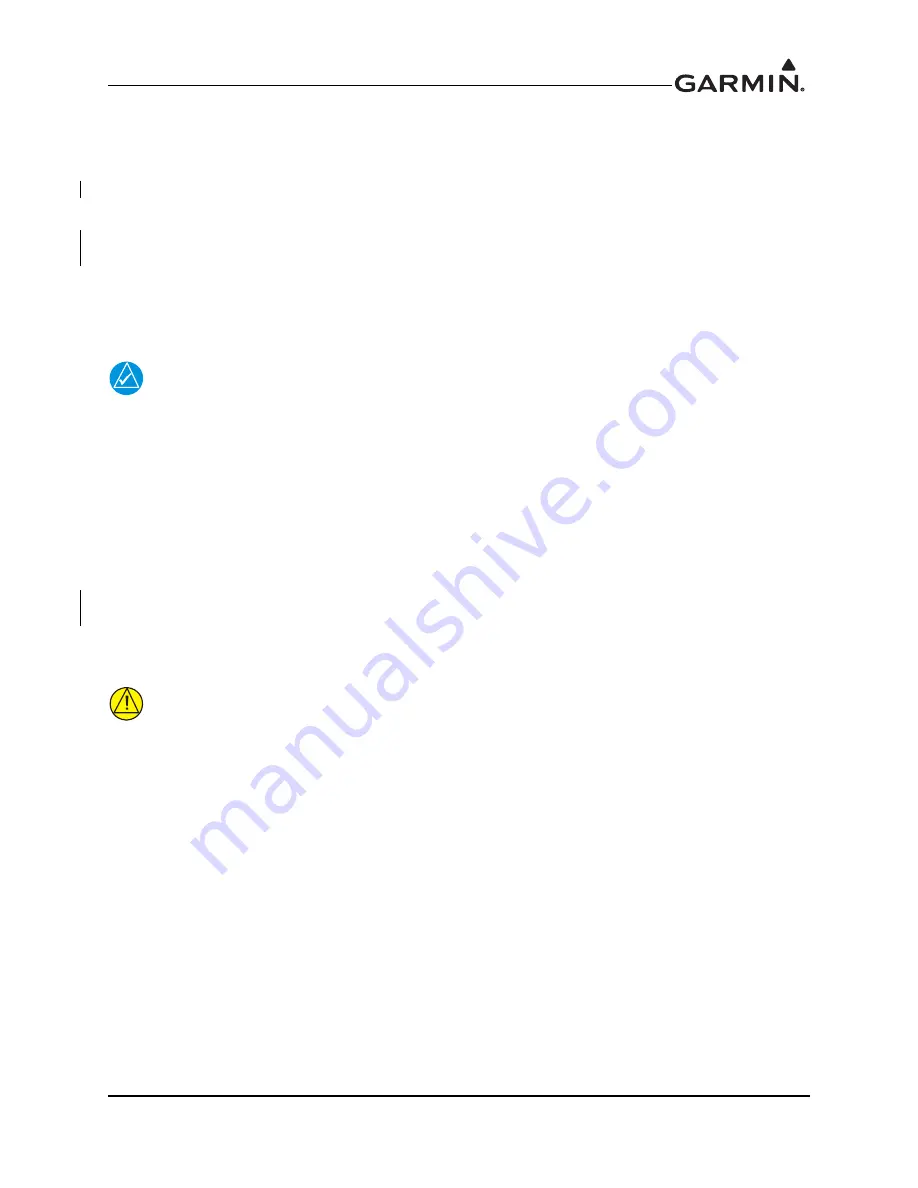
190-01279-01
GTS 8XX Part 23 AML STC Maintenance Manual
Rev. 2
Page 6-7
6.7 Omni-directional (Monopole) Antenna
Removal
1. Ensure there is no power supplied to the GTS 8XX.
2. Remove sealant from the antenna’s fasteners.
3. Remove the fasteners attaching the antenna to the fuselage.
4. Remove environmental seal between the antenna and fuselage skin and pull the antenna away from
the fuselage.
5. Disconnect the antenna coaxial cable from the antenna connector.
6. Remove the antenna from the aircraft. Retain the antenna backing plate (if used) and O-ring.
Re-installation
NOTE
Ensure the electrical bond meets requirements in Table 2-2.
1. Ensure there is no power supplied to the GTS 8XX.
2. Inspect the antenna O-ring for damage. If necessary, replace the O-ring with a new O-ring.
Otherwise, re-install the O-ring in the groove on the antenna baseplate.
3. Position the antenna backing plate (if used) on the aircraft structure.
4. Reconnect the coaxial cable to the antenna connector.
5. Position the antenna on the fuselage and re-install antenna fasteners. Torque the 8-32 fasteners
12-15 in-lbf.
6. Seal the antenna base to fuselage skin by applying MIL-S-8802 sealant around entire perimeter of
antenna base in a uniform fillet.
7. Ensure that the antenna connector is not contaminated with sealant.
8. Seal the mounting screws with sealant.
CAUTION
Do not use construction grade RTV sealant or sealants containing acetic acid. These
sealants may damage the electrical connections to the antenna. Use of these sealant types
may void the antenna warranty.
9. Complete the appropriate return to service procedures in Section 7.