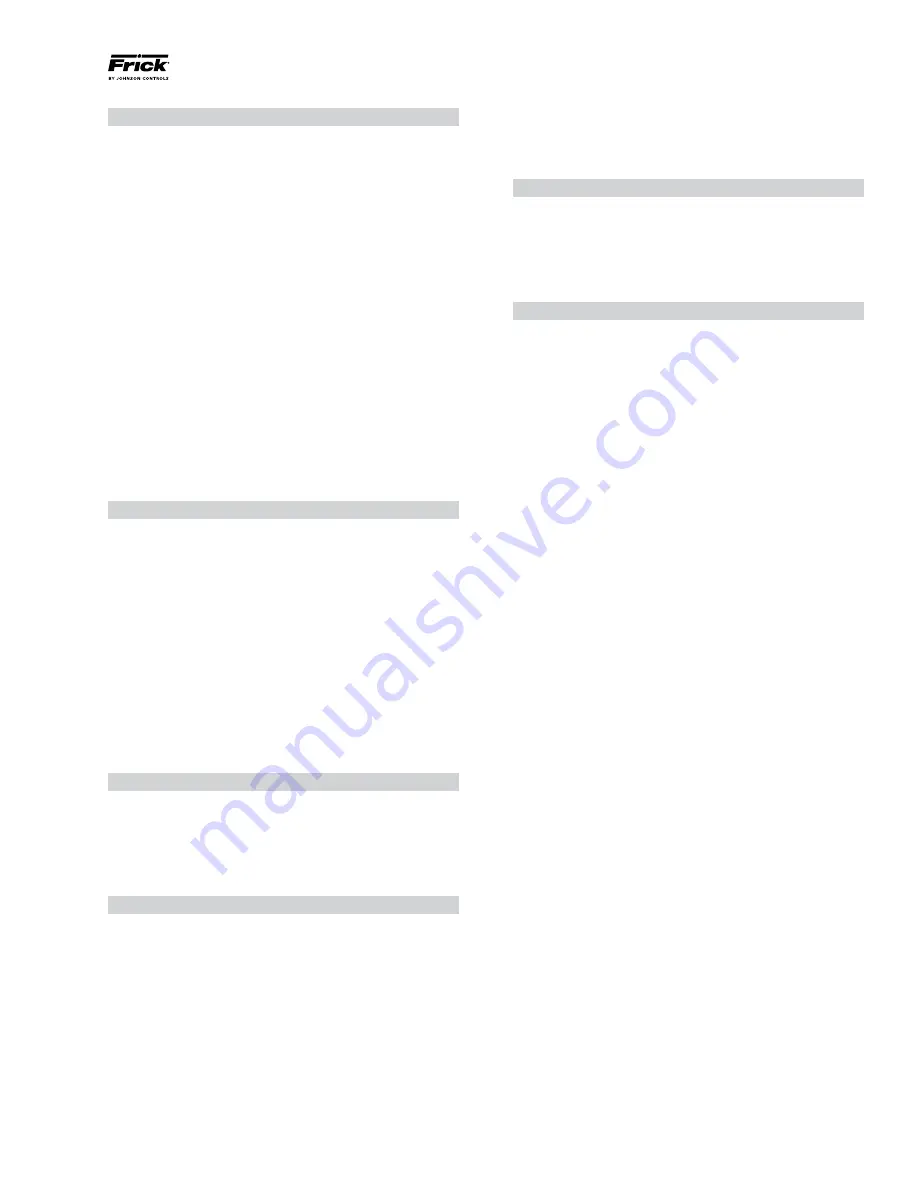
VYPER
™
VARIABLE SPEED DRIVE
MAINTENANCE
100-210 IOM (
JUL
09)
Page 61
Fault 10: Harmonic Filter - High Total Demand Distortion
Message
Quantum: “Fault 10”
Quantum LX: “Harmonic Filter High Total Demand Distortion’’
This shutdown indicates that the filter is not operating cor-
rectly or the input current to the Vyper™/filter system is not
sinusoidal. This fault occurs when any one of the three phases
of Total Demand Distortion (TDD) is greater than 25.0 %,
for forty-five continuous seconds while the Vyper™ is run-
ning. TDD is defined by the IEEE Std 519-1992 standard as
“the total root - sum - square harmonic current distortion, in
percent of the maximum demand load current (15 or 30 min
demand)”. In the filter option supplied by Frick, the displayed
TDD is the total RMS value of the harmonic current supplied
by the power mains to the Vyper™ system divided by the
FLA of the Vyper™, in percent. The harmonic filter option
was designed to provide an input current TDD level of 8%
or less for the Vyper™ system. A standard Vyper™ less the
optional filter typically has an input current TDD level on the
order of 28 - 30%. Causes for this shutdown are numerous,
but would most likely be caused by a faulty filter logic board.
