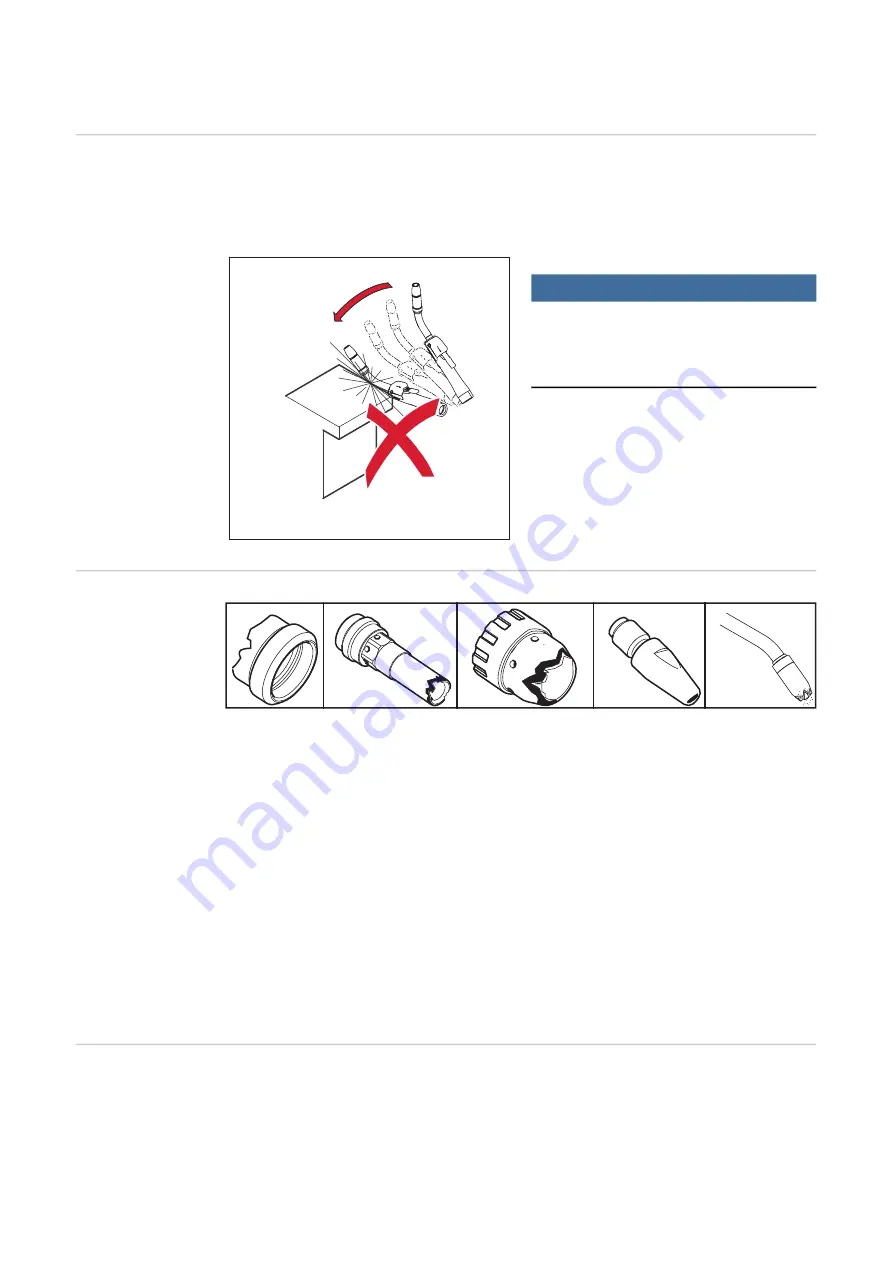
14
Care, maintenance and disposal
General
Regular preventive maintenance of the welding torch is essential if trouble-free operation
is to be ensured. The welding torch is subjected to high temperatures and heavy soiling.
The welding torch therefore requires more frequent maintenance than other components
in the welding system.
NOTE!
When removing welding spatter, avoid
scoring or scratching the torch.
Future welding spatter may become firmly
lodged in score or scratch marks.
Do not bend the torch body under any cir
-
cumstances!
Recognising
faulty wearing
parts
1. Insulating parts
–
Burned-off outside edges, notches
2. Nozzle fittings
–
Burned-off outside edges, notches
–
Heavily covered in welding spatter
3. Spatter guard
–
Burned-off outside edges, notches
4. Contact tips
–
Worn-out (oval) wire entry and wire exit holes
–
Heavily covered in welding spatter
–
Fusion penetration on the tip of the contact tube
5. Gas nozzles
–
Heavily covered in welding spatter
–
Burned-off outside edges
–
Notches
Maintenance at
every start-up
-
Check wearing parts
-
replace faulty wearing parts
-
Remove welding spatter from gas nozzle
1.
2.
3.
4.
5.
Summary of Contents for MTG 320i
Page 2: ...2 ...
Page 4: ...4 ...
Page 13: ...13 EN 1 3 ...
Page 22: ...22 ...
Page 24: ...24 ...
Page 33: ...33 ES 1 3 ...
Page 42: ...42 ...
Page 44: ...44 ...
Page 53: ...53 FR 1 3 ...
Page 62: ...62 ...
Page 63: ...63 FR ...