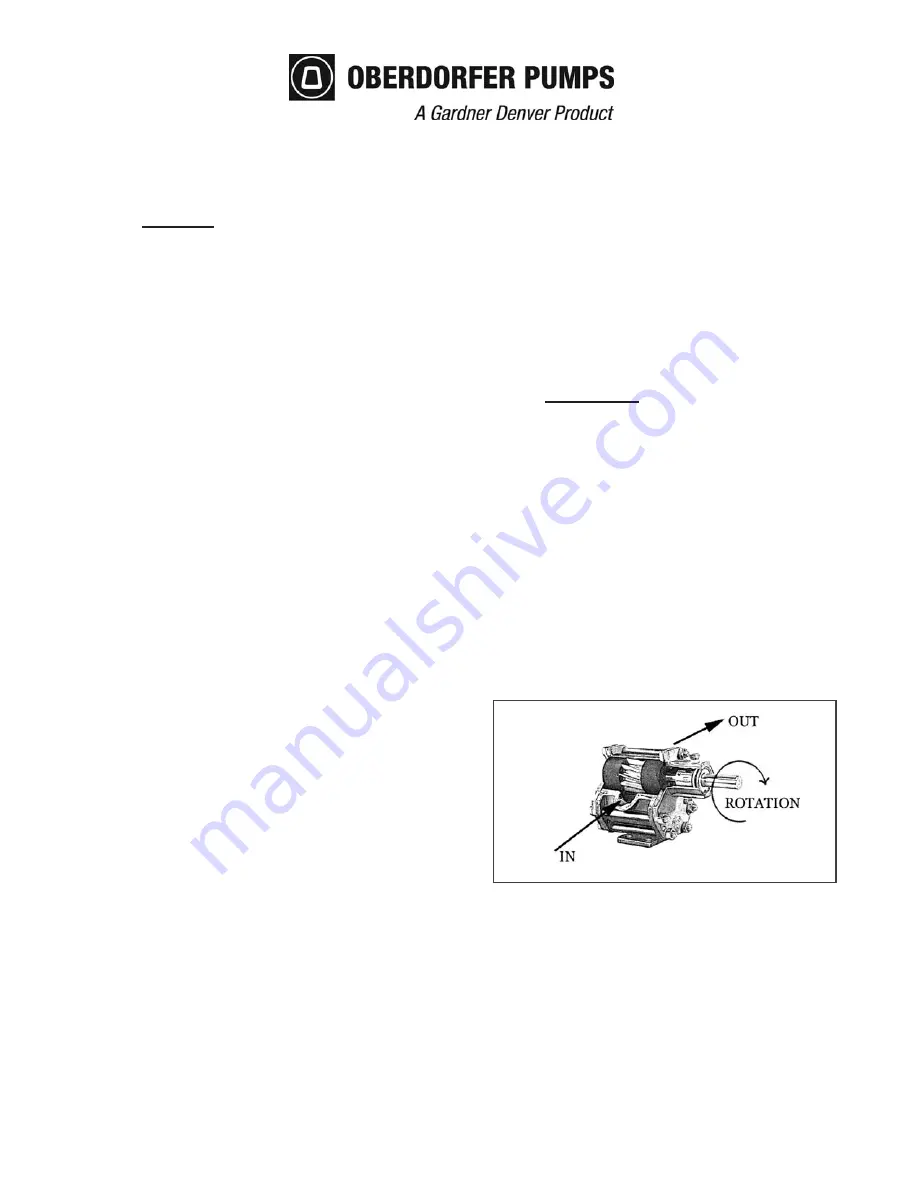
Chemsteel® Sealed Rotary Gear Pumps
Installation, Operation and Maintenance Instructions
Introduction
Congratulations for choosing an Oberdorfer Chemsteel
®
pump,
the Industry Standard for quality since 1890.
Construction
Chemsteel® metal pump housings are made of top quality invest-
ment cast 316 Stainless Steel or Alloy C. Non-metallic pump
housings are constructed from injection molded Ryton® PPS or
PEEK®. Shafts are Stainless Steel, or Alloy B. Pumps are avail-
able with carbon-graphite bearings or with Teflon® bearings. No
bearing lubrication is required. Dynamic seal arrangements
include packing, lip, or mechanical seals for a variety of applica-
tion requirements. Static cover o-ring seals eliminate gasket prob-
lems.
Application Range
Chemsteel® Rotary Gear pumps are of the external gear positive
displacement type, displacing a finite volume of fluid with each
shaft revolution. As such, capacity varies in direct proportion to
pump speed. They are suited to handle clear lubricating and non-
lubricating fluids at temperatures to 450F. These pumps handle
viscous fluids to 100,000 cps (462,000 SSU) at reduced shaft
speeds, with flow rates to 60 GPM ( 227 LPM), differential pres-
sures to 150 psig (10.3 BAR), and suction lift capability to 20 feet
(6.1 meters) for new pumps.
Field Inspection
Chemsteel® Rotary Gear pumps may be readily inspected in the
field usually without removal from the drive or system plumbing.
Simply remove the cover nuts (or cap screws) to pull the rear
cover. Before attempting an inspection, follow safety precautions
and be sure to read and understand this manual.
New Pump Receipt Inspection
Upon receipt, check for obvious shipping damage and complete-
ness to purchase order requirements. Shortages or damage should
be reported immediately to the carrier and to your Oberdorfer dis-
tributor. Occasionally during shipment, possible misalignment or
other damage including cracked mechanical seal faces can occur.
As such, customers are advised to test the pump with water in a
convenient location prior to installing into the intended system.
Storage
If the pump is to be stored prior to installation, it is recommend-
ed that it be left in the original shipping carton with all shipping
plugs in place and stored in a dry environment avoiding tempera-
ture variations. Contact the motor manufacturer for specific motor
storage information.
Records
These instructions should be kept in a convenient location for
ready reference. The manual should be read carefully by persons
responsible for installation, operation, and maintenance of the
equipment. For ease of reference, a copy of the order should be
kept with the manual. Write down the pump model number as
shown on the pump nametag, and the date the unit was placed into
service.
Installation
Site Preparation
Choose a site that allows easy access to the pump for mainte-
nance. Consider protection from the elements. Guard against
drips and spray from nearby equipment. Choose a solid founda-
tion for mounting. If noise is a concern, consider a rubber pad
under the pump base to dampen.
Flow Direction
Chemsteel® pumps will perform equally well in either direction.
To change flow direction effectively reversing the suction and
discharge ports, simply switch driver rotation by following motor
wiring diagram instructions. Most pump motor units are factory
supplied with clockwise shaft rotation (when viewing the pump
from the shaft end).
Suction Plumbing
Suction side plumbing considerations are key to desirable pump
performance. Minimize head loss by assuring sufficient pipe size
(especially important for highly viscous services). Generally the
same size pipe as the pump ports is adequate. For long runs
(beyond 3 feet) or viscous fluids, use one or two pipe sizes larg-
er. Strive to keep the lines as short and straight as possible. If flex-
ible lines are used, they should be selected to prevent wall col-
lapse. To keep the pump from being starved or running dry, be
sure there is sufficient fluid supply. A flooded suction is general-
ly preferred. Suction lifts over 3 vertical feet and long horizontal
runs (beyond 3 lineal feet) require a foot or check valve below the
1