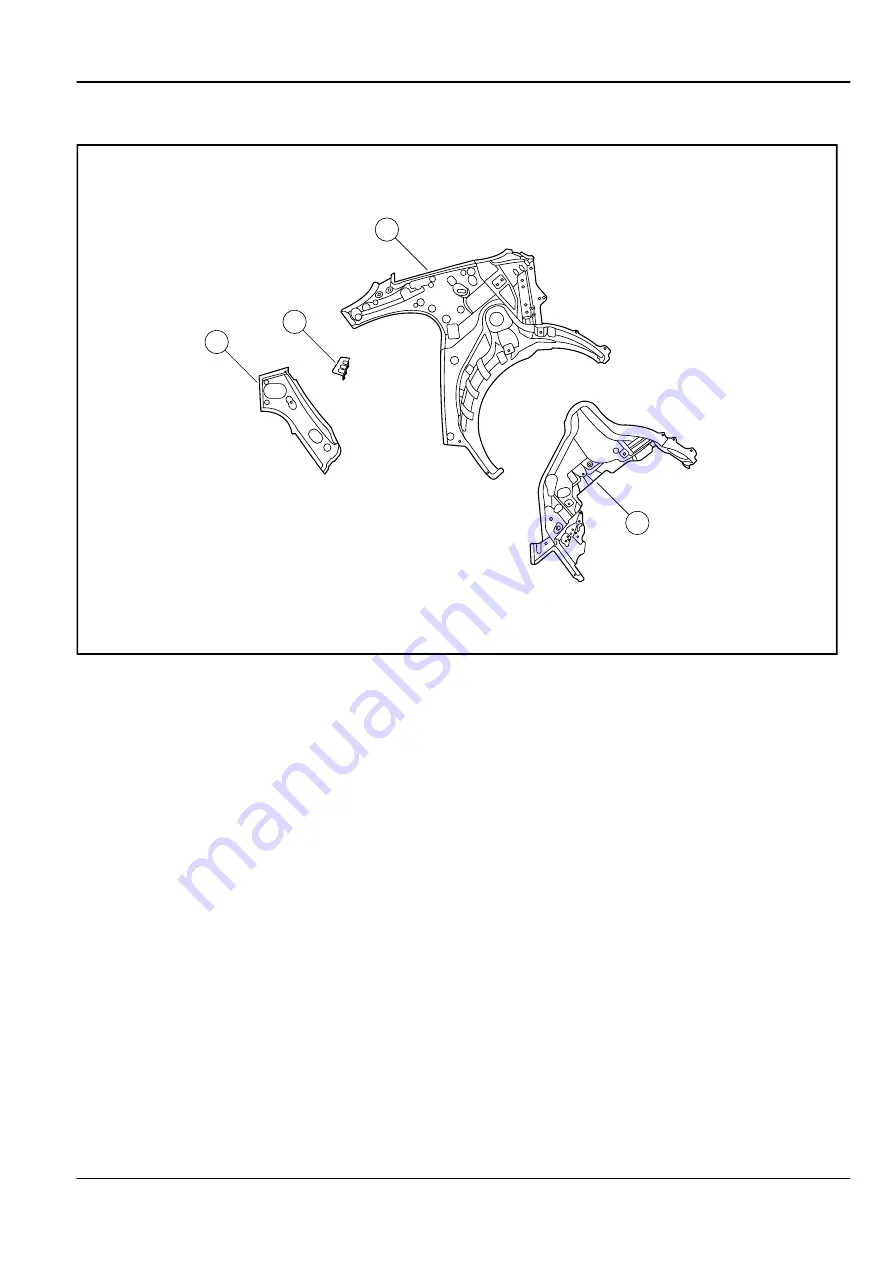
12.12.3.12 Body Rear Pillars (Sedan)
2
4
1
3
FE12-1040b
Legend
1. Left Rear Pillar Inner Panel Assembly
2. Left Rear Pillar Reinforcement Panel
3. Left Rear Wheelhouse Panel
4. Left Rear Door Lock Mounting Panel
Body, Sheet Metal and Painting
Collision Repair
12-149
EC718/EC718RV EC715/EC715RV 10/2009
Summary of Contents for EC715 2009
Page 4: ......
Page 330: ...Next Step 10 End 2 248 Fuel System JL4G18 D Engine EC718 EC718RV EC715 EC715RV 10 2009 ...
Page 1164: ......
Page 2008: ......