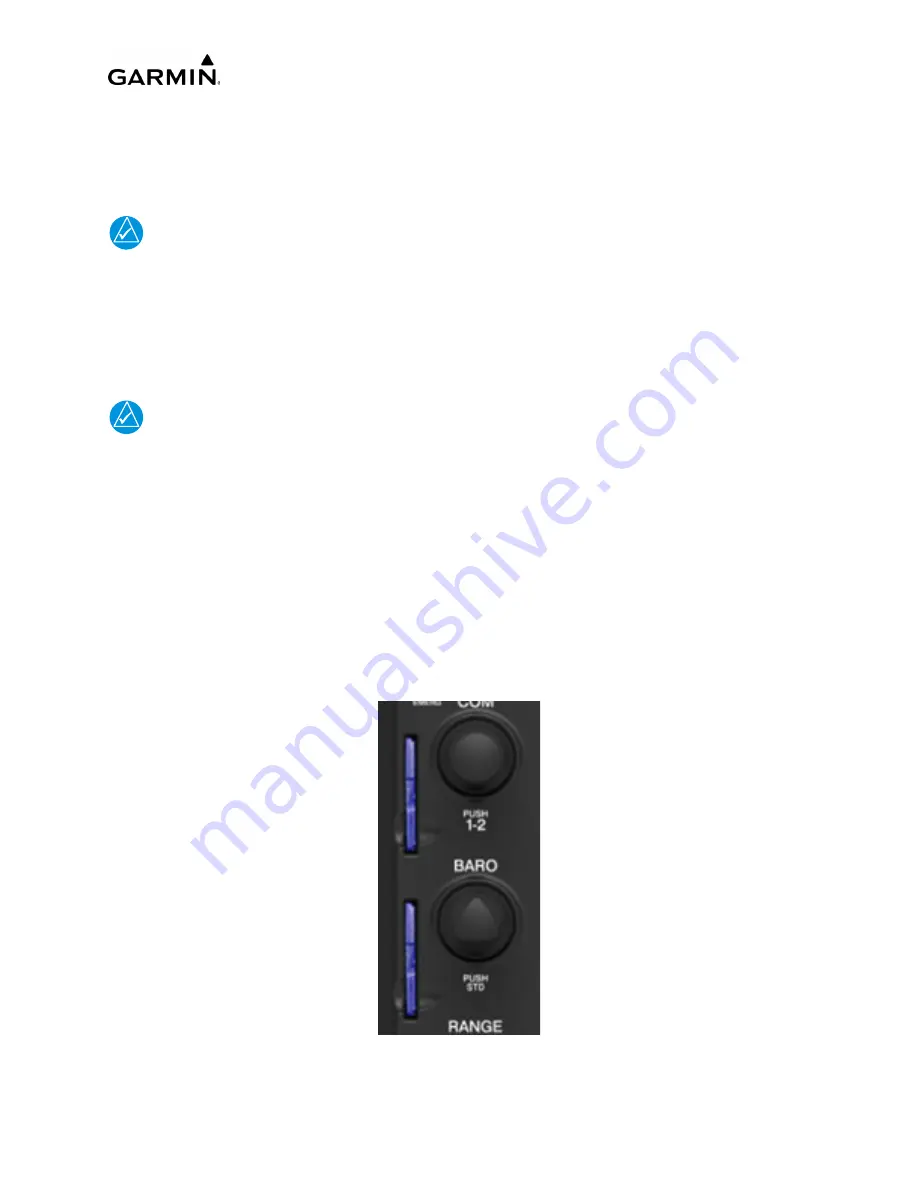
______________________________________________________________________________
____________________________________________________________________________
LMM for the Kodiak 100
Page 3-1
190-02102-00 Rev.4
3 LOADING SYSTEM SOFTWARE AND CONFIGURATION
The G1000 NXi system does not contain the correct software or configuration settings for
the Kodiak 100 when it is shipped from the factory. Those must be loaded when the
system is initially installed.
NOTE
There might be a situation in which the only solution to a problem is to
reload system software and configuration according to the procedures in
this section. Perform the troubleshooting steps in
shooting does not resolve the issue; before reloading, contact Garmin Avi-
ation Support to find another solution to the fault if one exists.
3.1 Loader Cards
NOTE
The system requires the use of SanDisk SD™ cards for loading software
and configuration.
A Secure Digital (SD) Card is used for loading software and configuration. It is very
important to use the correct loader card part number. Each loader card part number
defines all files found on the card for a specific installation. Approved loader card part
numbers can be found in the Kodiak 100 Aircraft Maintenance Manual (AMM).
The GDU data card slots are located in the upper right portion of the display bezels (see
). Each display bezel is equipped with two card slots. SD cards are used for
aviation databases, system software, recording flight data, and storing electronic
documents.
Figure 3-1. GDU SD Card Slots
Uncontrolled if Printed
Summary of Contents for Cessna Caravan G1000
Page 2: ...BLANK PAGE Uncontrolled if Printed...
Page 288: ...Uncontrolled if Printed...