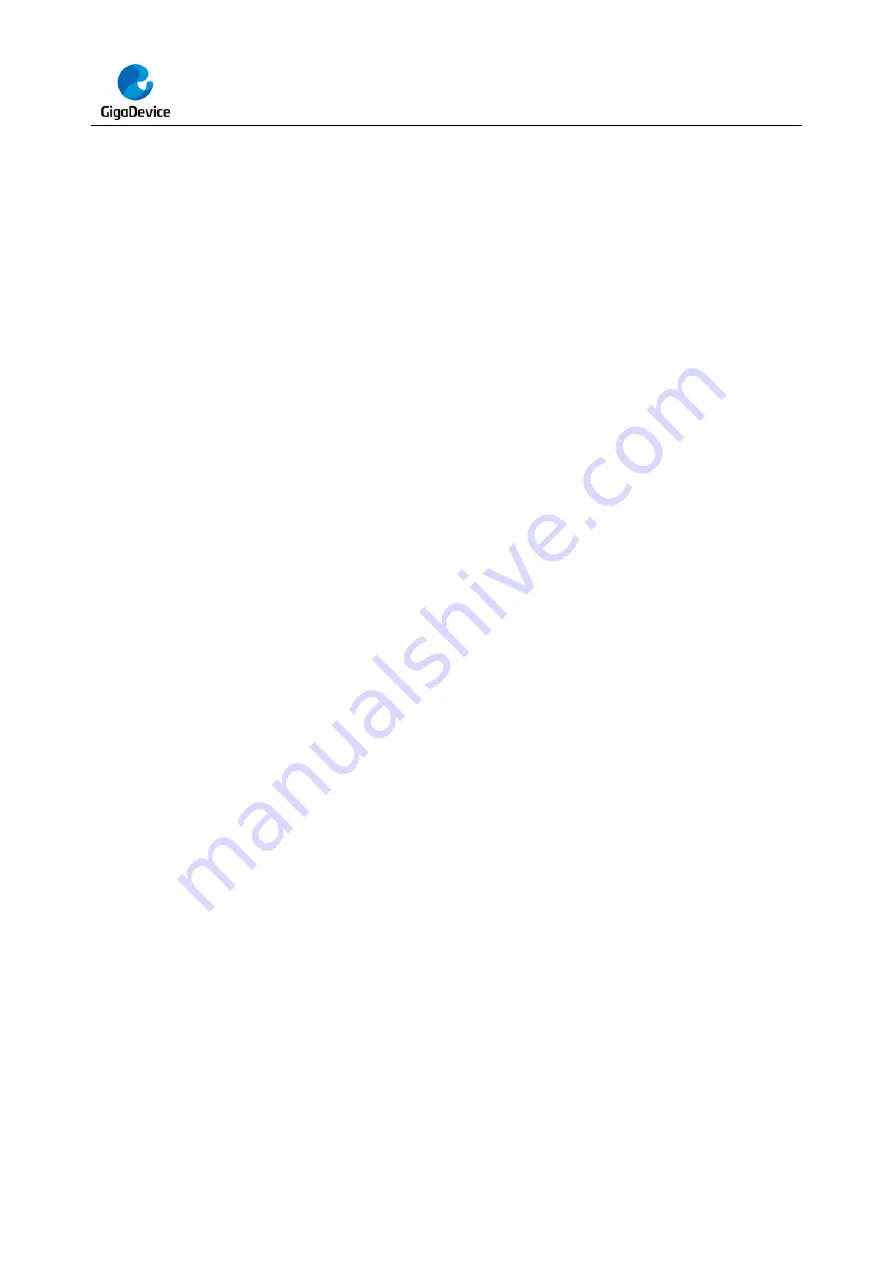
AN055
ESD Static Protection Manual
12
3.
Operating Precautions
3.1.
Guidelines
Avoid contaminating the pad surface before soldering. Anything that comes into contact with
these surfaces must be cleaned. Be very careful when removing the PCB from its protective
packaging. Only touch the edge of the board away from the edge connector. Gloves that meet
EOS/ESD requirements may be required when mechanical assembly requires a firm grip on
the board. The above principles are especially important when using a no-clean process.
During assembly and acceptability checks, care must always be taken to ensure product
integrity.
1.
Keep the workbench clean and tidy. There should be no food, beverages or tobacco in
the work area.
2.
Minimize hand-held chips or PCBs to prevent damage.
3.
Gloves need to be replaced in time to prevent contamination caused by glove stains.
4.
Do not touch PCB pads and chip pins or pads with bare hands or fingers. Human finger
grease and salt can reduce solderability, increase corrosion and solder dendrite growth,
and lead to poor adhesion of subsequent coatings or encapsulations.
5.
Do not use hand creams and hand sanitizers containing silicon components. Chemical
agents containing silicon components will cause solderability and coating adhesion
problems.
6.
The PCB test board or chip cannot be stacked. The stack is susceptible to physical
damage, delineate a specific assembly area in the test area, use specific ESD racks for
temporary storage.
7.
Even if there is no ESD mark on the chip and PCB packaging, the chip or PCB to be
operated should be the ESD sensitive device or component by default.
8.
Testers must be trained in ESD protection and follow appropriate ESD regulations and
procedures.
9.
For the mailing and transportation of ESD sensitive devices, appropriate ESD protective
packaging must be used, otherwise it cannot be packaged.
PCBs and common plastic chips have different levels of moisture absorption and release.
During the soldering process, heat accumulation causes moisture expansion, which can
damage the material and fail to meet the performance requirements of the product. This type
of damage is hidden damage, such as cracks, internal delamination, and popcorn phenomena,
which are difficult to observe with the naked eye, but occur during initial welding and rework
operations.
If the humidity of the environment is unknown, the PCB should be baked to reduce the internal
moisture and prevent the PCB from over-wetting the laminate. The selection of the baking
temperature and the baking time should be controlled during the baking process to prevent
the reduction of solderability due to the growth of intermetallic compounds, surface oxidation