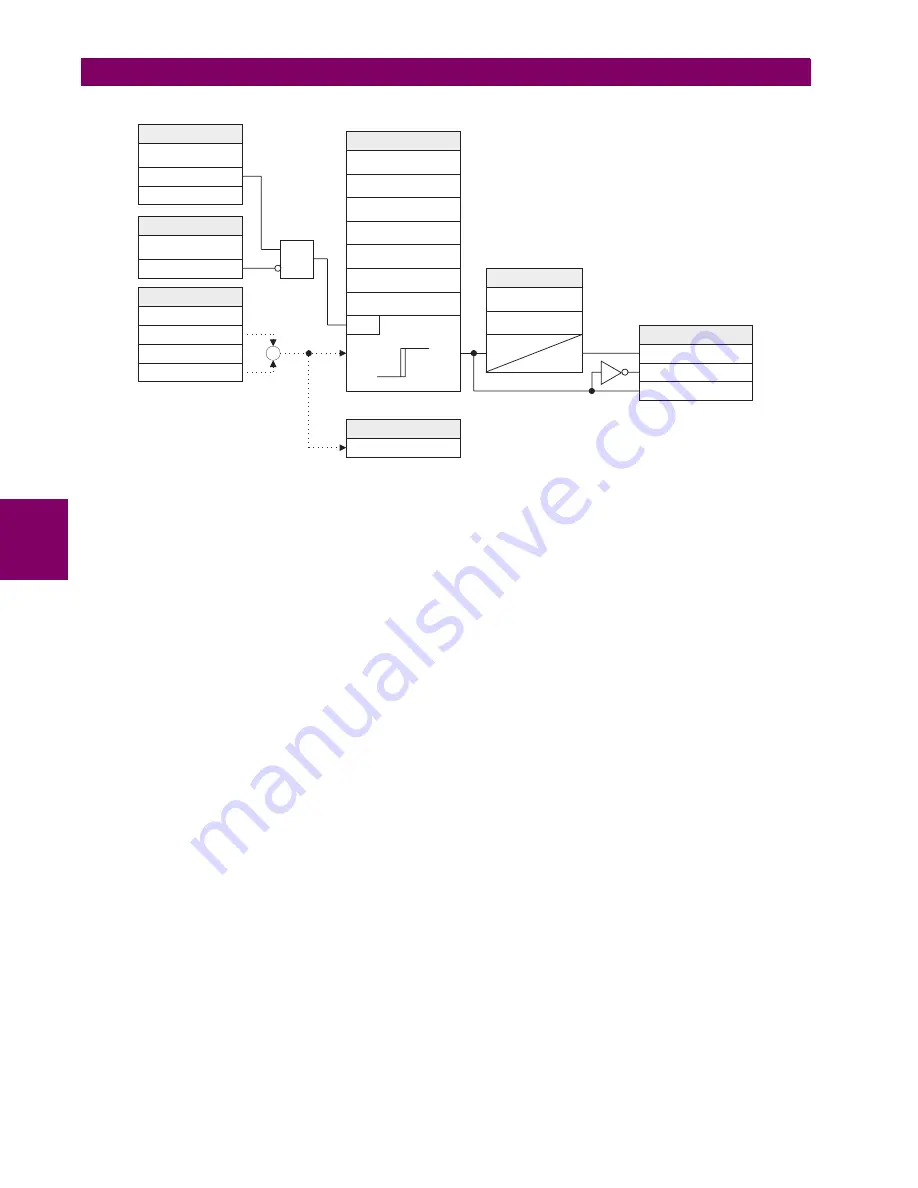
5-102
F60 Feeder Protection System
GE Multilin
5.4 FLEXLOGIC™
5 SETTINGS
5
Figure 5–42: FLEXELEMENT™ SCHEME LOGIC
The
FLEXELEMENT 1 +IN
setting specifies the first (non-inverted) input to the FlexElement™. Zero is assumed as the input if
this setting is set to “Off”. For proper operation of the element at least one input must be selected. Otherwise, the element
will not assert its output operands.
This
FLEXELEMENT 1 –IN
setting specifies the second (inverted) input to the FlexElement™. Zero is assumed as the input if
this setting is set to “Off”. For proper operation of the element at least one input must be selected. Otherwise, the element
will not assert its output operands. This input should be used to invert the signal if needed for convenience, or to make the
element respond to a differential signal such as for a top-bottom oil temperature differential alarm. The element will not
operate if the two input signals are of different types, for example if one tries to use active power and phase angle to build
the effective operating signal.
