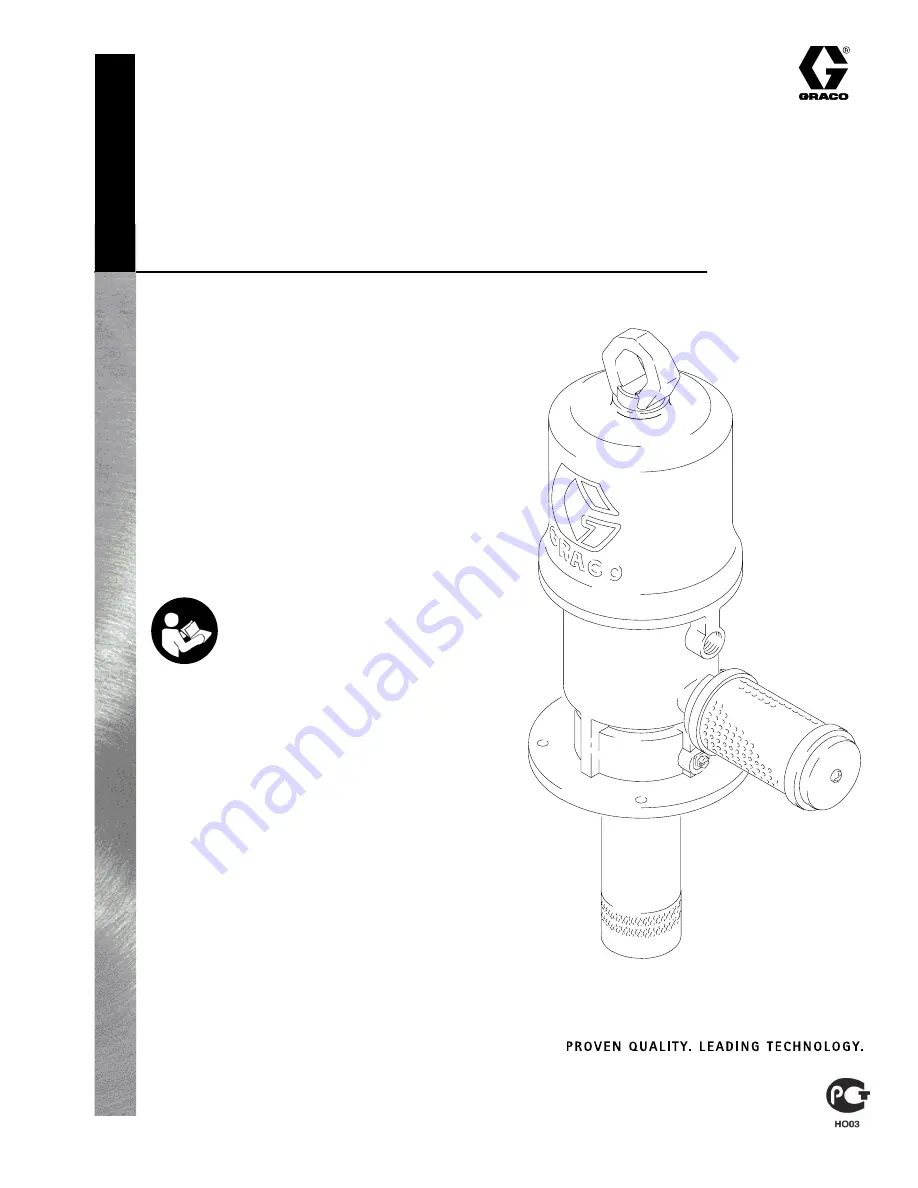
Instructions – Parts List
GRACO INC.P.O. BOX 1441MINNEAPOLIS, MN55440-1441
Copyright 1995, Graco Inc. is registered to I.S. EN ISO 9001
6:1 Fire–Ball
r
425 Pump
For pumping non–corrosive and
non–abrasive oils and lubricants only.
Model 238108, Series D
1100 psi (7.6MPa, 76 bar) Maximum Working Pressure
180 psi (1.2 MPa, 12 bar) Maximum Air Input Pressure
308608K
06031
Important Safety instructions
Read all warnings and instructions in this manual.
Save these instructions.