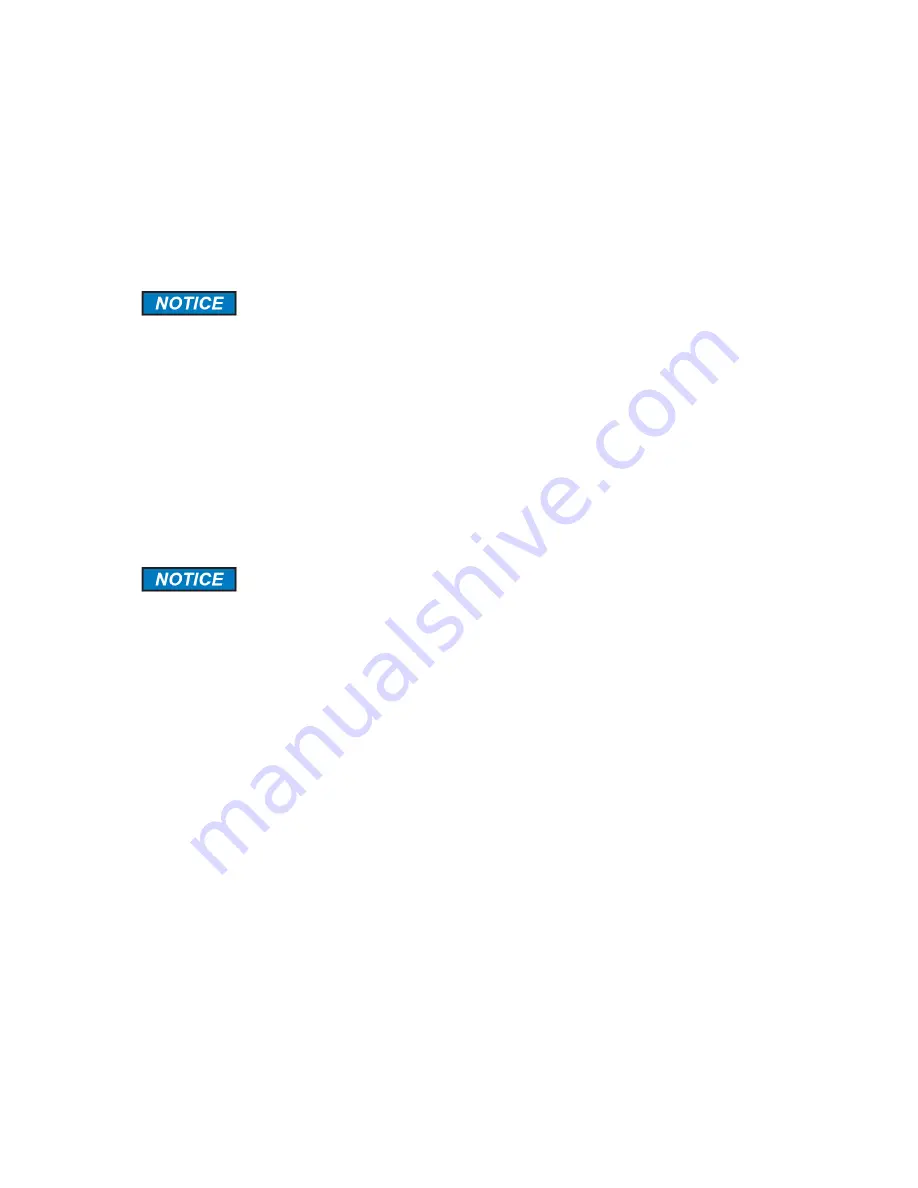
Revision 1
19
9/10/2019
2.4.4 Connection of the Analog Signal Cables
One conduit connector labeled
‘Analog Signals’
is provided on the bottom of the control
cabinet for the signal cable connection as shown in Mounting and Service Connections
drawing,. The
analog output signals
are available at the terminals shown in the
Customer
Signal Outputs
drawing (Section 9). The user may connect to any of all of the available
signals. The shields from the signal cable pair should be connected to the ‘shld’ terminals.
Installation of the conduit, wiring and disconnect devices must comply with
all applicable national, local and user electrical codes.
2.4.5 Connection of the Digital Signal Cables
One conduit connector labeled
‘Digital Signals’
is provided on the bottom of the control
cabinet for the signal cable connections as shown in the Mounting and Service connections
drawing,
The alarm relay contacts are available at the terminals shown in the
Inputs/Outputs
drawing
(Figure 9-3). The relays are shown in the ‘alarm’ state. The user may connect to any or all of
the available signals. The signal cable pair shields should be connected to the ground
terminals provided.
Installation of the conduit, wiring and disconnect devices must comply with
all applicable national, local and user electrical codes. The connection (s)
must be ‘sealed’.
2.4.6 Connection of Instrument Air Services
The installation of the 962-AGX analyzer system requires the connection of instrument air
service to the control cabinet air purge/cooler valve. Instrument air service should be 80 to
100 psig of clean, dry instrument air (ANSI/ISA Standard 57.3-1975 R (1981)). Service to the
analyzer must be capable of a sustained flow of 900 SCFH at 80 to 100 psig.
It is recommended that a particulate filter be installed in the instrument air line before final
connection to the analyzer system valve. Blow down the air lines to remove any possible
debris such as dirt, scale, water, oil, etc., before connection to the analyzer system.
Purging of the control cabinet is required in respect of the hazardous area classification and
to mitigate corrosive element exposure on the system electrical equipment. As soon as
practical, initiate cabinet purge until the analyzer is commissioned by Galvanic Applied
Sciences, Inc.
Summary of Contents for 962-AGX
Page 43: ...Revision 1 43 9 10 2019 Figure 4 13 Network Sub Panel...
Page 86: ...Revision 1 86 9 10 2019 Figure 9 1 Customer Connections...
Page 87: ...Revision 1 87 9 10 2019 Figure 9 2 Analyzer Components...
Page 88: ...Revision 1 88 9 10 2019 Figure 9 3 Inputs and Outputs...
Page 89: ...Revision 1 89 9 10 2019 Figure 9 4 AC Wiring Overview...
Page 90: ...Revision 1 90 9 10 2019 Figure 9 5 DC Wiring Overview...