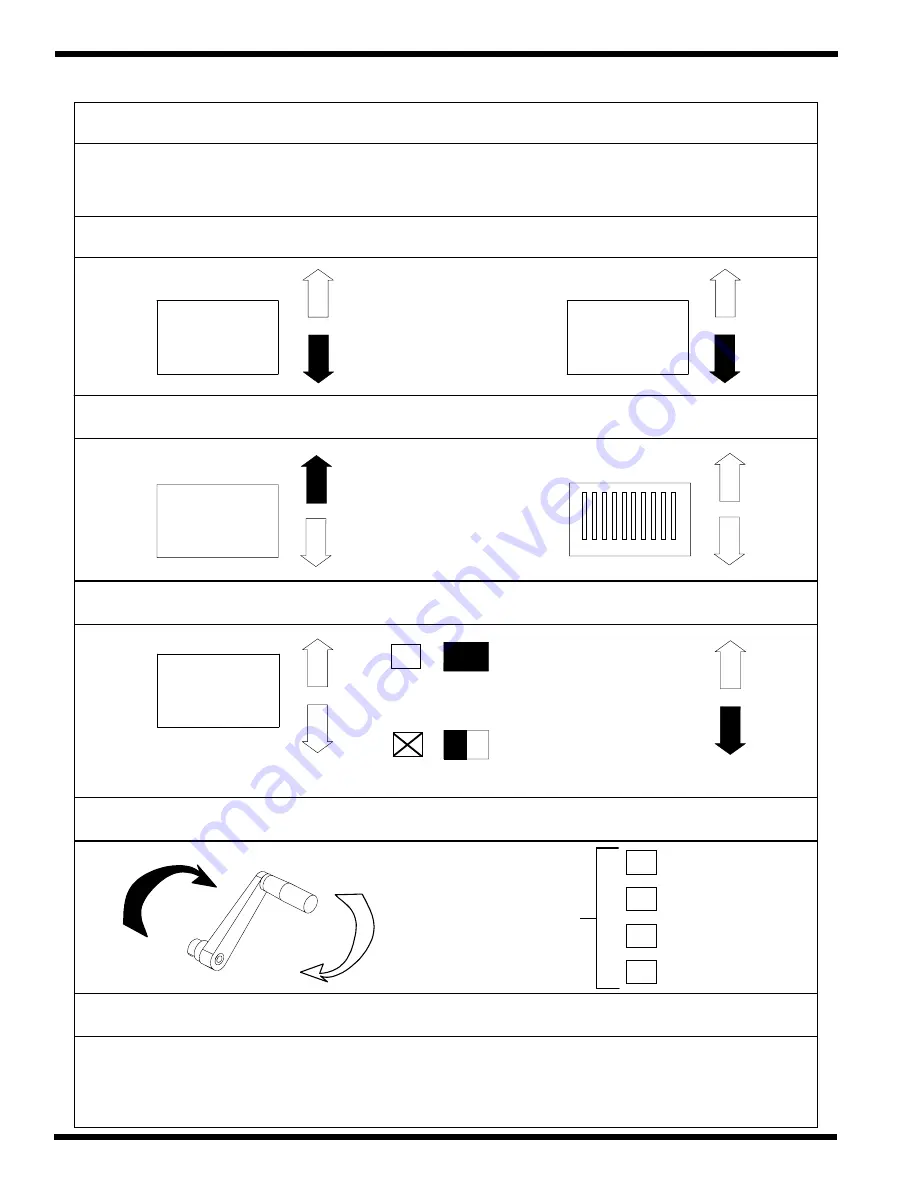
© GBC Pro - Tech August 1999
Page 6 - 116
F - 160 Operation and Maintenance Manual
Applications
Parameter Chart 10 - Thermal decal and Mount ( Mount )
T E M P E R A T U R E
GAP & PRESSURE
MOTOR DIRECTION & SPEED
T O P T E M P .
B O T . T E M P .
P R E S S U R E
G A P
S P E E D
F W D
R E V .
G O
G O
= Panel
SOLID
F L A S
H I N G
= Footswitch
PULL ROLL SETTINGS
N O T E S
N / A
1/4 Turn
1/2 Turn
3/4 Turn
P R E S S U R E
MATERIALS
U P P E R U N W I N D :
L O W E R U N W I N D :
S U B S T R A T E :
P R I N T S :
N / A
N / A
Decals
6 8
6 8
1
0.00
The mounting process is done from the rear position of the laminator to avoid the waiting period involved with
cooling down the main rollers. The rollers may be left heated or turn them down 68
o
F. Pull roller pressure
with be dependent of the substrate. Apply the necessary pressure without crushing the board.
D O W N
U P
N / A