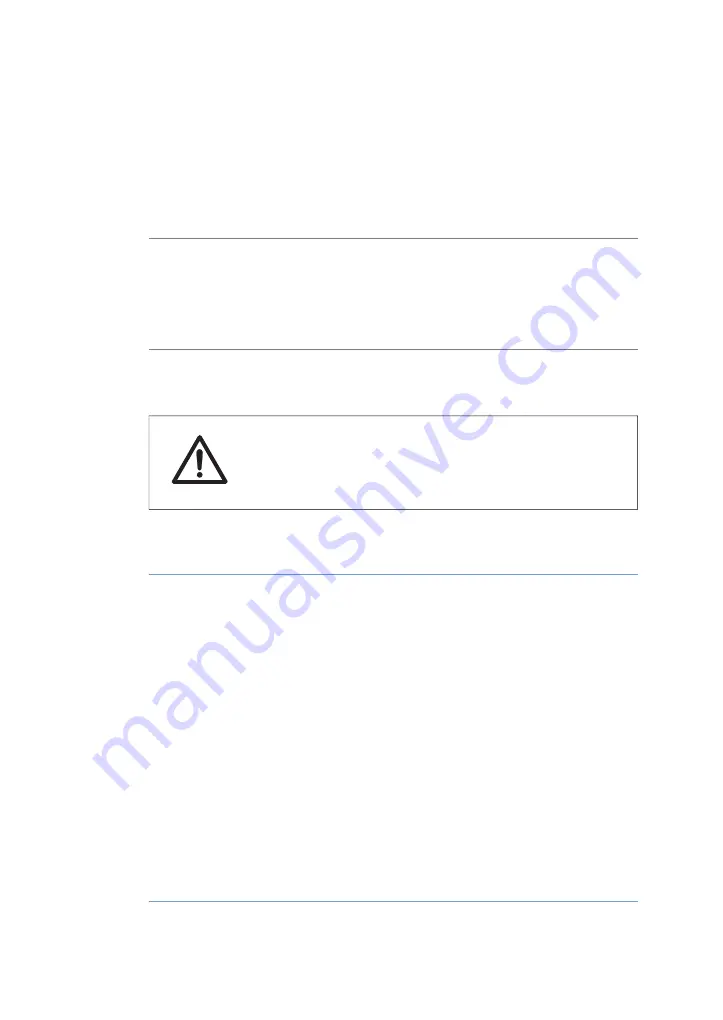
7.5.2
Replace the pH electrode
Maintenance interval
Replace the pH electrode every six months, or when required.
Required material
The following materials are required: pH electrode, deionized water and standard buffer
pH 4.
Instruction
CAUTION
pH-electrode. Handle the pH-electrode with care. The glass tip
may break and cause injury.
Follow the instructions below to replace the pH electrode.
Action
Step
Disconnect the pH electrode cable of the used pH electrode from the con-
nection on the front of the pH valve.
1
Unscrew the nut of the pH electrode by hand, and pull the used electrode
away.
2
Unpack the new pH electrode. Remove the cover from the tip of the new pH
electrode. Make sure that the electrode is not broken or dry.
3
Prior to first use of the electrode, immerse the glass bulb in deionized water
for 30 minutes and then in a standard buffer, pH 4, for 30 minutes.
4
Carefully insert the new pH electrode into the pH flow cell. Tighten the nut
by hand to secure the electrode.
5
Connect the pH electrode cable of the new electrode to the connection on
the front of the pH valve.
6
Calibrate the new pH electrode, see Section 7.7.1 Calibrate the pH monitor,
on page 321.
7
286
ÄKTA avant User Manual 29035184 AE
7 Maintenance
7.5 Semiannual maintenance
7.5.2 Replace the pH electrode
Summary of Contents for AKTA avant
Page 1: ...ÄKTA avant User Manual ...
Page 2: ...Page intentionally left blank ...
Page 536: ...Page intentionally left blank ...
Page 537: ...Page intentionally left blank ...