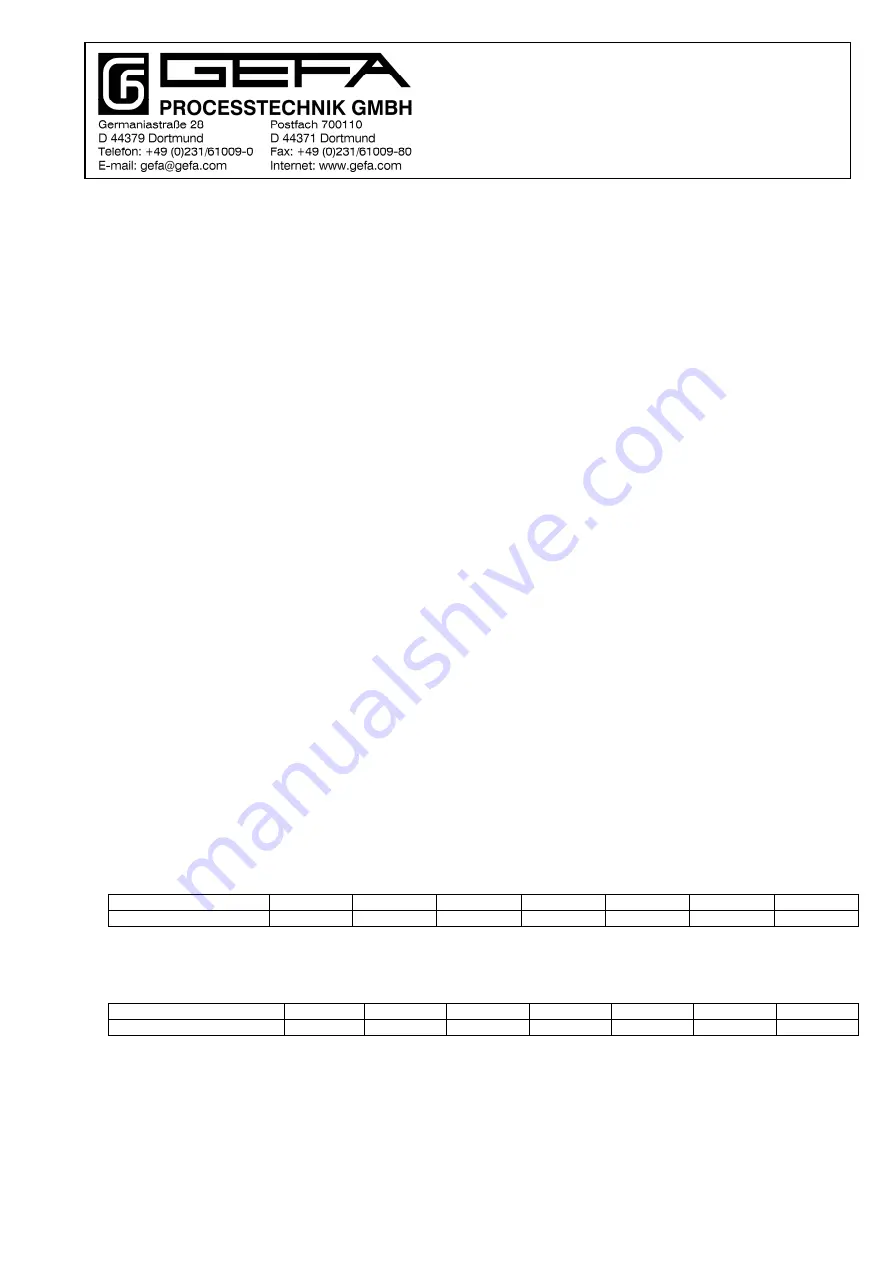
\HGT-Wartungsanleitung (GB) (GR) 05.11.2014
Page
1 of 2
Operating instructions
Maintenance / Mounting
triple offset
butterfly valve series HGT
General information
A routine maintenance or lubrication of the triple offset butterfly valve HGT is not necessary.
