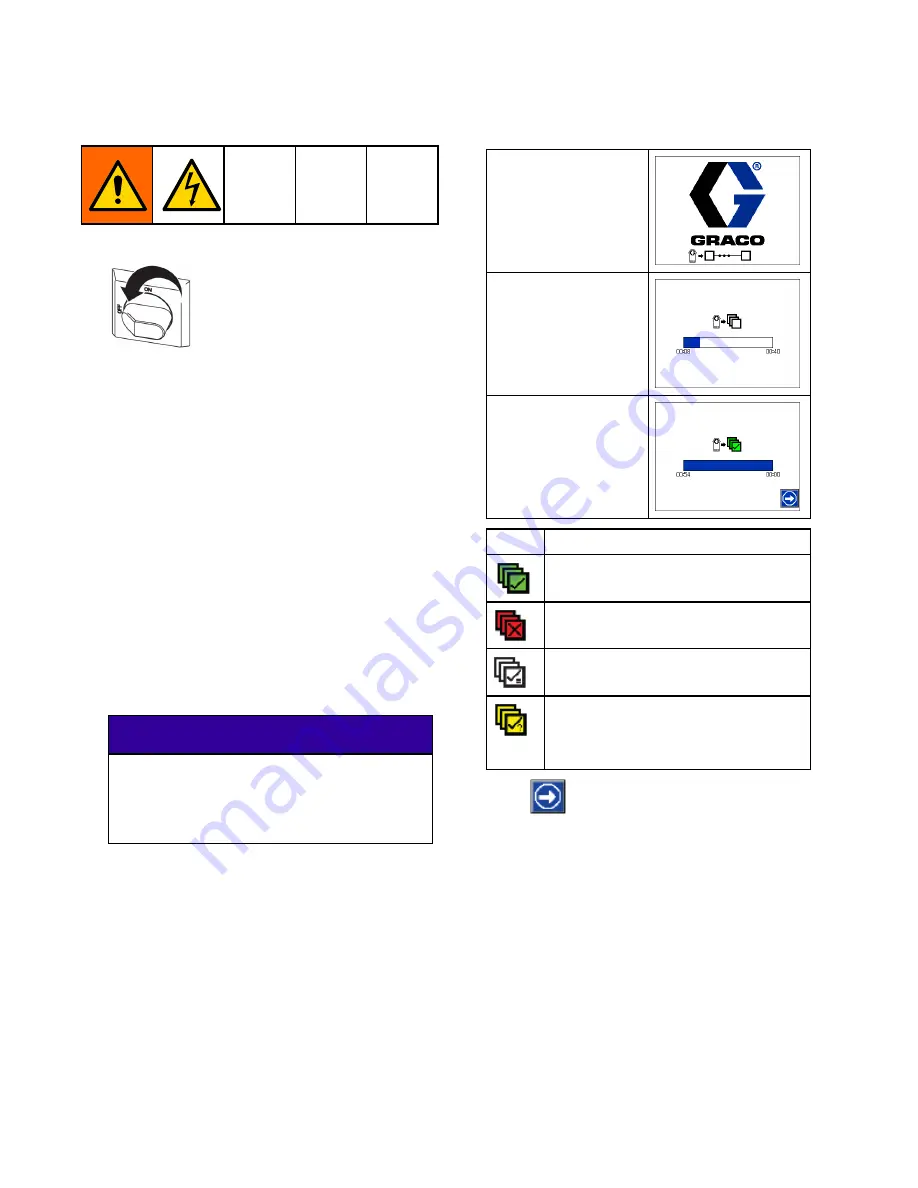
Update
Update
Update ADM
ADM
ADM Software
Software
Software
1. Turn the main power switch OFF.
2. Open the top and bottom door latches to the
electric cabinet.
3. Open the electrical cabinet. Use a Phillips
screwdriver to loosen the four ADM
mounting screws on the inside of the cabinet
door.
4. Lift the ADM up and pull it away from the
Reactor to unseat the mounting screws. For
easy reassembly, leave the loosened screws
attached to the ADM.
5. Remove the token access panel on the back
of the ADM.
6. Insert and press the software upgrade token
firmly into the slot.
NOTE:
NOTE:
NOTE: There is no preferred orientation of
the token.
7. Close the electrical cabinet.
8. Turn the main power switch ON.
NOTICE
NOTICE
NOTICE
A status is shown while software is
updating to indicate progress. To prevent
corrupting the software load, do not
remove the token until the status screen
disappears.
NOTE:
NOTE:
NOTE: When the ADM display turns on, you
may see the following screens:
First:
First:
First:
Software is checking
which modules will
take the available
updates.
Second:
Second:
Second:
Status of the
update with
approximate time
until completion.
Third:
Third:
Third:
Updates are
compete. Icon
indicates update
success/failure. See
the following table.
Icon
Icon
Icon
Description
Description
Description
Update successful
Update unsuccessful
Update complete, no changes
necessary
Modules were updated or did
not require an update; however,
one or more modules need to be
updated manually with a token.
9. Press
to continue to the operation
screen.
10. Turn the main power switch OFF.
11. Remove the software update token.
12. Replace the token access panel.
13. Open the electrical cabinet, remount the
ADM, and fully tighten the four mounting
screws.
14. Close the lock and the cabinet door with the
door latches.
74
334946J