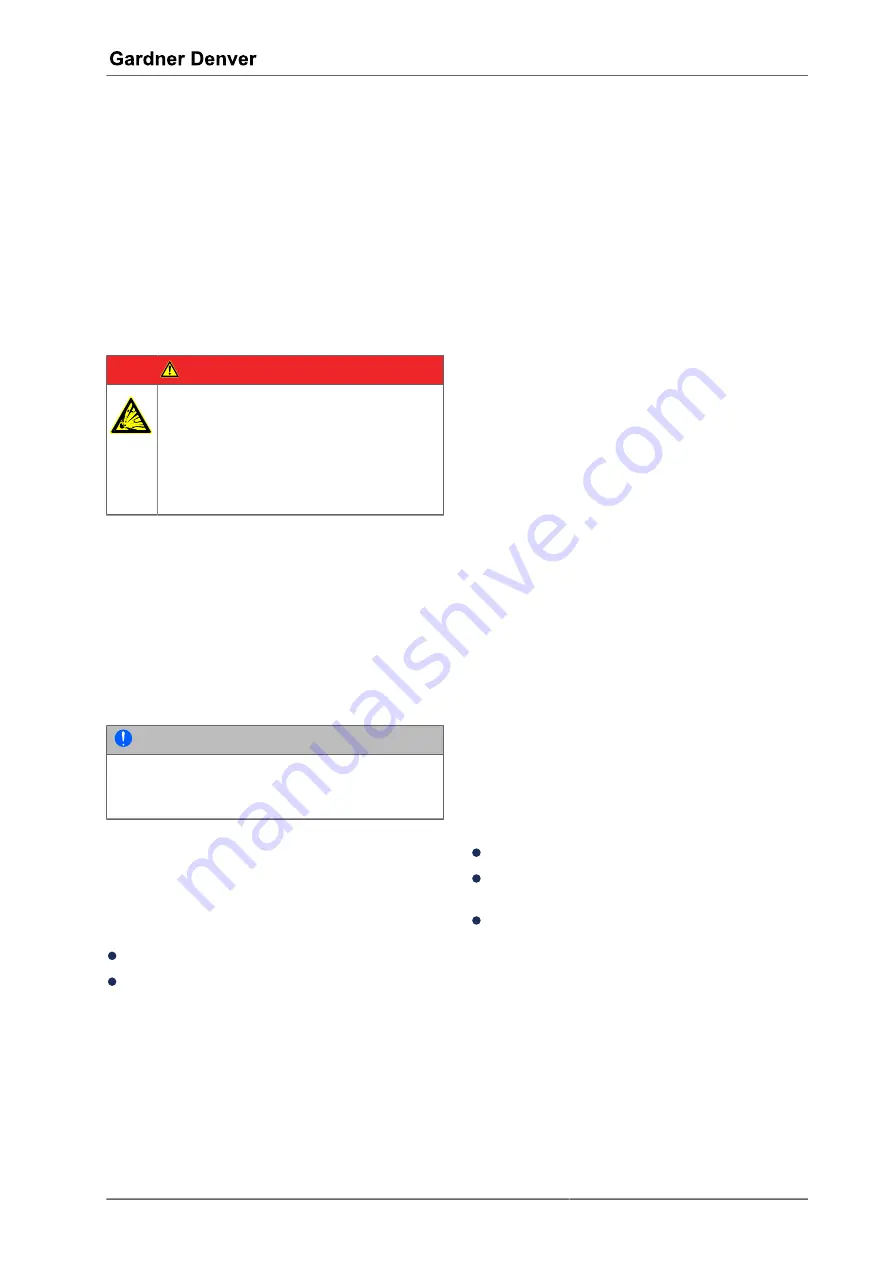
Safety requirements
2
January 2017
America
9 /72
The sound pressure level with sound-dampening
enclosure is about: (See "Technical data".)
During normal operation the compressor may only
be operated with a closed acoustic hood.
Oil, grease, and other chemical substances
Follow the applicable safety requirements when
handling oils, greases, and other chemical
substances.
Use caution when handling hot materials, as there
is a risk of burning or scalding.
Explosive hazard areas
DANGER
Explosion hazard
The compressor is not designed for
operation in explosion hazard areas.
➯
Operation of the compressor in
explosion hazard areas is not
permitted!
2.3
Protective and safety devices
The compressor is equipped with the following
protective and safety equipment.
Prior to commissioning, particularly after
maintenance and repair work, all protective and
safety devices must be installed and checked for
proper function.
In addition, the inspection intervals required in the
country of use must be complied with.
NOTE
Operation of the compressor is permitted only
with complete, functional protective and safety
devices in place.
Emergency stop
The emergency stop button can be used to bring
the compressor to a safe condition in dangerous
situations.
Emergency stop buttons are mounted:
On the control panel of the compressor
Optionally in a pedestal (control console)
Using the emergency stop
1
Press the <Emergency stop> pushbutton.
The compressor is placed in a safe condition.
2
Rectify the fault that was the cause of the
emergency-stop.
See the "Troubleshooting" chapter.
3
Unlock <Emergency-Stop> button.
Turn the pushbutton anticlockwise.
4
Start up the compressor.
See section "Commissioning after a fault" in the
chapter "Commissioning and operation".
Safety valve / non-return valve
The compressor is protected from exceeding the
permissible operating pressure by a safety valve.
The safety valve opens at 15 bar / 218 psi.
The compressor is protected against backpressure
from the compressed air network by means of a
check valve on the pressure side.
Protective covers and enclosure panels
The cooling air fans are covered with protective
mesh.
The coupling between the drive and the
compressor is protected by a mesh guard.
The housing of the compressor is designed so
that any broken parts that may be thrown off are
retained within the compressor.
The compressor housing serves as a sound
protection cover.
2.4
Residual risks
Hot surfaces
Some parts of the compressor become hot in
operation (up to 120 °C / 248 °F). A hazard
warning sign on the compressor enclosure warns
of this danger.
Before beginning maintenance and repair work,
the compressor must have cooled off sufficiently.
Personal protective equipment
We recommend wearing the following personal
protective equipment:
Safety shoes
Safety glasses whenever working with
compressed air and open enclosure
Hearing protection when the sound protection
cover is open
2.5
Labeling of safety instructions
Safety instructions are used as special warning
notices in the operating instructions, using the
following names and symbols.
Summary of Contents for L160 110A V2
Page 1: ...User manual Screw compressor L160 L290 V2 L160RS L290RS V2 America ZS1149274 03 January 2017...
Page 7: ...Foreword 1 January 2017 America 7 72 1 6 Rating plate Fig 1 1 Rating plate...
Page 69: ...Appendix 9 January 2017 America 69 72...
Page 70: ...9 Appendix 70 72 America January 2017...