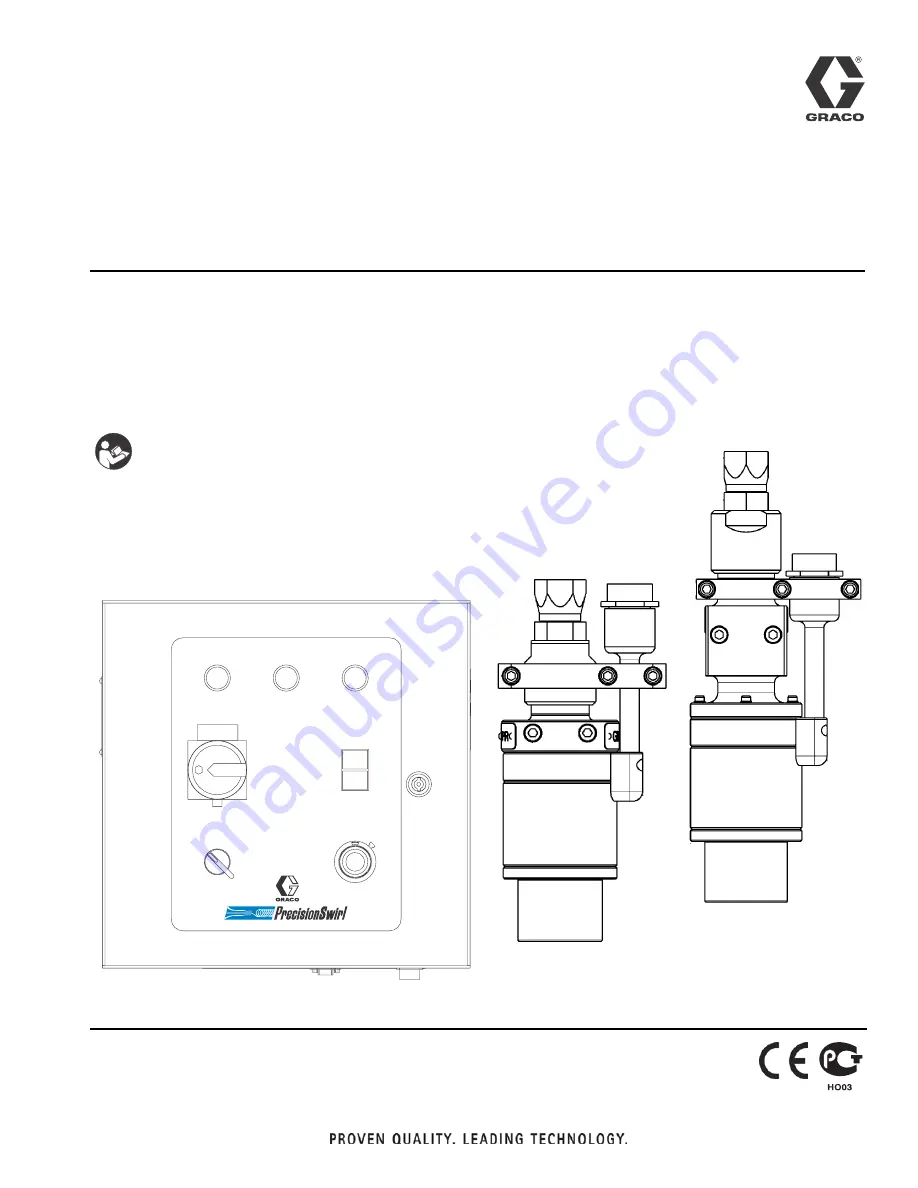
Instructions - Parts List
PrecisionSwirl
™
Module
An orbital dispenser used to apply sealant and adhesive materials for a variety of
applications.
Part No. 241658, 234029, 289911 and 289912
3500 psi (24.1 MPa, 241 bar) Maximum Fluid Working Pressure
See page 2 for List of Models.
U.S. Patent No. 6,499,673
EU Patent No. 0852160
Important Safety Instructions
Read all warnings and instructions in this manual.
Save these instructions.
PrecisionSwirl
Orbital Dispenser
243402 and 243403
POWER
MOTOR FAULT
RUN
MAIN
RUN / ENABLE
CONTROL
S
ELECT
AUTOMATIC
MANUAL
MANUAL
S
PEED CONTROL
8037B
PrecisionSwirl Control Assembly
918616
289261 and 289262
PrecisionSwirl
Orbital Dispenser
310554V
ENG
Summary of Contents for PrecisionSwirl 234029
Page 7: ...Warnings 310554V 7...