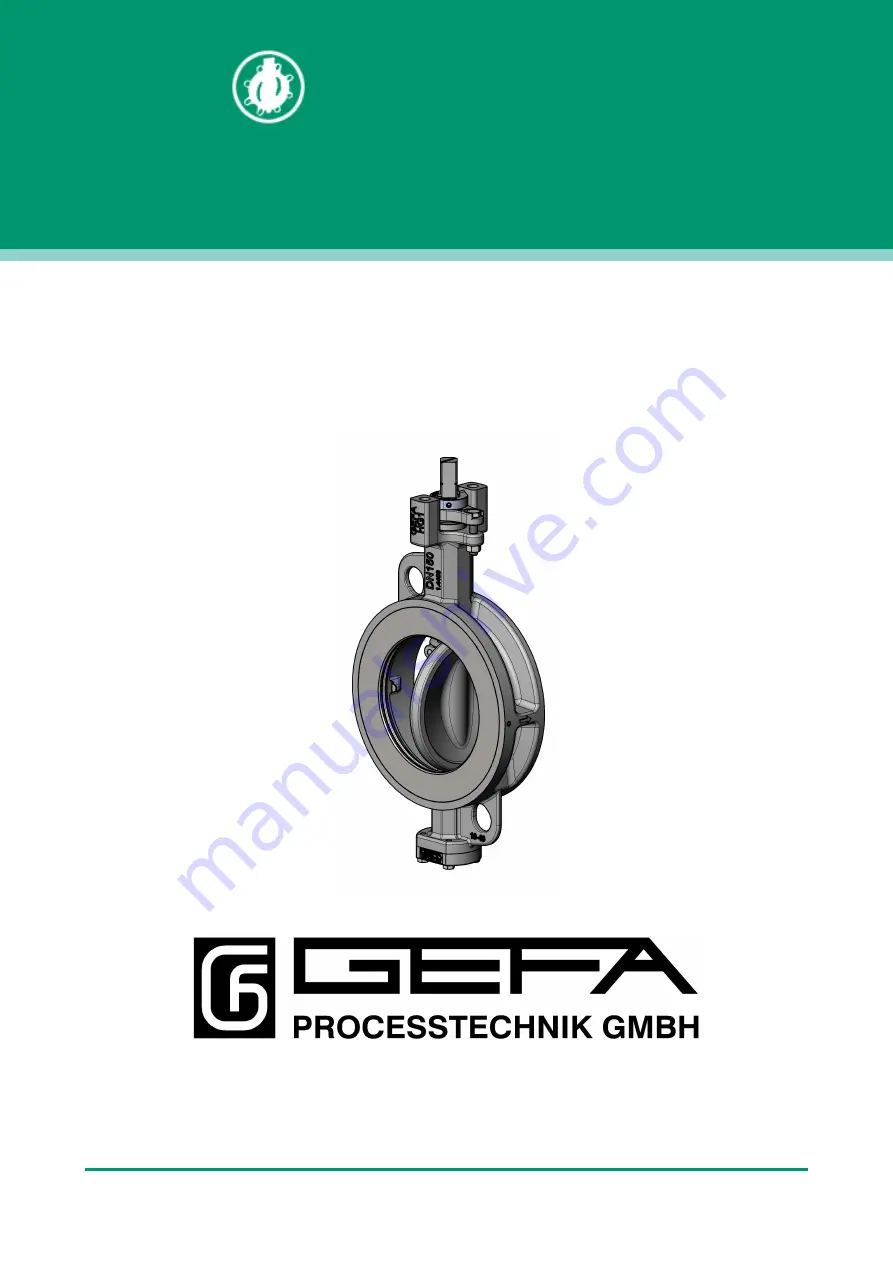
HG1
ARMATURENTECHNIK
Original instructions
Germaniastraße 28 • D-44379 Dortmund
Tel.: +49 (0)231 / 61 00 9-0 • Fax: +49 (0)231 / 61 00 9-80
Internet: www.gefa.com • E-Mail: [email protected]
Version 0 • Dokument-Nr. 74572811
HG1
ARMATURENTECHNIK
Original instructions
Germaniastraße 28 • D-44379 Dortmund
Tel.: +49 (0)231 / 61 00 9-0 • Fax: +49 (0)231 / 61 00 9-80
Internet: www.gefa.com • E-Mail: [email protected]
Version 0 • Dokument-Nr. 74572811