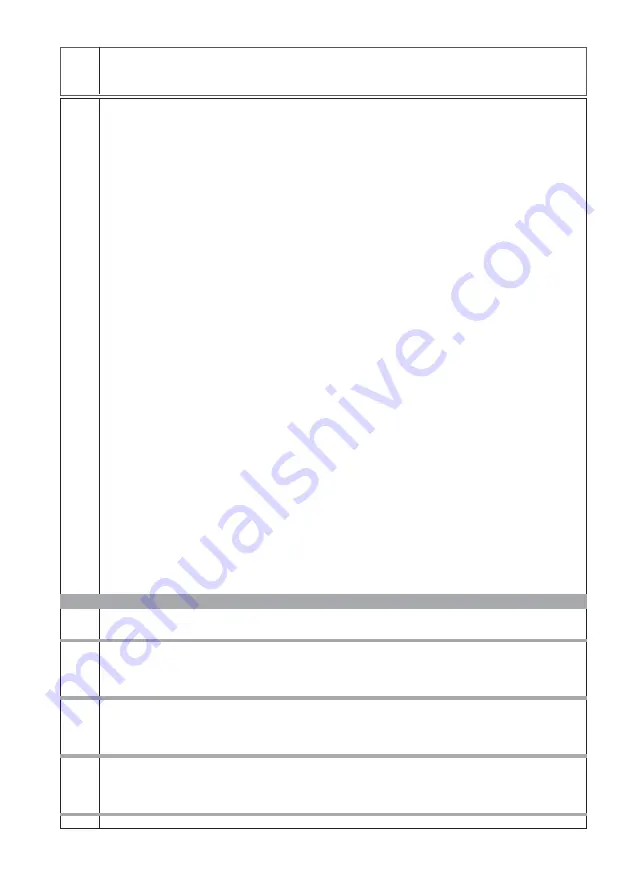
Index
MENU
MENU
MENU
MENU
MENU
[Unit] Access Default
Min/Max
Format Reg.Mode Level Ipa
Parameter Name
Description
ARTDrive V2 series - Instruction Manual
Chapter 6 Parameter • 303
By setting the source of
O06.05 - DiaClc start src
to one and if the Drive is enabled, the
procedure is started.
During this phase the parameters and the PI and PD regulators are disabled.
The regulation checks the signal coming from the dancer potentiometer.
If this value is higher than the one set in Max deviation, the motor starts rotating with the
speed reference set in Positioning spd in order to wind the material on the winder and to
bring the dancer into its central working position.
If the regulation checks that the signal coming from the dancer potentiometer is lower
than the value set in Max deviation, the motor starts rotating with the speed reference set
in Positioning spd in order to unwind the material and to bring the dancer to the point
identified by Max deviation.
At this point the reference is inverted till bringing the dancer in its central working
position.
When the dancer has reached its central position, the
O03.44 - PID PI out
parameter is
initialized with the value of the measured diameter.
The
Diacalc active
variable brings to a high logic level the
Diam Calc act
digital output,
stating the end of the diameter calculation phase.
Now, if the PI and/or PD blocks are enabled, the system reaches automatically
the regulation mode.
To this purpose the digital inputs programmed as
DiaClc start
for the PI and PD enable
are brought simultaneously to a high logic level.
The Diacalc active output signal can be used to reset the
DiaClc start
command (such
command is activated on the climbing leading edge of the digital input; for this reason it
has to be brought to a high level after power supplying the Drive regulation section and it
has to be reset when the starting calculation phase is over).
The value of
O03.44 - PID PI out
is calculated via the following formula:
PID PI out
= (Minimum diameter x
PI clamp top
) / value of the calculated diameter
The
O03.28 - PI clamp top
and
O03.28 - PI clamp bot
parameters of the PI controls
menu have to be set according to the maximum and minimum winder diameter.
O06 APPL CFG / DiamCalc
N
OTE
!
Menu accessible with Access Level = FULL.
O06.00 Max deviation
[%]
RWS
90
-200/200
PP
V-F-S-B
Full
7360
Position of maximum mechanical sealing for the dancer.
O06.01 Positioning spd
[%]
RWS
0.00
-200/200
PP
V-F-S-B
Full
7361
Positioning speed.
O06.02 Gear box ratio
NULL RWS
1.00
0.001/1.00
FK
V-F-S-B
Full
7362
Reduction ratio between motor and winder (<=1).
Summary of Contents for ARTDrive Vector V2 400Vac Series
Page 1: ...Instruction Manual ARTDrive ARTDrive Vector AC Drives V2 series 400Vac Class 575Vac Class...
Page 14: ...0 14 Chapter 0 Safety Precautions ARTDrive V2 series Instruction manual...
Page 40: ...40 Chapter 3 Installation Guidelines ARTDrive V2 series Instruction Manual...
Page 92: ...92 Chapter 5 Quick Start Up Guide ARTDrive V2 series Instruction Manual...
Page 358: ...358 Chapter 8 Appendix ARTDrive V2 series Instruction Manual...
Page 376: ...Chapter 9 Pick Lists 376 ARTDrive V2 series Instruction manual...