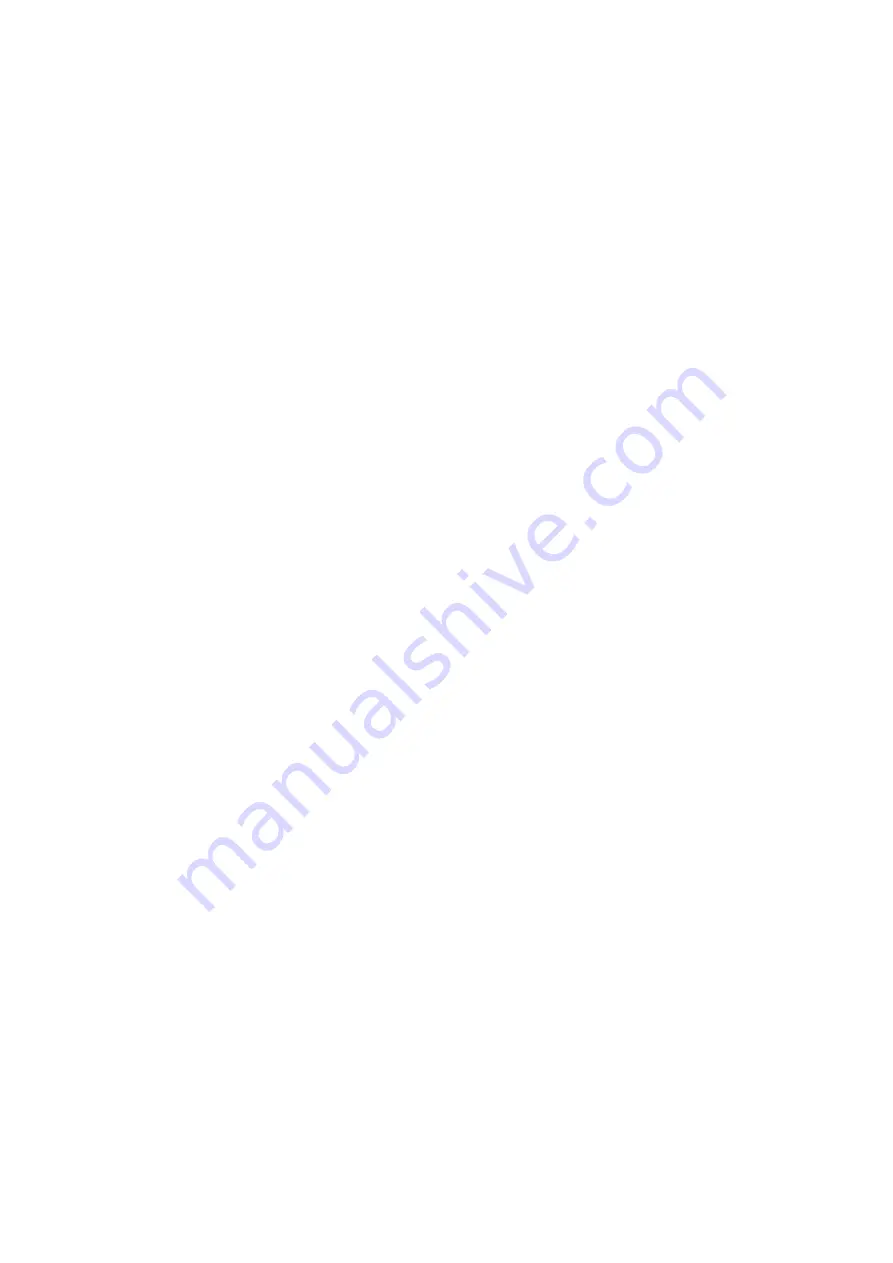
System with speed control (RS) / e variant
Depending on ambient conditions (relative humid-
ity, intake temperature and ambient pressure), the
oil temperature level is regulated using an elec-
tronically controlled regulator. The aim is to pre-
vent the formation of condensation within the oil
circuit and to reach the defined final compres-
sion temperature. In this process, you can choose
between the two modes "AUTO" and "Manual",
whereby as cold a final temperature as possible
is striven for in "AUTO" mode. "MANUAL" mode
should be chosen if as constant a final tempera-
ture as possible is desired, and is especially rec-
ommended if using HRC. In both cases, the con-
trol algorithm reliably prevents undershooting of
the dew point and thus condensation inside the oil
circuit. (Ambient pressure must be set during com-
missioning!)
The oil flows from the pressure vessel (6) through
the cooler bypass pipe directly to the oil filter(s)
(18) and is then injected into the screw compres-
sor (4).
If the oil temperatures reaches the safer level, the
oil flow is divided between oil cooler (15) and by-
pass pipe.
Combined oil circuit
The oil separated in the oil fine separator (7) is
fed back to the compressor through the oil suction
pipe.
The entire oil circuit is based on differential pres-
sure in the system. If the pressure difference in-
side the oil circuit of about 2 bar is allowed for,
then the oil, at a vessel pressure of, for example
10 bar is injected into the screw compressor at
about 8 bar .
During screw compressor off-load operation, a
sufficiently large drop in pressure, and thus the
required oil injection volume, is achieved so that
vacuum pressure is produced at the intake port
and at the injection point when the suction regula-
tor is closed (2).
An overpressure of approx. 1.5 bar (off-load pres-
sure) is simultaneously generated in the pressure
vessel.
3.5
Air circuit
The air drawn in reaches the screw compressor
(-4-) via the suction filter (-1-) and the suction reg-
ulator (-2-). It is cooled by the injected oil dur-
ing the compression process. The ensuing com-
pressed air-oil mixture flows tangentially into the
pressure vessel (-6-). After the pre-separation and
the subsequent fine separation in the fine precipi-
tator (-7-), the low-oil compressed air reaches the
load network via the pressure-retaining and non-
return valve (-12-) and the air cooler (-14-).
3.6
Controller
(also refer to the operating instructions for the
compressor control DELCOS XL)
Unit standstill
•
During unit standstill times, the suction regula-
tor (-2-) is shut by a pressure string on the ad-
justing cylinder (-2.1-).
•
The solenoid valve (-24-(Y1)) is current-free.
•
The pressure vessel is depressurised through
the blow-off valve (-25-) to atmospheric pres-
sure.
•
The cooling water solenoid valve (-32-(Y6)) is
closed in a zero-current state (only L xxx W –
water-cooled systems).
Starting the unit
•
The motor starts up in Y-operation.
•
The cooling water solenoid valve (-32-(Y6)) is
supplied with power and opens (only L xxx W).
•
The suction regulator is shut.
•
The compressor draws in air by means of a
butterfly valve. Pressure builds up in the pres-
sure vessel.
•
Oil is supplied to the screw compressor due to
the drop in pressure between the pressure ves-
sel and the injection point in the screw com-
pressor.
•
When switching the drive motor to Δ-operation,
the solenoid valve (-24-(Y1)) switches, as it is
being supplied with power.
•
The air circulated in the system flows through
the solenoid valve (-24-(Y1)) into the upper
control space of the adjusting cylinder (-2.1-).
The blow-off valve (-25-(Y4)) closes.
•
The butterfly valve (-2.2-) in the suction regula-
tor (-2-) is opened.
•
At a vessel pressure of 4.5 bar, the pres-
sure-retaining and non-return valve (-12-)
opens.
Summary of Contents for L110 10A V4
Page 73: ......