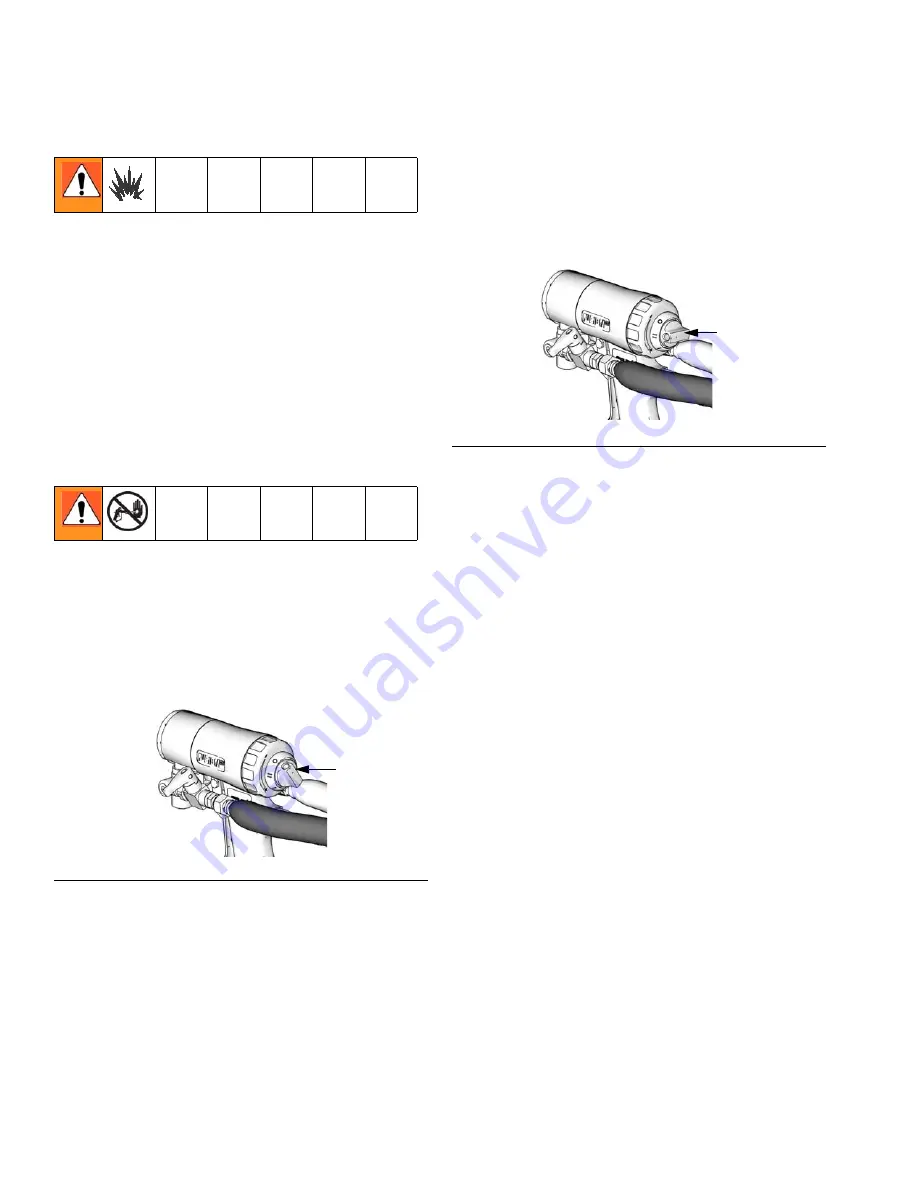
Grounding
12
312666P
Grounding
Check your local electrical code and propor-
tioner manual for detailed grounding instruc-
tions.
Ground the spray gun through connection to a
Graco-approved grounded fluid supply hose.
Piston Safety Lock
Engage piston safety lock whenever you stop
spraying to avoid accidental triggering.
Engage
To engage piston safety lock, push knob in and
turn clockwise. If engaged, gun will not actu-
ate.
Disengage
To disengage piston safety lock, push knob in
and turn counterclockwise until it pops out.
There will be a gap between knob and gun
body.
F
IG
. 2
Engaged
TI11326a
F
IG
. 3
Disengaged
TI12240a
Summary of Contents for Fusion CS00F1
Page 22: ...Variable Flow 22 312666P...