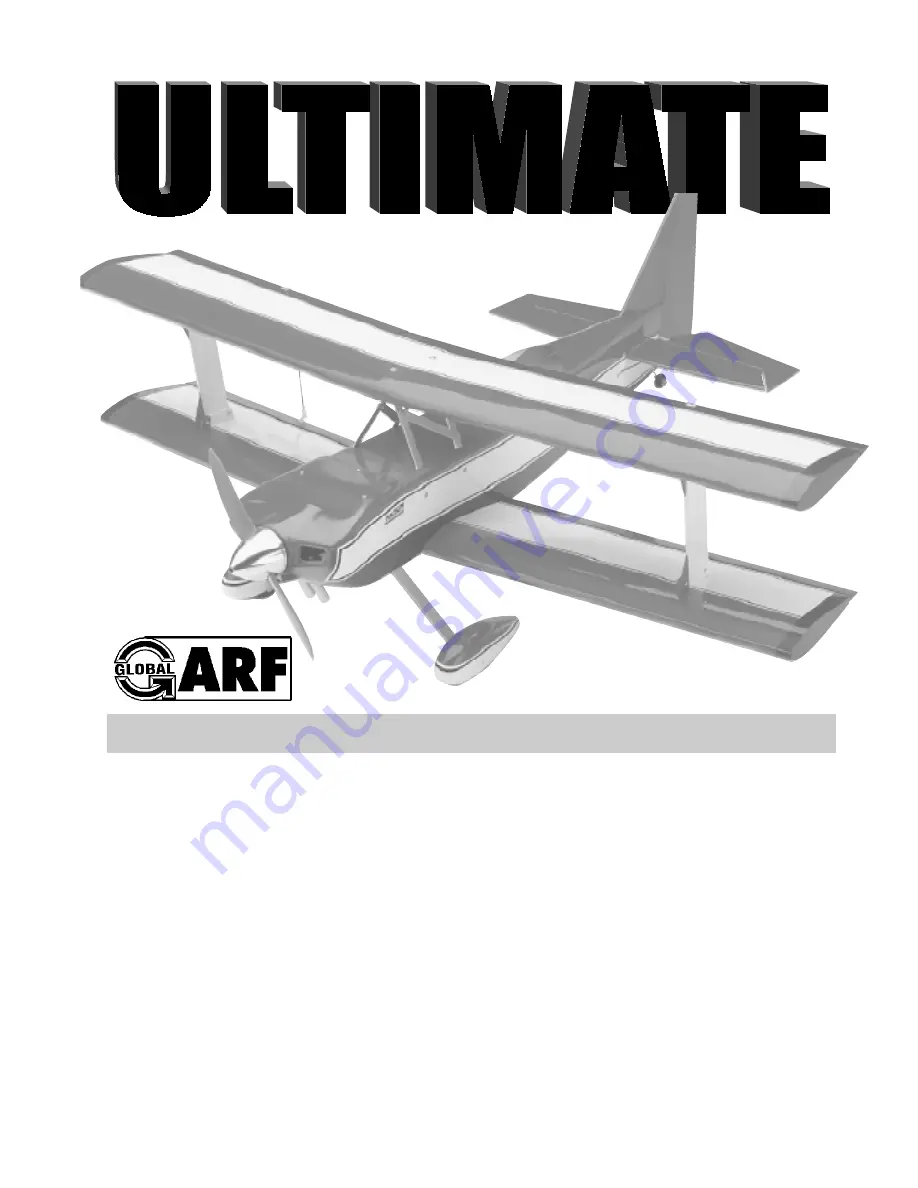
1
Instructions for Final Assembly
Would you like to fly your own Ultimate Biplane? Do you want to be flying in a weekend?
Are you ready for an aerobatic 46 size performance biplane? Then you’ve chosen wisely.
The Global ARF Ultimate was made for you. Features like an all balsa and plywood built up
airframe, just like you'd do it yourself from a kit. A generous tail section combined with a
long fuselage moment and swept wings make this an aerobatic performer that you'll always
want to fly. A super strong metal wing center cabane system with outer plywood interplane
struts hold everything together when you're performing snap rolls and inverted spins. To go
along with this we've provided a prepainted four color cowling, prepainted wheel pants and
a clear molded canopy. There is no other aerobatic biplane in it's class that is easier to
assemble or that flys better. We know you’ll enjoy building the Ultimate, but you bought this
airplane to fly. And that's what it does best. Set up for sport flying, it’s predictable and
tracks like it's on rails. Deceivingly easy to fly, change the set-up parameters and you’ll
push the envelope like an experienced airshow performer. Complete inverted flat spins and
torque rolls like you’ve never performed before!
Version V1.0
3-99
Kit # 123820
All Contents © Copyright 1999
.46 SIZE AEROBATIC ARF PERFORMANCE BIPLANE
.46 SIZE AEROBATIC ARF PERFORMANCE BIPLANE
.46 SIZE AEROBATIC ARF PERFORMANCE BIPLANE
.46 SIZE AEROBATIC ARF PERFORMANCE BIPLANE
.46 SIZE AEROBATIC ARF PERFORMANCE BIPLANE