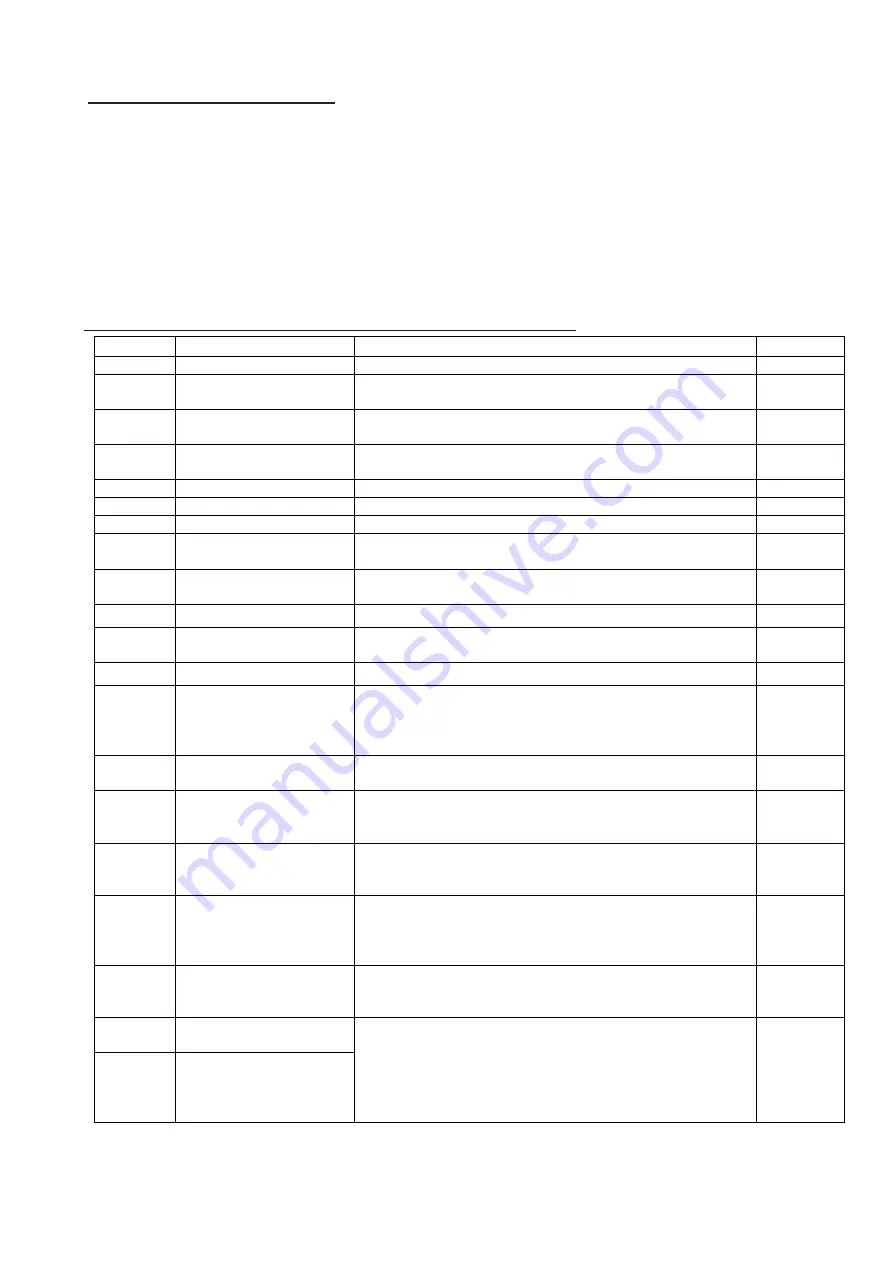
51
Setting the axis number (d0xxxx)
GSK driver you need to set the the axis number (1 to 30 decimal) in order to identify each axis.
Please set the following parameters to manipulate the case of a two-axis for the driver panel.
In the case of Axis 1: Write to set the axis number to d00177. (Same as 1-axis type driver)
In the case of Axis 2: Write to set the axis number to d10177.
Please set so as not to overlap with the driver axis number.
Please set the axis number to 0 (not used) or, if you do not want to connect the motor
in the two-axis type of driver.
7-2
(
d-00***, d-10***
)
Each-axis setting, driver parameter setting
Address
Name
Matter
unit
036
Speed limit
This sets the maximum value of the rotational speed.
rpm
064
method of return to origin
0: If you are detected using the LSW and the sensor
1: butting formula
―
065
Set position data after
the return to origin
Abutment formula: return amount homing
(LSW formula: set position after homing)
―
066
Homing
start direction
Starting rotary direction of homing operation
0: positive direction 1: negative direction
―
068
Homing speed
Speed to start the homing
rpm
069
Creep rate
Origin detection rate
rpm
070
Collision time
Butting time in the origin detection of abutment type
msec
071
Collision torque
Butting
torque
in the origin detection of abutment type
Please set as a percentage of the motor rated current
%
084
ID of the monitor 1
Data of the set ID is converted into an analog signal that it
‘s outputted from the M1 terminal.
―
085
Scale of the monitor 1
Output scaling of the monitor 1
―
086
ID of the monitor 2
Data of the set ID is converted into an analog signal that it
‘s outputted from the M2 terminal.
―
087
Scale of the monitor 2
Output scaling of the monitor 2
―
104
Detection current of
overload alarm
The alarm becomes overloaded when the average value of
the motor current exceeds the set value.
Setting value is set as a percentage of the motor rated
current.
%
105
Detection rate of
Acceleration alarm
The number of revolutions of the motor
rpm
142
Magnification of the
sensor resolution
It sets the resolution magnification of the sensor.
NR, positioning encoder, positioning resolver: 4
―
160
Gear abnormality
determination count
(continuous)
When the gear failure is detected, it will set the number of
times determined to the alarm.
―
161
Gear abnormality
determination count
(cumulative)
It sets the resolution of the sensor
NR: 256, Positioning resolver: 8192
Positioning encoder: 16384
NR2: 1024
―
163
Temporary tightening
torque-free monitoring
time
This sets the torque-free monitoring time of the
pre-tightening.
msec
165
Minimum gradient
determination value
It is judged to be abnormal when the gradient is less than
the value obtained by multiplying the value of -1 to be set
here.
Here you set the rapid torque change rate that it is
generated by a bolt
breakage
at the time of this tightening
end.
%
%
166
Bolt fracture criterion
value
Summary of Contents for GSK Series
Page 1: ...Instruction Manual GSK GSKW Controller November 2017 GIKEN INDUSTRIAL CO LTD The 3rd edition...
Page 16: ...15 Size Interface dimensions Standard type GSK IF...
Page 17: ...16 Controller dimensions Standard type GSK 4 GSKW 4...
Page 18: ...17 Controller dimensions Standard type GSK 5 7...
Page 19: ...18 Controller dimensions T type GSK T5 T7...
Page 20: ...19 Controller dimensions Standard type GSKW 5...
Page 21: ...20 Controller dimensions T type GSKW T5...
Page 22: ...21 Dimensions display Model GSK D1 Panel cut out dimensions Back Side Front Under...
Page 24: ...23 M net ver GSK Controller system wiring reference diagram...
Page 28: ...27 External connection diagram I F unit Connected equipment standard and T type...
Page 50: ...49 Setting...
Page 58: ...57 Reverse tightening reference waveform...
Page 62: ...61...
Page 63: ...62 Gradient calculation method...