The element responds directly to the differential signal if the
FLEXELEMENT 1 INPUT MODE
setting is set to “Signed”. The ele-
ment responds to the absolute value of the differential signal if this setting is set to “Absolute”. Sample applications for the
“Absolute” setting include monitoring the angular difference between two phasors with a symmetrical limit angle in both
directions; monitoring power regardless of its direction, or monitoring a trend regardless of whether the signal increases of
decreases.
The element responds directly to its operating signal – as defined by the
FLEXELEMENT 1 +IN
,
FLEXELEMENT 1 –IN
and
FLEX-
ELEMENT 1 INPUT MODE
settings – if the
FLEXELEMENT 1 COMP MODE
setting is set to “Level”. The element responds to the
rate of change of its operating signal if the
FLEXELEMENT 1 COMP MODE
setting is set to “Delta”. In this case the
FLEXELE-
MENT 1 dt UNIT
and
FLEXELEMENT 1 dt
settings specify how the rate of change is derived.
The
FLEXELEMENT 1 DIRECTION
setting enables the relay to respond to either high or low values of the operating signal. The
following figure explains the application of the
FLEXELEMENT 1 DIRECTION
,
FLEXELEMENT 1 PICKUP
and
FLEXELEMENT 1 HYS-
TERESIS
settings.
842004A3.CDR
FLEXELEMENT 1
FUNCTION:
S
ETT
I
NG
Enabled = 1
S
ETT
I
NG
S
FLEXELEMENT 1 INPUT
MODE:
FLEXELEMENT 1 COMP
MODE:
FLEXELEMENT 1
DIRECTION:
FLEXELEMENT 1 PICKUP:
FLEXELEMENT 1 dt UNIT:
FLEXELEMENT 1 dt:
RUN
FLEXELEMENT 1 +IN:
S
ETT
I
NG
S
Actual Value
FLEXLOG
I
C OPE
R
AND
S
FxE 1 DPO
FxE 1 OP
FxE 1 PKP
FLEXELEMENT 1 -IN:
Actual Value
+
-
FlexElement 1 OpSig
ACT
U
AL VAL
U
E
Disabled = 0
FLEXELEMENT 1 BLK:
S
ETT
I
NG
Off = 0
AND
t
PKP
t
RST
S
ETT
I
NG
S
FLEXELEMENT 1 RST
DELAY:
FLEXELEMENT 1 PKP
DELAY:
FLEXELEMENT 1 INPUT
HYSTERESIS:
Summary of Contents for F60 UR Series
Page 2: ......
Page 4: ......
Page 30: ...1 20 F60 Feeder Protection System GE Multilin 1 5 USING THE RELAY 1 GETTING STARTED 1 ...
Page 48: ...2 18 F60 Feeder Protection System GE Multilin 2 2 SPECIFICATIONS 2 PRODUCT DESCRIPTION 2 ...
Page 126: ...4 30 F60 Feeder Protection System GE Multilin 4 2 FACEPLATE INTERFACE 4 HUMAN INTERFACES 4 ...
Page 354: ...5 228 F60 Feeder Protection System GE Multilin 5 9 TESTING 5 SETTINGS 5 ...
Page 382: ...6 28 F60 Feeder Protection System GE Multilin 6 5 PRODUCT INFORMATION 6 ACTUAL VALUES 6 ...
Page 398: ...8 8 F60 Feeder Protection System GE Multilin 8 2 FAULT LOCATOR 8 THEORY OF OPERATION 8 ...
Page 414: ...A 14 F60 Feeder Protection System GE Multilin A 1 PARAMETER LIST APPENDIXA A ...
Page 492: ...B 78 F60 Feeder Protection System GE Multilin B 4 MEMORY MAPPING APPENDIXB B ...
Page 530: ...D 10 F60 Feeder Protection System GE Multilin D 1 IEC 60870 5 104 APPENDIXD D ...
Page 542: ...E 12 F60 Feeder Protection System GE Multilin E 2 DNP POINT LISTS APPENDIXE E ...
Page 558: ...x F60 Feeder Protection System GE Multilin INDEX ...