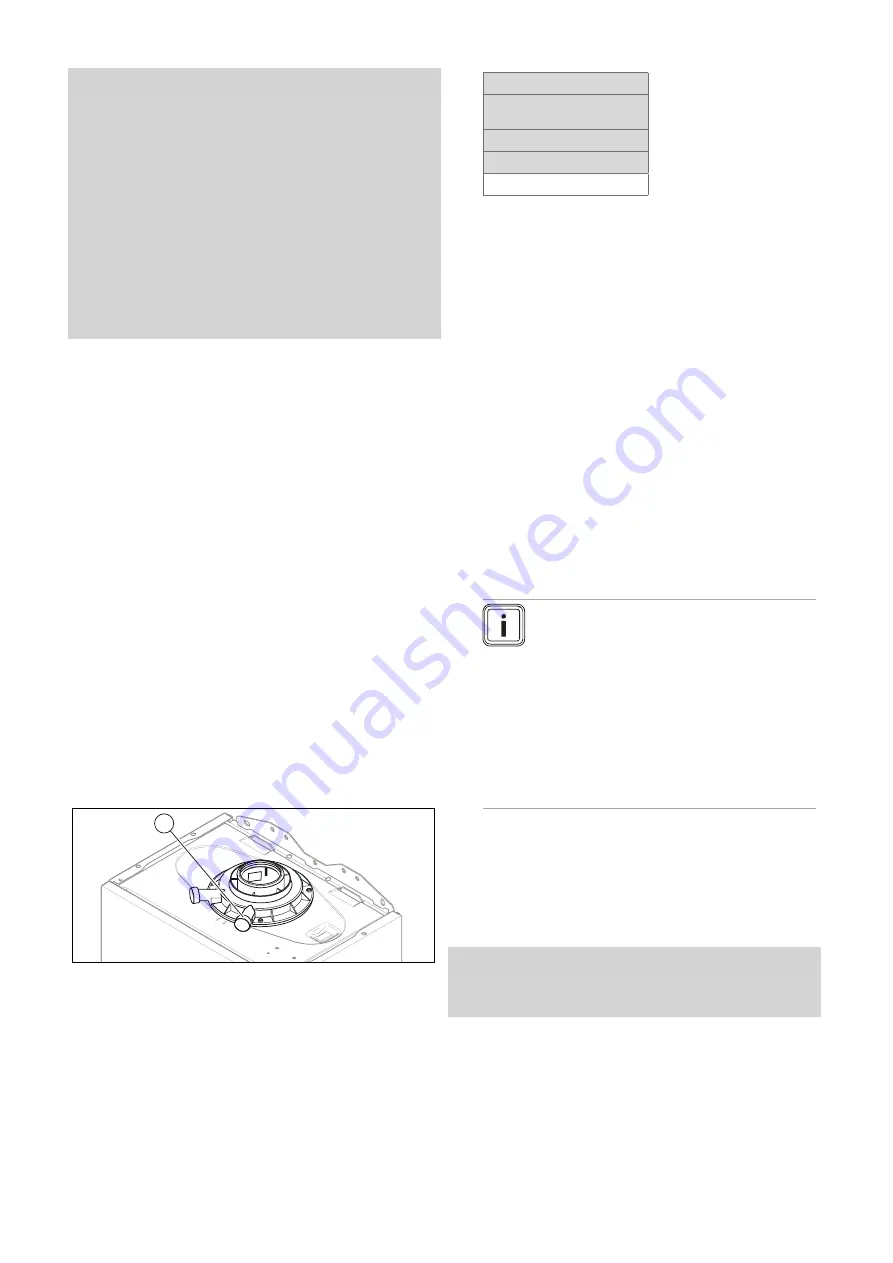
Start-up 9
0020300875_01 Energy
7
Installation and maintenance instructions
33
Condition
: Gas flow pressure
in the
permissible range
▶
End the check programme
P.01
.
▶
Allow the boiler to cool down allowing pump overrun to
operate for a minimum of two minutes.
▶
Close the gas stopcock
(1)
.
▶
Remove the pressure gauge and retighten the sealing
screw
(2)
for the measuring nipple.
▶
Open the gas stopcock
(1)
.
▶
Check the test nipple for gas tightness.
▶
Install the front casing. (
▶
Reset boiler controls for normal operation.
▶
Record the appliance gas inlet working pressure (kPa
resp. mbar) in the Benchmark gas boiler commissioning
checklist.
9.11.3 Checking the air/flue pipe/flue gas
recirculation
1.
Check the flue gas installation is intact in accordance
with the latest gas safe technical bulletin and informa-
tion supplied in the installation instructions.
2.
For extended flue gas installations check for flue gas
recirculation using the air analysis point.
3.
Use a flue gas analyser.
4.
If you discover unusual levels of CO or CO
2
in the sup-
ply air, search for the leak in the flue system or for signs
of flue gas recirculation.
5.
Eliminate the damage properly.
6.
Check again whether the supply air contains any un-
usual levels of CO or CO
2
.
7.
If you cannot eliminate the damage, do not start up the
product.
9.11.4 Checking the CO
₂
content
1.
Start up the product with the check programme
(P.01)
and set the value.
–
Setting value for the programme P.01: 100
Check programmes
–
Overview
2.
Wait until the value that is read is stable.
–
Waiting period for reading a stable value: 5 min
1
3.
Unscrew the cover from the flue gas analysis point
(1)
.
4.
Measure the CO
₂
content at the flue gas analysis point
(1)
.
5.
Compare the measured value with the corresponding
value in the table.
Great Britain and Ireland
Removed front casing /
installed front casing
Natural gas
H
9.2
±
1%
◁
The value is OK.
▽
The value is not OK; you cannot start up the
product.
▶
Inform Customer Service.
9.12
Thoroughly flushing the heating installation
("hot")
1.
Operate the appliance until the boiler and the heating
system are up to temperature.
2.
Check the heating system for leaks.
3.
Connect a hose to the drain valve located at the lowest
position of the heating system.
4.
Shut off the boiler, open the drain valve and all purge
valves on the radiators and allow the water to flow out
of the heating system and the boiler quickly and fully.
5.
Close the drain valve.
6.
Fill the heating system again with water as described in
Filling the heating installation and Purging the heating
installation.
7.
Re-fill the system until the system design pressure of
0,1 MPa (1,0 bar) is attained.
Note
The actual reading on the digital pressure
gauge should ideally be 0,05 MPa (0,5 bar)
plus an additional pressure corresponding
to the highest point of the system above the
base of the boiler
–
10 m head equals an ad-
ditional 1 bar reading on the pressure gauge.
The minimum pressure should not be less
than 0,1 MPa (1 bar) in any installation. If
the system is to be treated with an inhibitor it
should be applied at this stage in accordance
with the manufacturer’s instructions
8.
Install the front casing.
9.13
Checking leak-tightness
▶
Check the gas pipe, the heating circuit and the hot water
circuit for leak-tightness.
▶
Check that the air/flue pipe has been installed correctly.
Condition
: Room-sealed operation
▶
Check whether the vacuum chamber has been closed
tightly.
9.13.1 Checking the heating mode
1.
Activate the heating mode on the user interface.
2.
Turn all thermostatic valves on the radiators until they
are fully open.
3.
Allow the product to operate for at least 15 minutes.
4.
Fill and purge the heating installation. (