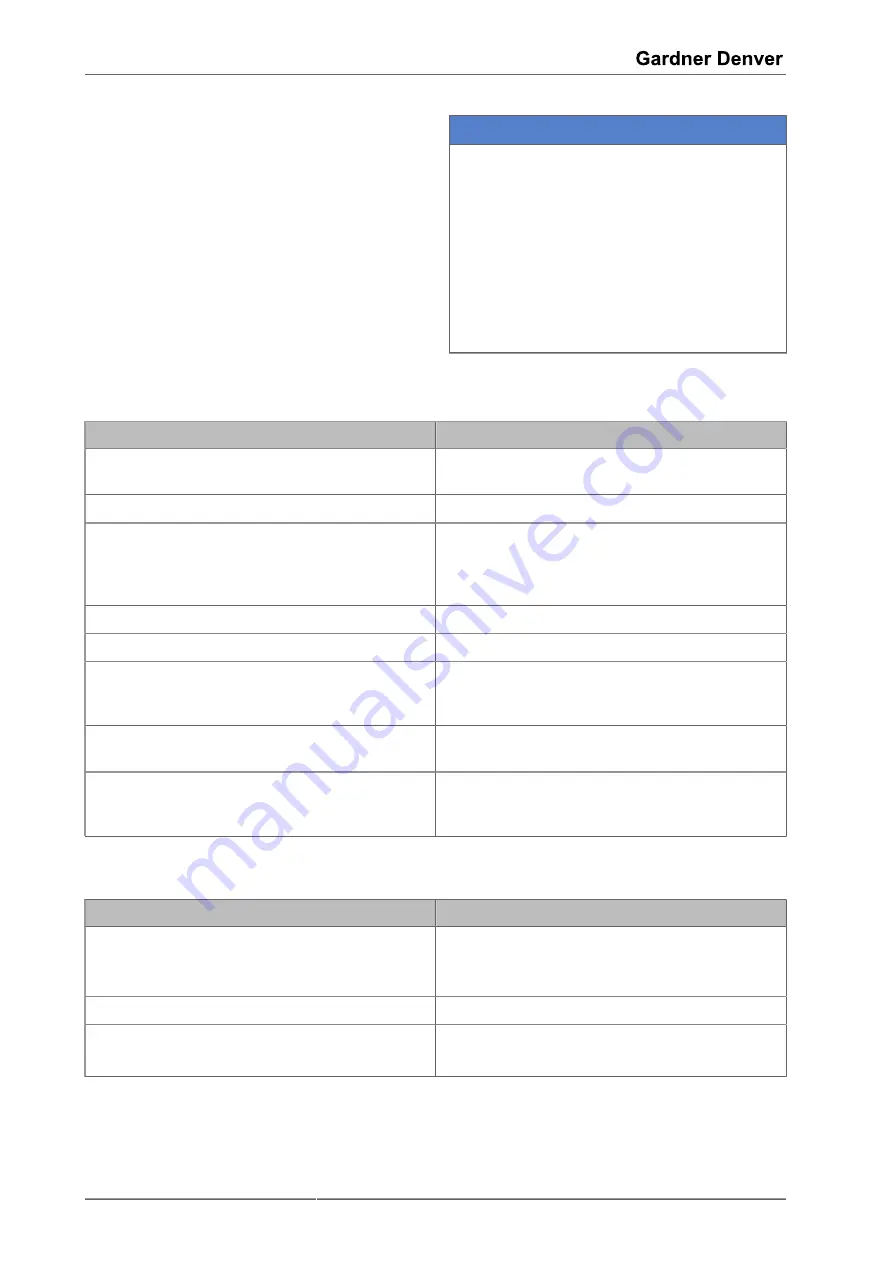
7
Clearing a fault
38 / 72
America
January 2017
7
CLEARING A FAULT
Instructions for clearing a fault
Potential causes and solutions are listed in the
following tables.
The measures listed in these operating
instructions for clearing faults may be performed
only by specially trained personnel. Any other
work beyond this must be performed by the
manufacturer's service personnel! Work on the
electrical equipment may be performed only by
authorized electrical technicians.
Solutions are described in detail in repair
instructions, which are transmitted as part of the
operator training.
NOTICE
Property damage
Property damage due to incorrect/unsuitable
measures for fault clearing.
➯
If the solutions listed here are not sufficient
to clear the fault. Contact Gardner Denver.
➯
For fault and warning messages that are
displayed on the display of the electronic
controller, follow the instructions in the
chapter "Fault clearing" in the operating
instructions for the electronic controller.
Fault: Unit will not start
Potential root cause
Remedy
Missing operating or control voltage
Check fuses, main disconnect switch, and supply
lines.
Fault not acknowledged
Acknowledge a fault in the electronic controller.
Pressure vessel not depressurised.
Wait for depressurisation. Screw compressor does
not start up when the vessel pressure is greater
than the preset value. See factory setting “Start
protection” GD Pilot TS.
Drive motor defective
Check connections, windings, etc.
Compressor defective
Rotate compressor by hand, replace if needed.
Ambient temperature < +1 °C / 33.8 °F
Ensure that the ambient temperature is at least
+1 °C / 33.8°F if necessary provide stationary heat-
ing
The remote control/timer control via terminal strip is
activated
Deactivate remote control/timer control
Line pressure is above the lower switching point
(L160-L290) or the nominal pressure (L160RS-
L290RS)
Wait until the line pressure has fallen below the
switching point / nominal pressure
Chart 7-1: Fault cleared by: Unit will not start
Fault: Unit remains stopped during the run-up phase.
Potential root cause
Remedy
Short circuit in the compressor
Determine and correct the cause of the short cir-
cuit.
Replace defective fuses.
Loose terminal connections
Check terminal connections and tighten if needed.
Switching on and off by hand has exceed the maxi-
mum number of motor switching cycles.
Avoid switching on and off frequently by hand.
Allow the electric motor to cool down.
Chart 7-2: Fault cleared by: Unit remains stopped during the run-up phase.
Summary of Contents for L160 110A V2
Page 1: ...User manual Screw compressor L160 L290 V2 L160RS L290RS V2 America ZS1149274 03 January 2017...
Page 7: ...Foreword 1 January 2017 America 7 72 1 6 Rating plate Fig 1 1 Rating plate...
Page 69: ...Appendix 9 January 2017 America 69 72...
Page 70: ...9 Appendix 70 72 America January 2017...