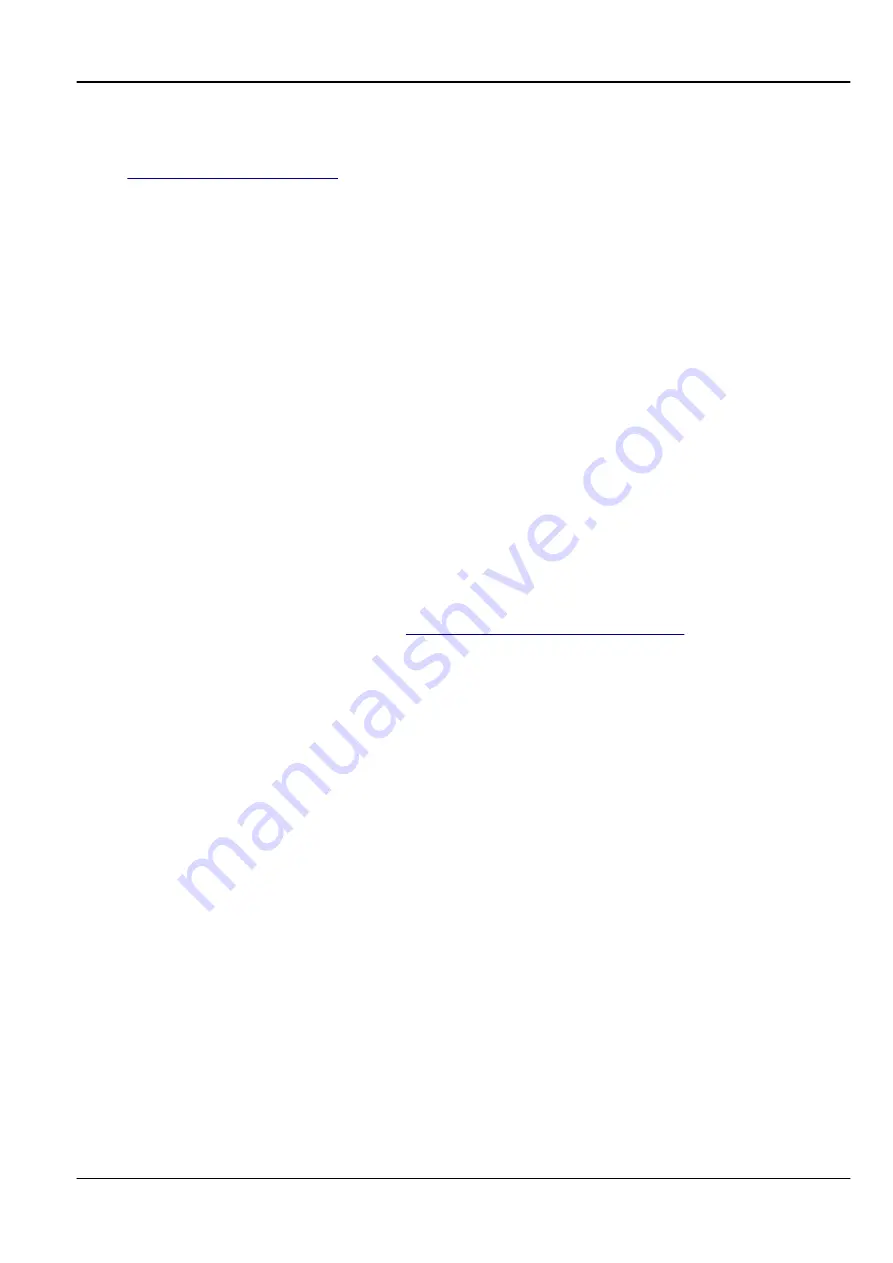
11.17.7 Diagnostic Information and Procedures
11.17.7.1 Diagnosis Description
Refer to
get familiar with the system functions and operation before start system diagnostics, so
that in the event of failure it will help to determine the correct diagnostic steps, more importantly, it will also help to determine whether
the customer described situation is normal.
11.17.7.2 Visual Inspection
–
Check the installed after market equipment that may affect data communication system.
–
Check the easy to access system components to identify whether there is a significant damage or a potential malfunction.
–
If the data communication system has a fault, before repair check whether all data communication system control module harness
connectors have been correctly connected.
11.17.7.3 CAN Bus Fault Prevention
–
Do not stretch CAN bus wiring harness.
–
Do not open the CAN bus wiring harness more than 4 cm (1.6 in).
–
Do not connect CAN bus wiring harness with other wiring harness.
–
Use manufacturers recommended scan tool.
11.17.7.4 CAN Bus Integrity Diagnosis
To check whether CAN bus is normal, perform the CAN bus integrity diagnosis to confirm whether the fault is due to the physical
CAN bus circuit open. For specific operations. Refer to
CAN Bus Network Integrity Checking
.
11.17.7.5 CAN Bus Wiring Harness Repair Specification
–
CAN_H and CAN_L two lines must be articulated way.
–
When CAN bus circuit fault occurs, the length of wire joints should not exceed L1: 50 mm (1.97 in).
–
If the circuit is open at two or more places. The distance between the two places must be more than L2: 100 mm (3.94 in), then
it is allowed to repair. Otherwise replace the CAN bus wiring harness.
Body Electric
Data Communication System
11-521
EC718/EC718RV EC715/EC715RV 10/2009
Summary of Contents for EC715 2009
Page 4: ......
Page 330: ...Next Step 10 End 2 248 Fuel System JL4G18 D Engine EC718 EC718RV EC715 EC715RV 10 2009 ...
Page 1164: ......
Page 2008: ......