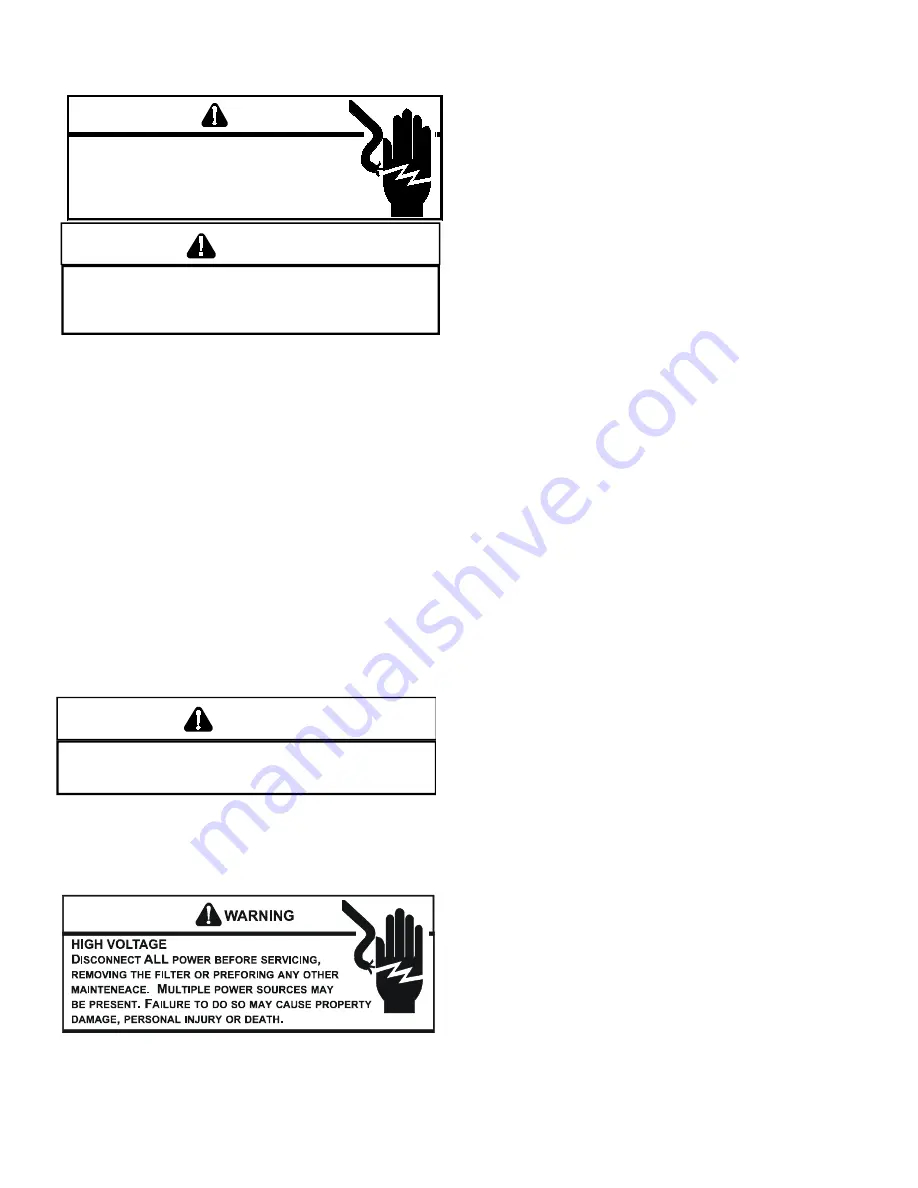
SCHEDULED MAINTENANCE
13
WARNING
H
I
GH
V
OLTAG
E
D
IS
CONN
E
CT
ALL
PO
WER
B
E
FO
RE
SERVI
C
I
NG O
R
I
N
S
TALL
I
NG TH
IS
U
N
I
T.
M
U
LT
I
PL
E
PO
WER
S
O
UR
C
ES
M
AY
B
E
P
RESE
NT.
F
A
I
L
URE
TO DO
S
O
M
AY CA
USE
P
R
OP
ER
TY
DA
M
AG
E
, P
ERS
ONAL
I
N
JUR
Y O
R
D
E
ATH.
I
F YO
U
MUS
T HANDL
E
TH
E
I
TN
I
TO
R
, HANDL
E
WI
TH CA
RE
.
