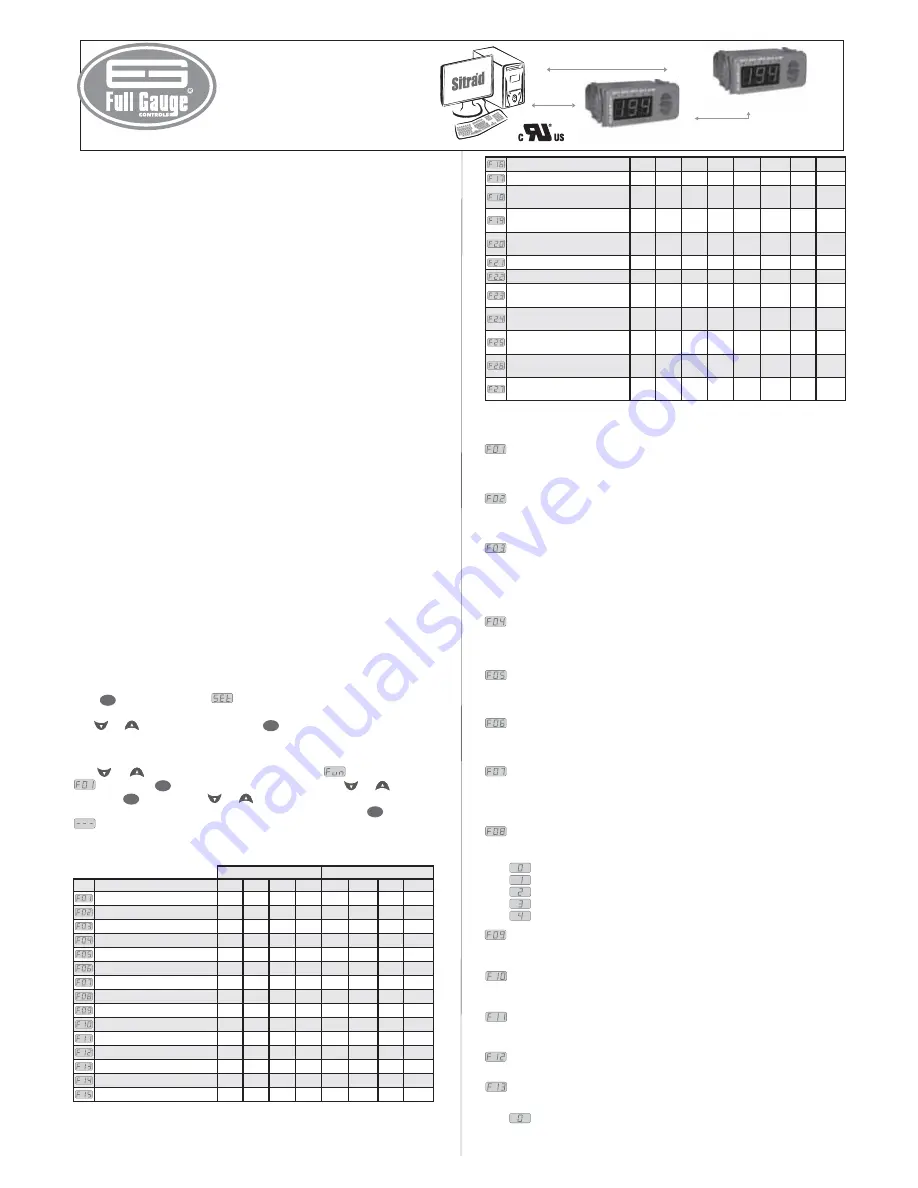
DIGITAL PRESSURE CONTROLLER
FOR COOLING CENTERS
PCT-400Ri plus
DISCHARGE PRESSURE
GAUGE
SUCTION PRESSURE
GAUGE
UL-Underwriters Laboratories
1. DESCRIPTION
The
is a pressure controller to be used in cooling centers that need control over
the suction and discharge stages. Working in pairs, it is possible to control up to four fans and four
compressors at the same time. Through remote communication between suction and discharge
controllers, it is possible to obtain more precise control of the process.
