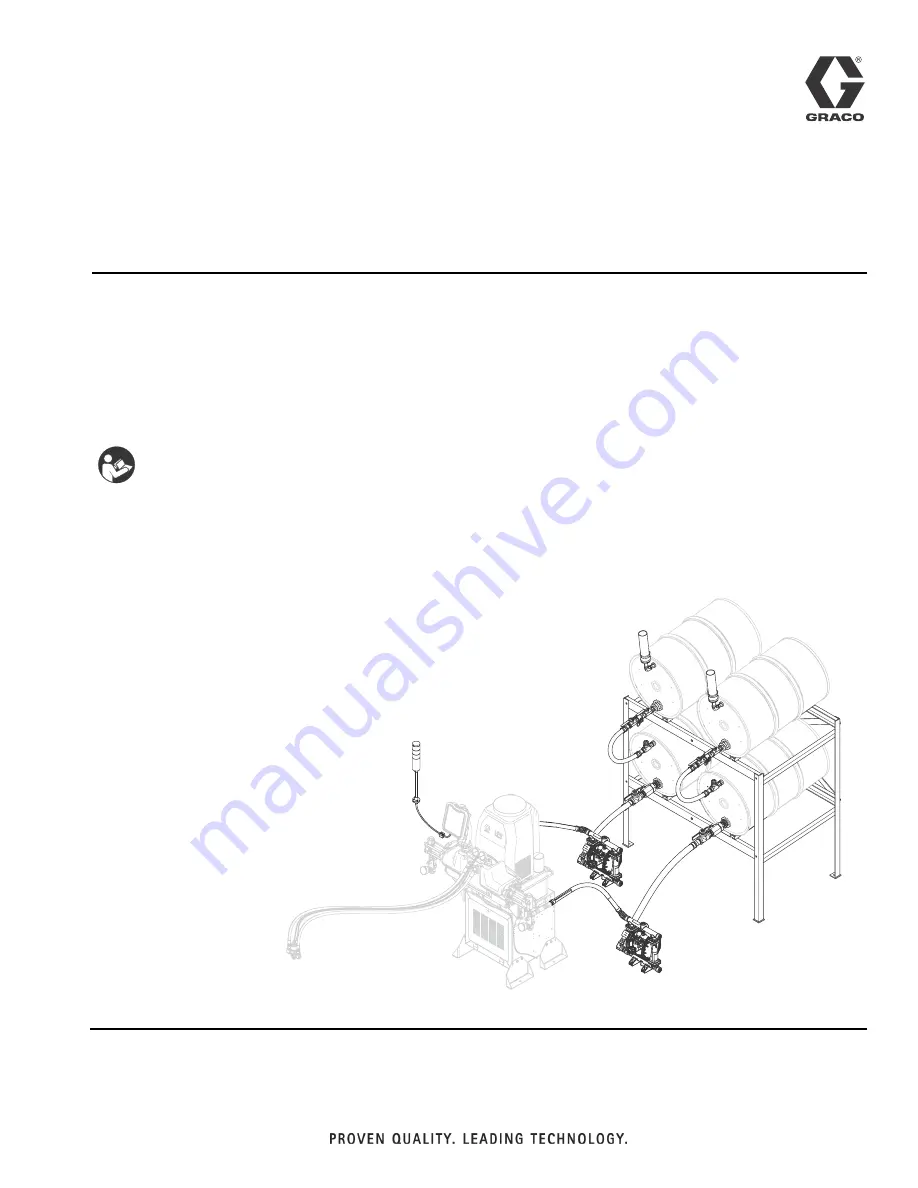
Instructions - Parts
Level Detection Module
and Drum Feed Kit
3A2806A
EN
Installation kit to provide low level sensors in both chemical sides of an HFRL
plural-component proportioner being fed from 55 gallon (208 liter) drums. For professional
use only.
Not approved for use in explosive atmospheres or hazardous locations.
See page 3 for model information.
125 psi (0.86 MPa, 8.6 bar) Maximum Fluid Working Pressure
125 psi (0.86 MPa, 8.6 bar) Maximum Air Input Pressure
Important Safety Instructions
Read all warnings and instructions in the HFRL and HFRS
Setup-Operations manual. Save all instructions.
ti19596a