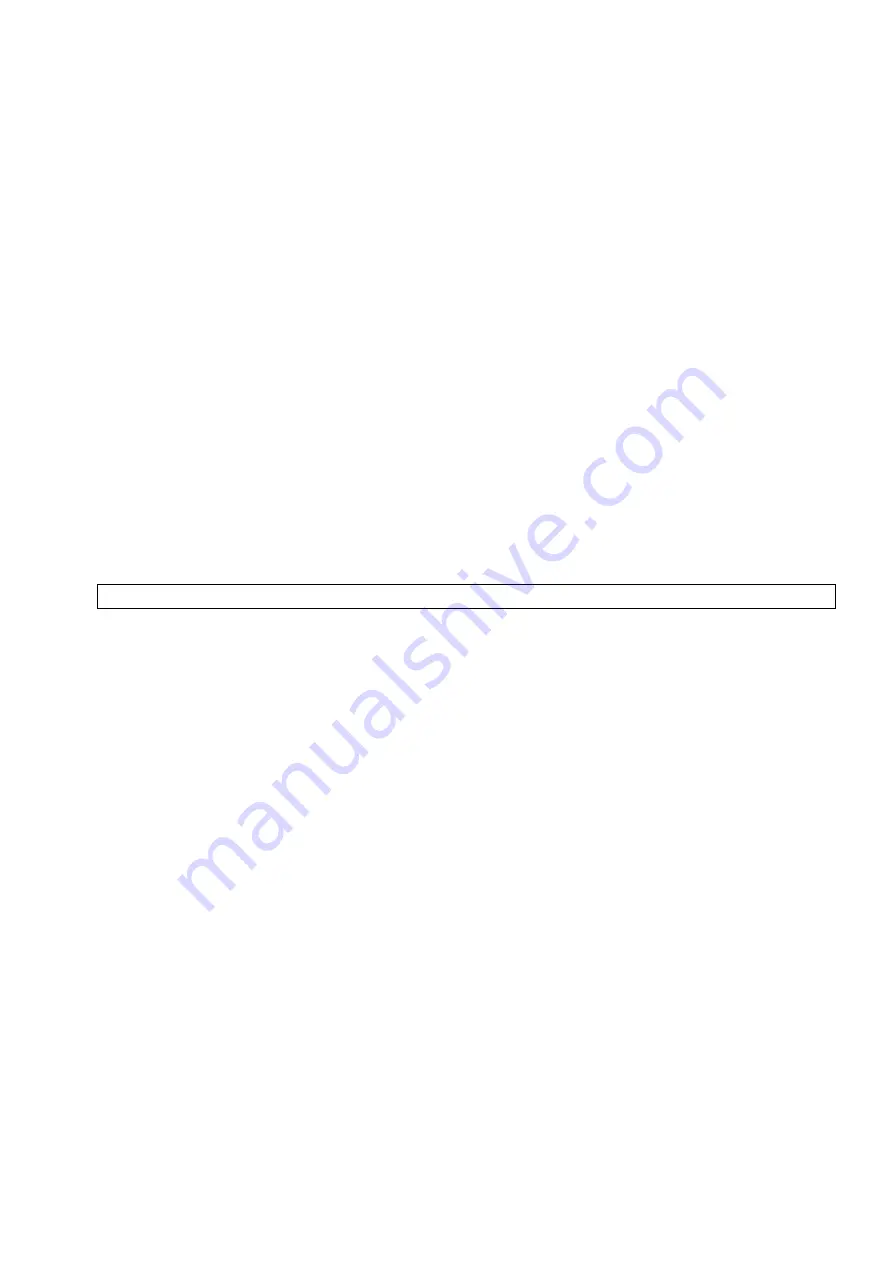
SAFETY
PAGE 13
The installation should have purging valves fitted to the inlet and outlet lines of the compressor,
permitting the inert gas used for purging to be admitted and discharged before and after the equipment
being purged.
Once this has been acheived the valves should be locked and /or plugged to avoid them being left
open whilst running on gas.
Operators should also be aware that the compressor is not guaranteed leak tight whether in normal
operation or under fault conditions and It is assumed that the compressor is situated in a well
ventilated area with suitable gas leakage detection equipment to minimise possible risks.
Due to the unknown nature of the plant processes involved, Reavell cannot be held responsible
for any heath risk arising from leakage of gas into the atmosphere.
The following comments may help to achieve successful purging of the compressor:-
The use of an
Oxygen
meter is recommended when purging prior to running on flammable gases.
Feeding the purge gas at pressure (maximum 0.5 bar g) will speed up procedure.
The crankcase will be purged more quickly if the oil filler cap is removed and the rod inside is
depressed to allow the air to escape.
The pipes from the separators to the unloader valves and from the first stage to unloaders (and water
valve if fitted) can be purged by disconnecting them at their far end, allowing the purge gas to pass
through and remove the air,
before reconnecting them.
After any maintenance or repairs have been carried out which involves dismantling and opening up gas
containing parts, the system must always be re-purged.
1.9 HAZARDOUS AREA OPERATION
1.9.1
ELECTRICAL CONNECTIONS
There are varying regulations covering electrical equipment specifications for use with flammable
gases. It is the responsibility of the user to meet all regulations for electrical equipment and its
connections whether or not supplied by Reavell.
1.9.2
DEFINITIONS
When flammable materials are mixed with air in appropriate proportions, a potentially explosive mixture
is produced. There is therefore a danger of explosion existing whenever flammable gases are being
handled.
To protect personnel and plant, special precautions must be taken to prevent ignition. Conditions likely
to ignite a potential explosive mixture include, but are not limited to the following:-
Electrical sparks produced when a circuit is opened or closed (e.g. cut-out switches)
Conductors heated by the passage of the current or by faulty equipment.
Sparks produced by a moving object hitting a stationary one.
Sparks produced by the periodic discharge of static electricity.
Summary of Contents for Reavell H5000 Series
Page 2: ......
Page 18: ...SAFETY PAGE 16...
Page 20: ...AMENDMENTS PAGE 18...
Page 22: ...COMPRESSOR LOG SHEET PAGE 20 REMARKS DATE REMARKS DATE...
Page 24: ...GENERAL DESCRIPTION AND OPERATION PAGE 22 4 6 LUBRICATION SCHEMATIC FLOW DIAGRAM...
Page 26: ...GENERAL DESCRIPTION AND OPERATION PAGE 24...
Page 36: ...OPERATION AND ROUTINE MAINTENANCE PAGE 34...
Page 44: ...DISMANTLING AND REASSEMBLY OF VALVES PAGE 42...
Page 50: ...FAULT GUIDE PAGE 48...
Page 72: ...PARTS LIST PAGE 70 93 95 1ST STAGE CONCENTRIC VALVE 9 8 6 5 4 2 1 3...
Page 74: ...PARTS LIST PAGE 72 96 97 2ND STAGE CONCENTRIC VALVE 2 1 3 4 5 6 5...
Page 80: ...PARTS LIST PAGE 78...
Page 92: ...ANCILLARY PARTS PAGE 90...
Page 94: ...STANDARD WIRING TERMINAL NUMBERS PAGE 92...
Page 95: ......