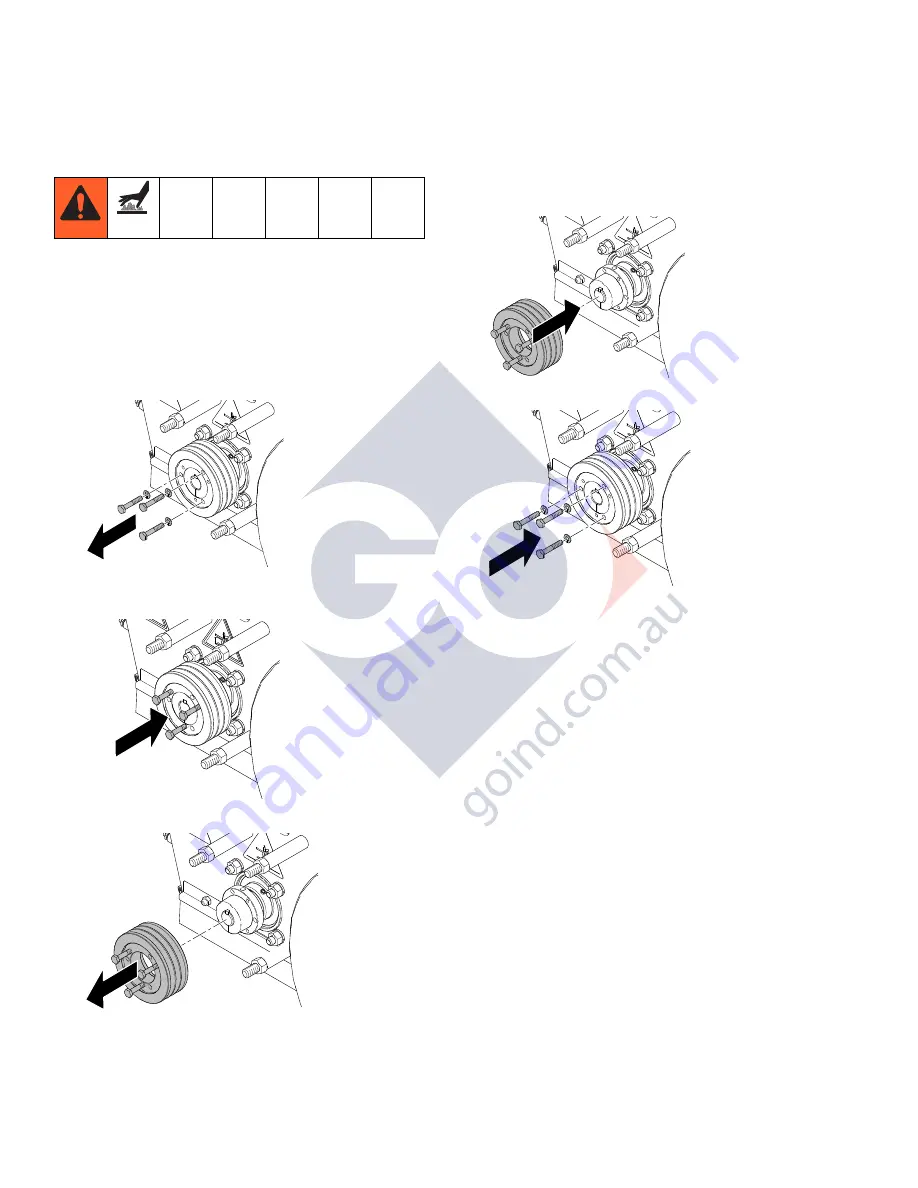
Pulley Replacement
12
3A0102D
Pulley Replacement
Removal
1. Remove drum (see
Drum Replacement
, page 6).
2. Remove belt guard and belt (see
Belt Replace-
ment
, page 9).
3. Remove three belt pulley screws and washers.
4. Insert three screws into pulley removal holes.
Evenly tighten screws and slowly remove pulley.
5. Remove pulley.
Installation
6. Install pulley onto hex shaft.
7. Insert three pulley screws and washers.
8. Replace belt guard and belt (see
Belt Replace-
ment
, page 9).
9. Replace drum (see
Drum Replacement
, page 6).
ti15122a
ti15121a
ti15126a
ti15131a
ti15127a
Summary of Contents for 571002
Page 39: ...Notes 39 3A0102D Notes ...