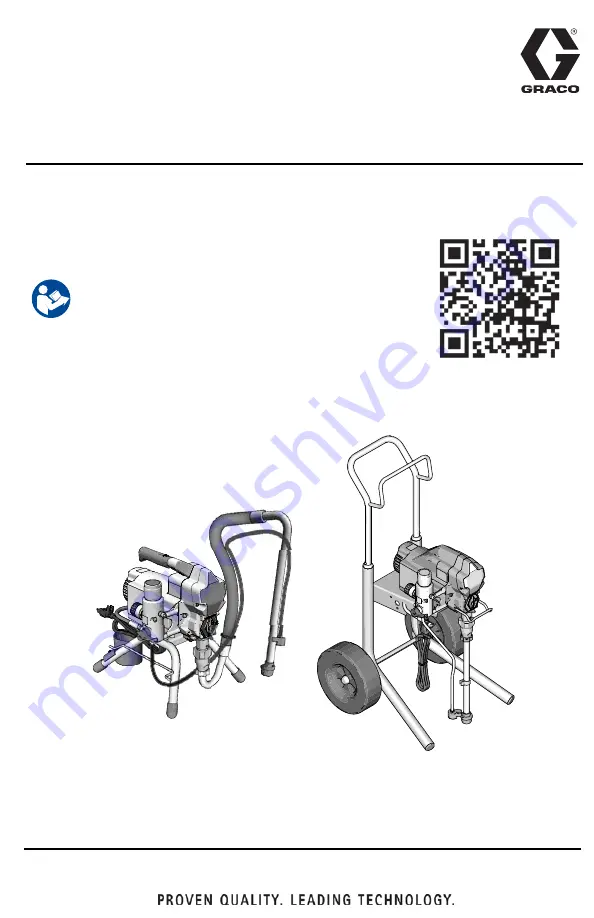
334659G
EN
Operation, Parts
210 ES Electric
Airless Sprayers
For professional use only.
Not approved for use in explosive atmospheres or hazardous locations.
For portable airless spraying of architectural paints and coatings.
Models: 17D163, 17C305
3000 psi (207 bar, 20.7 MPa) Maximum Working Pressure
Important Safety Instructions
Read all warnings and instructions in this manual and
related manuals. Be familiar with the controls and the
proper usage of the equipment. Save these instructions.
Related Manuals
Gun – 312830 (SG3)
Pump – 334599
ti25464a
17D163
17C305
Use only genuine Graco replacement parts.
The use of non-Graco replacement parts may void warranty
.
Scan QR code or click on link for
operational video.