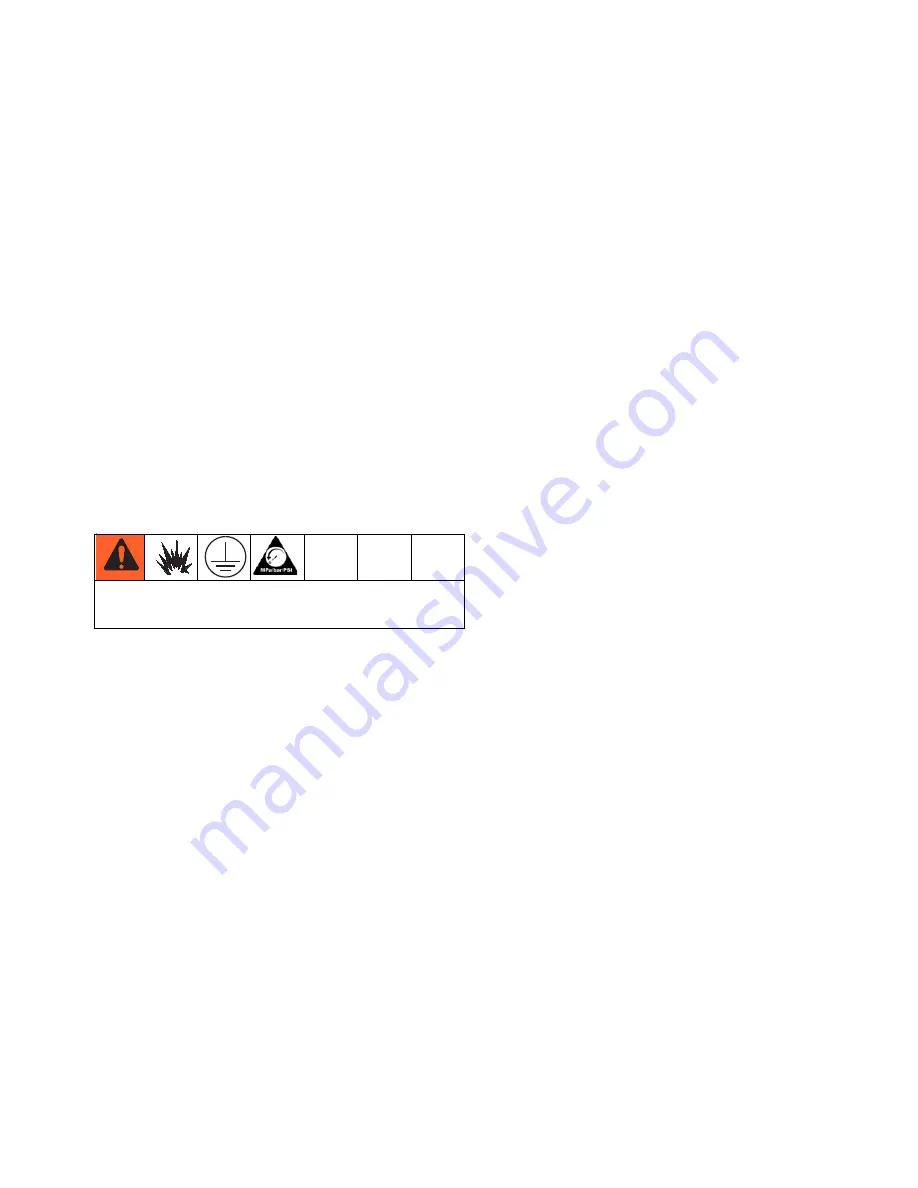
Maintenance
312795K
15
Maintenance
Preventive Maintenance
Schedule
The operating conditions of your particular system
determine how often maintenance is required. Establish
a preventive maintenance schedule by recording when
and what kind of maintenance is needed, and then
determine a regular schedule for checking your system.
Tighten Threaded Connections
Before each use, check all hoses for wear or damage.
Replace as necessary. Check that all threaded connec-
tions are tight and leak-free.
Flushing
Flush the pump:
•
Before first use
•
When changing colors or fluids
•
Before repairing equipment
•
Before fluid dries or settles out in a dormant pump
(check the pot life of catalyzed fluids)
•
At the end of the day
•
Before storing the pump.
Flush at the lowest pressure possible. Flush with a fluid
that is compatible with the fluid you are pumping and
with the wetted parts in your system. Check with your
fluid manufacturer or supplier for recommended flushing
fluids and flushing frequency.
1.
Follow Pressure Relief Procedure, page 13.
2.
Remove tip guard and spray tip from gun. Refer to
separate gun manual.
3.
Place siphon tube in grounded metal pail containing
cleaning fluid.
4.
Set pump to lowest possible fluid pressure, and start
pump.
5.
Hold a metal part of the gun firmly to a grounded
metal pail.
6.
Trigger gun. Flush system until clear solvent flows
from gun.
7.
Follow Pressure Relief Procedure, page 13.
8.
Clean the tip guard, spray tip, and fluid filter element
separately, then reinstall them.
9.
Clean inside and outside of suction tube.
Read all Warnings. Follow all Grounding instruc-
tions. See page 11.