Available in the version for high (discharge) and low (suction) pressures, the
can
operate in conjunction with another, or on its own.
With four pressure control outputs and remote communication, the
allows the
discharge pressure gauge to turn off the suction pressure gauge due to an alarm situation. Because it is
very versatile, it management the activation of the charges linearly, by rotation or by capacities. Through
serial output, the RS-485 allows communication with
software, which makes its configuration
simple and fast.
PCT-400Ri plus
PCT-400Ri plus
PCT-400Ri plus
SITRAD
For use with refrigeration processes controlling the system’s compressors (suction) or fans (discharge).
®
2. APPLICATION
3. TECHNICAL SPECIFICATIONS
- Power supply:
- Control pressure:
- Resolution:
- Maximum current:
- Dimensions:
- Controller operating temperature:
- Transducer operating temperature:
- Operating humidity:
- Control outputs:
12Vac/dc (with external energy source 127/220Vac ±10% (50/60Hz))
0 to 100 psi / 0 to 6.9 bar (using the SB69-100V transducer)
0 to 500 psi / 0 to 34.4bar (using the SB69-500V transducer)
1 psi / 0.1bar
5(3)A/ 250Vac 1/8HP (each output)
71 x 28 x 71mm
0 to 50 ºC
-40 to 125°C
10 to 90% RH (without condensation)
OUT1 - Output for the first pressure control stage
OUT2 - Output for the second pressure control stage
OUT3 - Output for the third pressure control stage
OUT4 - Output for the fourth pressure control stage
ALRM - Led for indicating alarms
4. CONFIGURATIONS
Attention
At first select the pressure measure unit (item 7) and the kind of pressostat (item 8) that you want to
work. It is very important select it to keep your configuration, if you do not do that the instrument returns
the standard configuration, now it is ready to select the setpoint.
4.1 - Control presssure adjust (SETPOINT)
4.2 - To enter into the functions menu
- Press
for 2 seconds until appears
, and release it after that. The adjusted operation pressure
will appear.
- Use
and
to change the value and then press
to record it.
Press
and
simultaneously for two seconds until it appears,
then releasing it. When
appears, press
(short hit) and enter the code (123) through keys
and
. To confirm,
press the key
. Through the keys
and
access the other functions and proceed in the same
manner to adjust them. To leave the menu and return to normal operations, press
(long hit) until
appears.
SET
SET
SET
SET
SET
4.3 - Parameters table
Description
Min
Max
Unit
SUCTION
Fun
Min
Max
DISCHARGE
Access code (123)
Indication Offset
Control differential (hysteresis)
Minimum Setpoint allowed for the end user
Maximum Setpoint allowed for the end user
Low pressure alarm
High pressure alarm
Automatic rearm after alarm
Startup delay (activation)
Time for blocking the alarm
Delay for proving alarm situation
Number of stages
Operating Mode for the Stages
Capacity of the compressor/stage 1
Capacity of the compressor/stage 2
-99
-5 / -0.3
1 / 0.1
0 / 0.0
0
0
0
0
/ 0.0
/ 0.0
0 / 0.0
0
0
1
0
0
0
999
5 / 0.3
100 / 6.9
100 / 6.9
100 / 6.9
100 / 6.9
100 / 6.9
4
999
999
999
4
2
100
100
-
psi / bar
psi / bar
psi / bar
psi / bar
psi / bar
psi / bar
-
sec.
sec.
sec.
-
-
%
%
-99
-20 / -1.4
1 / 0.1
0 / 0.0
0 / 0.0
0 / 0.0
0 / 0.0
0
0
0
0
1
0
0
0
999
20 / 1.4
100 / 6.9
500 / 34.4
500 / 34.4
500 / 34.4
500 / 34.4
4
999
999
999
4
2
100
100
Unit
-
psi / bar
psi / bar
psi / bar
psi / bar
psi / bar
psi / bar
-
sec.
sec.
sec.
