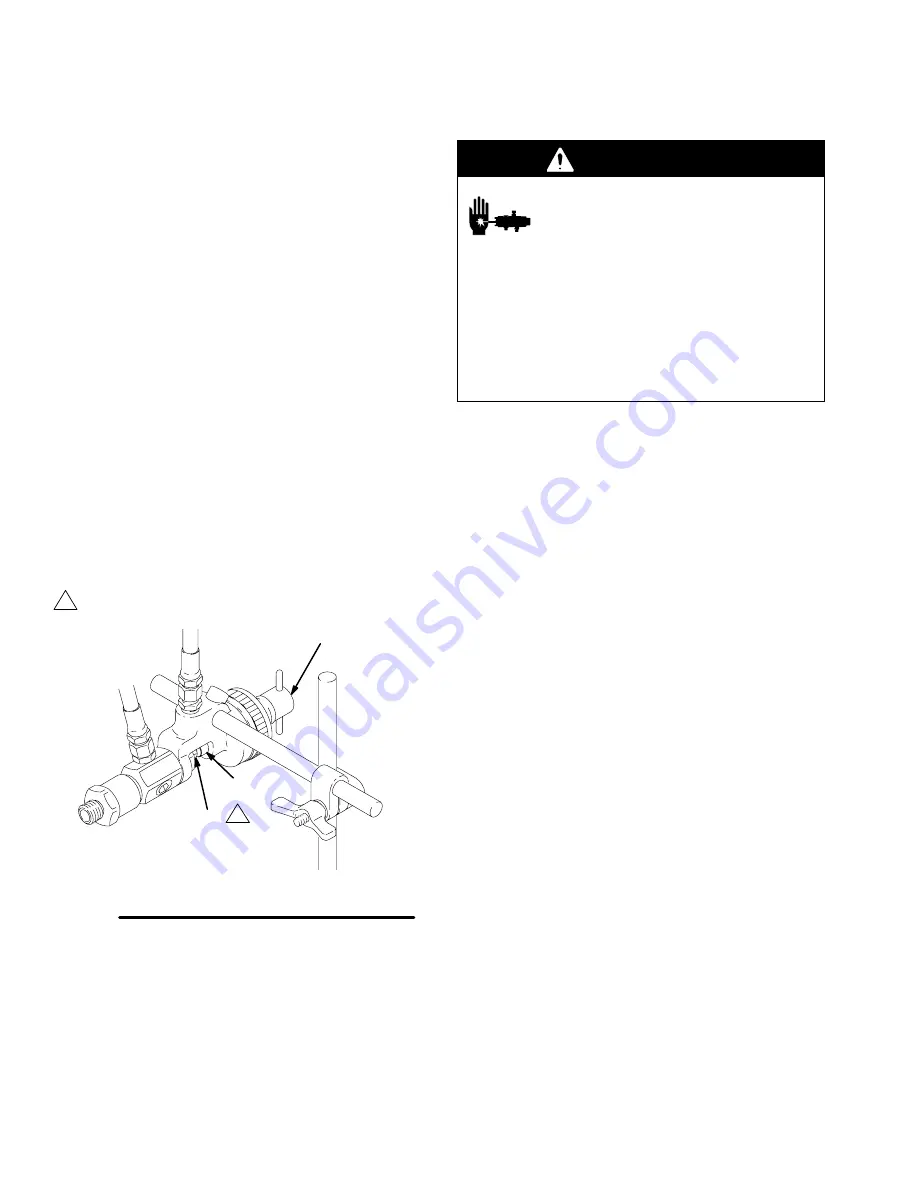
8
306715
Operation
Settings and Adjustments
Before each day’s operation, lubricate the exposed
portion of the needle (22) and the piston (16) with a
lubricant compatible with the fluid being dispensed.
After lubrication, cover the exposed portions of the
needle and piston with a piece of plastic to prevent
fluid buildup on these parts. Any buildup could damage
the valve packing (9 or 20). See Fig. 3.
Set the actuating air to at least 50 psi (345 kPa, 3.4
bar) and start the pump. Adjust the pump speed and
pressure to obtain the desired flow rate. Always use
the lowest pump speed necessary to get the results
you want.
To decrease needle travel, turn the adjusting screw
(12) clockwise; to increase, turn counterclockwise. If
the valve leaks from the outlet after it is closed, turn
the adjusting screw clockwise until the valve stops
leaking.
In a circulating system, adjust the back pressure valve
to provide constant system back pressure for all dis-
pensing valves while maintaining the proper pressure
for fluid circulation. See the
Typical Installation
on
page 6.
Fig. 2
06482
16
22
Model 207440 Shown
1
1
Oil Daily
12
Pressure Relief Procedure
WARNING
INJECTION HAZARD
Fluid under high pressure can be in-
jected through the skin and cause
serious injury. To reduce the risk of an
injury from injection, splashing fluid, or moving
parts, follow the
Pressure Relief Procedure
whenever you:
D
are instructed to relieve the pressure,
D
stop dispensing,
D
check or service any of the system equipment,
D
or install or clean the nozzle.
1.
Shut off the power to the pump.
2.
Close the bleed-type master air valve (required
with air powered pumps).
3.
Actuate the dispensing valve to relieve pressure.
4.
Open the pump drain valve (required in your
system) to help relieve fluid pressure in the dis-
placement pump. Actuating the dispensing valve to
relieve pressure may not be sufficient. Have a
container ready to catch the drainage.
5.
Leave the drain valve(s) open until you are ready
to dispense again.
If you suspect that the dispensing valve or hose is
completely clogged, or that pressure has not been fully
relieved after following the steps above, very slowly
loosen the hose end coupling and relieve pressure
gradually, then loosen completely. Now clear the valve
or hose.
Summary of Contents for 205435
Page 14: ...14 306715 Notes ...