Should a leakage occur at the gland packing, retighten the gland nut (21). Take care that the gland nut is not tightened too
much. Normally the leakage can be stopped by simply turning the nut by a quarter.
Replacing the Gland Packing
If the leakage cannot be stopped using the above method, the gland packing must be replaced.
For replacing the gland packing it is not necessary to remove the valve from the pipeline.
Check whether the pipeline has been rendered depressurized and is empty.
Remove the operating element.
Loosen the fixing devices (19, 21) of the gland flange and lift off the gland flange (9).
Remove the gland (8). A groove in the upper part of the gland makes the removal easier.
Remove the packing rings (6) and thoroughly clean the area of the gland packing.
Insert a new packing set, whereby it is to be ensured that the correct packing material is used.
Insert the gland, place the gland flange on top and fix it using the screws and nuts. Tighten the nuts
alternately so that the gland flange is not tilted. Only slightly tighten the nuts until the leakage is stopped.
Replacing the Seat
In order to ensure that the valve works safely, we highly recommend to order the replacing of the seat at the
factory of GEFA Processtechnik GmbH. If the changing of the seat is not carried out by our staff, we will not assume
any liability for the correct working of the valve.
The valve must be taken out of the pipeline for replacing the seat.
Ensure that the pipeline is rendered depressurized and is empty.
Completely close the valve, loosen the flange screws and remove them so far that the valve can be taken out.
Lay the valve down with the insert ring (7) facing upwards so that the valve’s actuator connection is in a 12 o’ clock position.
The flat sealing surface of the disc is now on the left-hand side.
Unscrew the cylinder screws (16) and lift the insert ring out of the body.
Remove the old seat (4). Clean the body, insert ring and disc in the area of the seat-engaging surface.
Bring the disc exactly into ‘CLOSED’ position. For this, the front side of the disc must be parallel to the seat contact
surface.
In the area of the seat contact surface the body (1) has 3 center holes (ø2 mm). The holes are arranged on top (12 o’ clock),
at the bottom (6 o’ clock) and on the left-hand side (9 o’ clock). Insert the new seat (4) in such a way that the holes in the
seat are congruent with the center holes in the body. Now the sealing surface of the seat must fully lie against the disc.
The insert ring is equipped with 2 opposing threaded holes. Another threaded respectively center hole is displaced at 90° to
these threaded holes. The insert ring is to be placed into the body in such a way that the opposing threaded holes are in the
12 o’ clock and 6 o’ clock positions and the third hole is in the 9 o’ clock position (left-hand side).
Insert the cylinder screws (16) and slightly tighten them alternately.
Carefully open and close the valve 5 times to allow the seat to centre itself. Whilst actuating the valve, it may be necessary
to increase the force with each closing operation in order to ensure the exact position of the seat.
Tighten the screws of the insert ring alternately, using following torque:
M5 = 6 Nm
M6 = 10 Nm
In order to achieve an optimum seat tightness, the seat has to be forced once. For this purpose, the insert ring has to be
pushed against the body, using the following force:
If no corresponding compactor is available, the seat can also be forced by installing it between 2 flanges. Using
this method care should be taken that a ring (or a disc) has to be laid on the insert ring, that has a slightly smaller
outside diameter than the outside diameter of the insert ring is. Tighten the flange screws alternately with the following
torque (that apply to DIN PN 10 flanges):
Ensure that the pressure is evenly applied to the insert ring.
After having forced the seat, alternately retighten the screws of the insert ring with the following torque:
M5 = 6 Nm
M6 = 10 Nm
Pressure-test the valve.
DN
80 100 125 150 200 250 300
Force
[kN]
60 70 90 100 150 200 240
DN
80 100 125 150 200 250 300
Tightening
torque
[Nm]
22 25 35 45 65 65 75