T
O
U
CH
I
NG
TH
E
I
GN
I
TO
R
BODY
WI
TH BA
RE
F
I
NG
ERS
,
R
O
U
GH HANDL
I
NG, O
R
VI
B
R
AT
I
ON CO
U
LD
RESU
LT
I
N
E
A
R
LY
I
GN
I
TO
R
FA
I
L
URE
.
O
NLY A
QU
AL
I
F
IE
D
SERVI
C
ER
S
HO
U
LD
EVER
HANDL
E
TH
E
I
GN
I
TO
R
.
CAUTION
ANNUAL INSPECTION
The furnace should be inspected by a qualified installer, or
service agency at least once per year. This check should be
performed at the beginning of the heating season. This will
ensure that all furnace components are in proper working
order and that the heating system functions appropriately. Pay
particular attention to the following items. Repair or service
as necessary.
•
Flue pipe system. Check for blockage and/or leakage.
Check the outside termination and the connections at
and internal to the furnace.
•
Heat exchanger. Check for corrosion and/or buildup
within the heat exchanger passageways.
•
Burners. Check for proper ignition and flame sense.
•
Wiring. Verify that electrical connections are tight and
free from corrossion.
•
Filters.
AIR FILTER
N
EVER
OP
ER
AT
E
F
UR
NAC
E
WI
HTO
U
T A F
I
LT
ER
I
N
S
TALL
E
D A
S
D
US
T
AND L
I
NT
WI
LL B
UI
LD
U
P ON
I
NT
ER
NAL PA
R
T
S
RESU
LT
I
NG
I
N LO
SS
OF
E
FF
I
C
IE
NCY,
EQUI
P
ME
NT DA
M
A
M
G
E
, AND PO
SSI
BL
E
F
IRE
.
WARNING
Filters must be used with this furnace. Filters do not ship
with these furnaces but must be provided by the installer for
proper furnace operation.
Dirty filters are the most common cause of inadequate heating
or cooling performance.
Maintenance
Improper filter maintenance is the most common cause of
inadequate heating or cooling performance. Filters should
be cleaned (permanent) or replaced (disposable) every two
months or as required.
Horizontal Unit Filter Removal
Filters in horizontal installations are located in the central
return register.
INDUCED DRAFT AND CIRCULATION BLOWERS
The bearings in the induced draft blower and circulator blower
motors are permanently lubricated by the manufacturer. No
further lubrication is required. Check motor windings for
accumulation of dust which may cause overheating. Clean
as necessary.
FLAME SENSOR (QUALIFIED SERVICER ONLY)
Under some conditions, the fuel or air supply can create a
nearly invisible coating on the flame sensor. This coating acts
as an insulator, causing a drop in the flame sensing signal. If
this occurs, a qualified servicer must carefully clean the flame
sensor with steel wool. After cleaning, the flame sensor output
should be as listed on the specification sheet.
The following is a must for every service technician and
service shop.
1. Dial type thermometers or thermocouple meter (option-
al) - to measure dry bulb temperature.
2. Amprobe - to measure amperage and voltage.
3. Volt-Ohm Meter - testing continuity, capacitors, and
motor windings.
4. Inclined Manometer - to measure static pressure, pres-
sure drop across coils, filters, and draft.
5. Water Manometer (12”) - to test gas inlet and manifold
pressure.
Other recording type instruments can be essential in solving
abnormal problems, however, in many instances they may
be rented from local sources.
Proper equipment promotes faster, more efficient service and
accurate repairs resulting in fewer call backs.
HEATING PERFORMANCE TEST
Before attempting to diagnose an operating fault code, run
a Heating Performance Test to determine if the heating
system is performing within 5% of the BTU input found on
the rating plate of the unit being tested. To conduct a heating
performance test, the BTU input to the unit must be calculated
(see Clocking a Gas Meter). Before clocking a gas meter,
contact your local utility to provide the caloric value (BTU
content) of the natural gas in the area.
It is also important to confirm the airflow (CFM) is within the
temperature rise range (see Airflow Data in spec sheet) and
external static pressure range (approximately 0.5” water
column). How-to instructions can be found in the service
manual under Checking External Static Pressure and
Checking Temperature Rise.
Summary of Contents for AMES960403BU AA
Page 25: ...TROUBLESHOOTING 25...
Page 26: ...TROUBLESHOOTING 26...