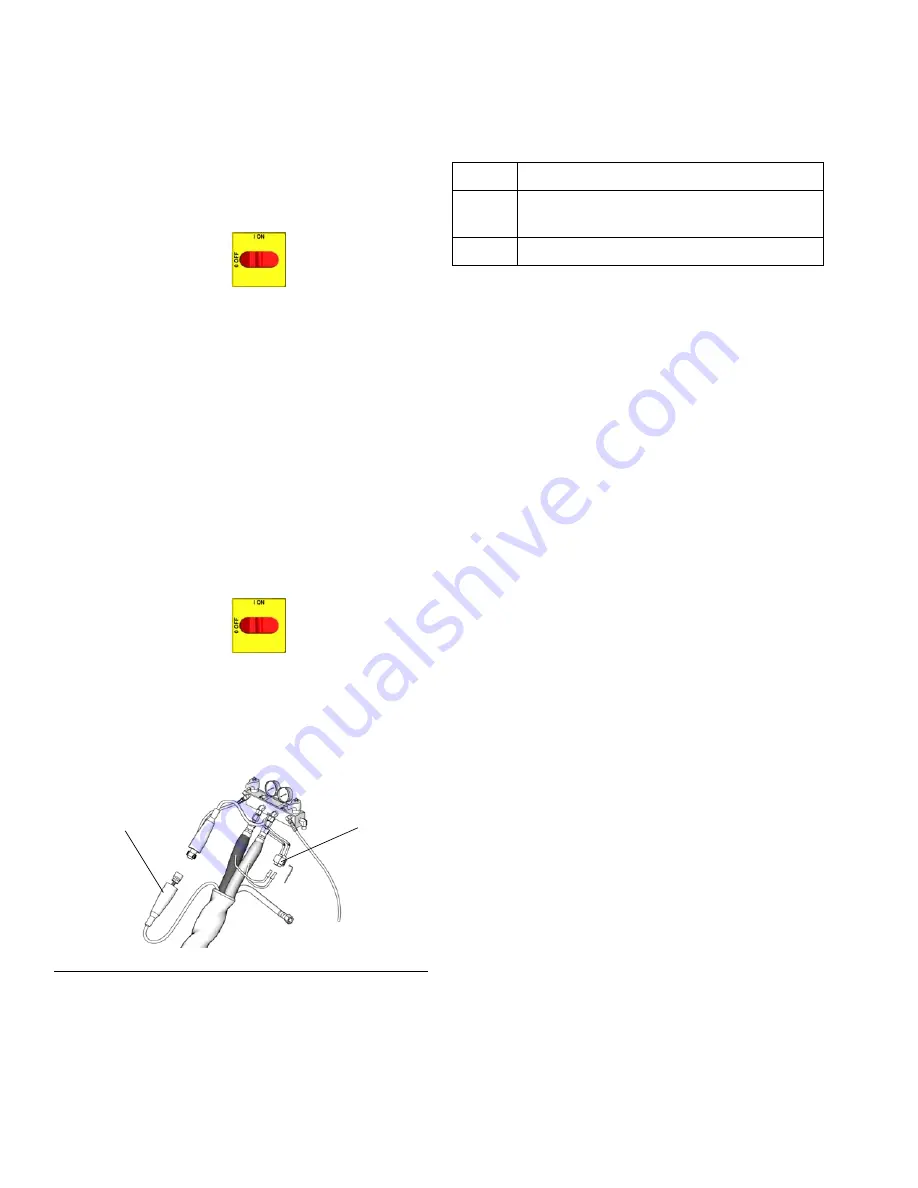
Repair
38
312063Z
Heated Hose
NOTE:
Refer to your heated hose manual for hose
replacement parts.
Check Hose Connectors
1. Turn main power OFF
. Disconnect power
supply.
2. Relieve the pressure. See
, page 26.
NOTE:
Whip hose must be connected.
3. Disconnect hose connector (D) at Reactor, F
. 10.
4. Using an ohmmeter, check between the two
terminals of the connector (D). There should be
continuity.
5. If hose fails test, retest at each length of hose,
including whip hose, until failure is isolated.
Check FTS Cables
1. Turn main power OFF
. Disconnect power
supply.
2. Relieve the pressure. See
, page 26.
3. Disconnect FTS cable (F) at Reactor, F
4. Test with ohmmeter between pins of cable
connector.
5. If cable fails test, retest at FTS,
F
IG
. 10 Heated Hose
ti9878a
F
D
Pins
Result
1 to 2
approximately 35 ohms per 50 ft (15.2 m) of
hose, plus approximately 10 ohms for FTS
1 to 3
infinity
Summary of Contents for Reactor H-XP2 Elite
Page 71: ...Dimensions 312063Z 71 ...