-
-
%
%
0
0 / 0.0
10 / 0.7
0 / 0.0
500 / 34.4
0 / 0.0
500 / 34.4
0
0
0
1
4
0
25
25
Standard
Standard
0
0 / 0.0
4 / 0.4
0 / 0.0
100 / 6.9
0 / 0.0
100 / 6.9
0
0
0
1
4
0
25
25
Capacity of the compressor/stage 3
Capacity of the compressor/stage 4
Outputs' state when a sensor error is
detected
Minimum time between activation of 2
different stages
Minimum time between deactivation 2
different stages
Minimum time of stage activated
Minimum time of stage deactivated
Maximum operating time between
maintenances on the stage 1
Maximum operating time between
maintenances on the stage 2
Maximum operating time between
maintenances on the stage 3
Maximum operating time between
maintenances on the stage 4
Address of the equipment on the network
RS-485 (serial communication)
0
0
0
0
0
0
0
0
0
0
0
1
100
100
15
999
999
999
999
999
999
999
999
247
%
%
-
sec.
sec.
sec.
sec.
x10h
x10h
x10h
x10h
-
25
25
0
2
1
1
1
999
999
999
999
1
0
0
0
0
0
0
0
0
0
0
0
1
100
100
15
999
999
999
999
999
999
999
999
247
%
%
-
sec.
sec.
sec.
sec.
x10h
x10h
x10h
x10h
-
25
25
0
2
1
1
1
999
999
999
999
1
4.4 - Parameters description
Access code (123)
Indication Offset
Control differential (hysteresis)
Minimum Setpoint allowed for the end user
This will be necessary for changing the configuration parameters. This code will not be necessary for
only viewing the adjusted parameters.
Allows compensation for any deviations on the pressure reading resulting from a change of the
sensor.
Is the value of the relative pressure that defines the pressure range within which the control stages
should be activated. The points on which each stage will be activated depend on functions F12
(number of stages) and F13 (operating mode for the stages). The minimum value of the hysteresis is
the number of stages configured in F12.
Lower limit, the purpose of which is to avoid any accidental regulation of pressures at levels that are
exaggeratedly below the setpoint.
Maximum Setpoint allowed for the end user
Low pressure alarm
High pressure alarm
Automatic rearm after alarm
Upper limit, the purpose of which is to avoid any accidental regulation of pressures at levels that are
exaggeratedly above the setpoint.
This is the value of the reference pressure for activating the low pressure signal when below the
desired point.
This is the value of the reference pressure for activating the high pressure signal when above the
desired point. In the event that the pressure gauge is configured as a discharge, a remote high
pressure alarm should also be sent to the suction pressure gauge, so that it deactivates its outputs.
This function defines how the pressure gauge will behave after the remote alarm situation stops.
Only accepts manual rearms, even after remote alarm situations stop
The controller only performs one automatic rearm
The controller only performs two automatic rearms
The controller only performs three automatic rearms
The controller only performs automatic rearms
Startup delay (activation)
Time for blocking the alarm
Delay for proving alarm situation
Number of stages
Operating Mode for the Stages
Linear Mode:
Time counted from the initialization wherein the instrument only shows the pressure without
activating either the alarm or the stages.
This is the time that the alarm will remain deactivated, even under alarm conditions. This block time
starts to be counted after the startup delay count has ended (F09).
Alarm blocking time to distinguish between one of the alarm situations or a transitory condition of the
system.
Function that indicates which stages will be activated.
Function that selects the method for activating the stages.
In this mode of operation, the controller activates compressors as the
pressure of the line moves away from the setpoint. The activation point for each compressor is
calculated in accordance with the value of the hysteresis (F03) and the number of stages
configured (F12).
Ver.03
PCT400V03-01T1
1273