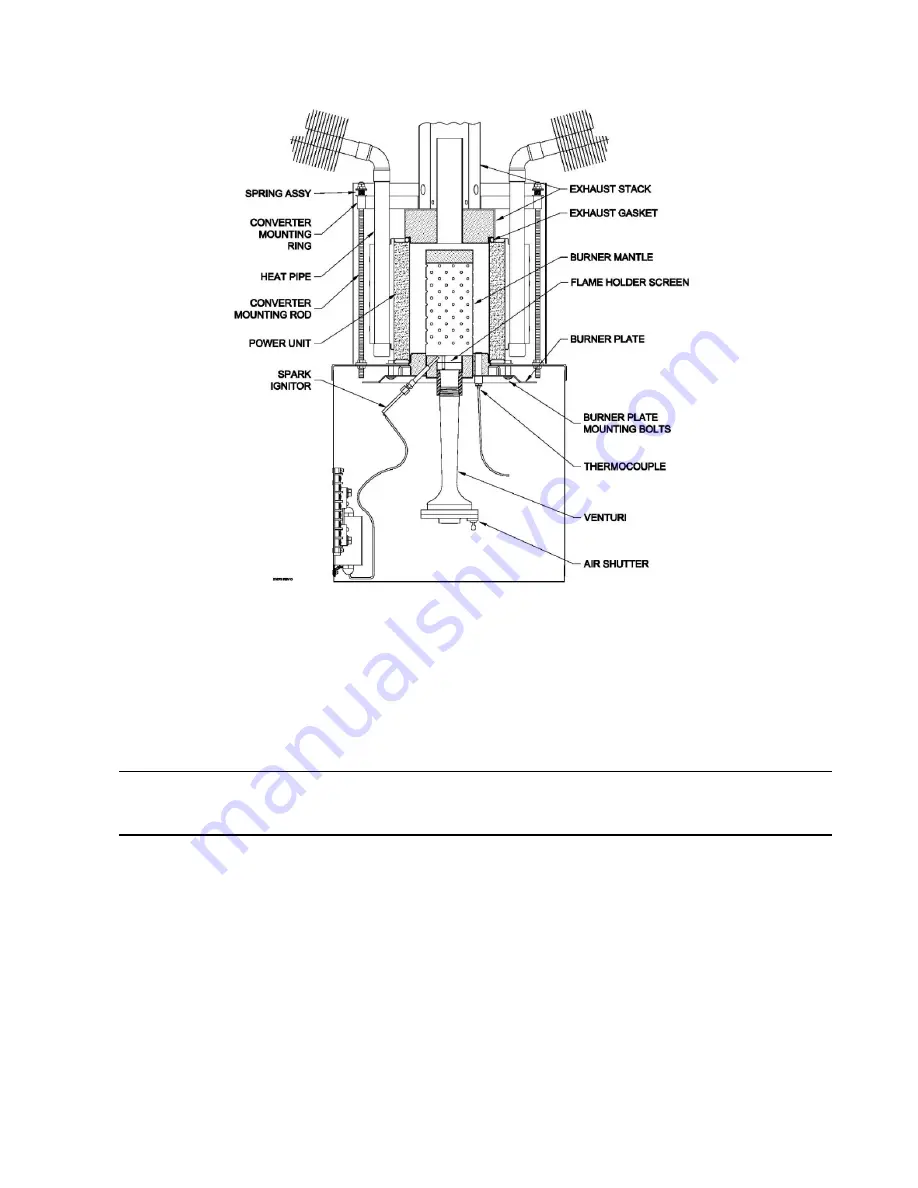
Global Power Technologies
SERVICE AND MAINTENANCE
05585 rev11 | Model 8550-SD
Page 29 of 53
Figure 15 – Burner System Components
With the burner plate assembly removed, examine the exhaust stack through the Power Unit,
remove any obstructions and check for corrosion.
If the exhaust stack is corroded, it must be replaced as follows:
1.
Remove the converter shroud which covers the lower portion of the heat pipes. This can be
accomplished without removing the heat pipe support frame.
NOTE: Turn off the fuel supply at the external valve before performing service checks on the
fuel system.
2.
Remove the four nut-and-spring assemblies that hold down the converter mounting ring.
Before removing the converter mounting ring, mark its position so that it can be reinstalled in the
same position.
3.
Lift the exhaust stack off.
Before replacing the exhaust stack, check if the high temperature exhaust gasket is still in good
condition and replace if necessary. To replace, t
ighten the spring assemblies that are holding the
converter mounting ring in place until the springs are solid, then back off by about 5 turns (1/4 inch
or 6 mm).
Always apply a high temperature nickel-based, anti-seize compound to the threads on the venturi
before installing it. It is not necessary to tighten the venturi more than hand tight.