In order to initiate a chiller run again, the Quantum™LX
panel’s compressor switch must first be placed into the
STOP/RESET position.
Fault 11: High Phase B Inverter Baseplate Temperature
Message
Quantum: “Fault 11”
Quantum LX: “High Phase B Inverter Baseplate Temperature”
The phase bank assembly shall contain one heat sink to cool
the three inverter power modules and the converter SCR/
Diode modules. The inverter power modules each contain
an internal temperature sensor (5K ohm at 25°C) to monitor
their baseplate temperatures. Each of the inverter power
module baseplate temperatures are compared in software
to a limit of 175°F (79°C). If this limit is exceeded, the unit
initiates a safety shutdown. The fan(s) and water pump re-
main energized until the inverter power module baseplate
temperature falls below 165°F (74°C). The fans and pumps
are de-energized when all baseplate temperatures drop
below the reset thresholds.
Fault 12: High Phase C Inverter Baseplate Temperature
Message
Quantum: “Fault 12”
Quantum LX: “High Phase C Inverter Baseplate Temperature”
Same comments as Fault 11 except applying to Phase C
Inverter Baseplate Temperature
Fault 13: Low Phase B Inverter Baseplate Temperature
Message
Quantum: “Fault 13”
Quantum LX: “Low Phase B Inverter Baseplate Temperature”
The phase bank assembly shall contain one heat sink to
cool both the inverter power module and the converter SCR/
Diode modules. The three inverter power modules each
contain internal temperature sensors (5K ohm at 25°C) to
monitor baseplate temperature. The inverter power module
baseplate temperatures are compared in software to a
lower limit of 37°F (2.8°C). If this limit is exceeded, the unit
initiates a cycling shutdown. In addition, if the three inverter
baseplates and the converter heat sink temperature falls
below the 37°F limit, the unit will trip and energize the fan(s)
and coolant pump. This feature provides service personnel
with a means to run the water pump while filling the cooling
system (by pulling VSD logic board plug P2).
Fault 14: Low Phase C Inverter Baseplate Temperature
Message
Quantum: “Fault 14”
Quantum LX: “Low Phase C Inverter Baseplate Temperature”
Same comments as Fault 13 except applying to Phase C
Inverter Baseplate Temperature
Fault 17: High Phase A Instantaneous Current
Message
Quantum: “Fault 17”
Quantum LX: “VSD High Phase A Instantaneous Current”
The three output lines to the motor are monitored via three
current transformers within the drive. The unit’s three phases
of instantaneous output current are compared to a prescribed
limit which is contained in hardware. If the peak current limit
is exceeded, the unit will trip and the Quantum
™
LX Panel will
display a fault message.
The Vyper
™
Logic board generates this shutdown. If any
single phase of motor current, as measured by the output
current transformers, exceeds 1890 Amps peak for 700 HP
/ 3093 Amps peak for 912 HP, a shutdown will occur. If an
Instantaneous Current occurs, but the chiller restarts and
runs without a problem, the cause may be attributed to a
voltage sag on the utility power feeding the Vyper
™
that is in
excess of the specified dip voltage for this product. This is
especially true if the chiller was running at or near full load.
If there should be a sudden dip in line voltage, the current
to the motor will increase, since the motor wants to draw
constant horsepower. This is a common problem when a
second chiller is started. Contact Frick factory service if this
is confirmed to be a problem.
If the chiller will not restart, but keeps tripping on this same
shutdown, then it is possible that the Vyper
™
power unit is the
problem. Check that all six red LEDs are illuminated on the
Vyper
™
gate driver board. Also, check for output short-circuits
using an ohm-meter set to the minimum ohms scale. Measure
from T1 to the Positive Bus and from T1 to the Negative Bus,
checking with the ohm-meter in both polarities. Repeat this
same check for T2 and T3.
If no short circuits are discovered in the Vyper
™
power unit,
the motor may be the problem. Meg the motor phase to phase
and phase to ground. Also verify that the compressor is free
to rotate. A seized compressor will also cause an overcur-
rent fault. If still no short circuits are discovered there is a
Vyper
™
Logic board problem. This is especially true if the trip
occurs during start-up, before the motor begins to turn. If this
is the case, it is possible to monitor the motor current during
start-up on the Logic board. Using an oscilloscope, connect
the ground clip to the GND test point on the board. Connect
the probe tip to the top of one of the three CT terminating
resistors R1, R2 or R3. If a trip occurs and no signal ap-
pears at the input, is definitely a Logic board problem. If the
problem cannot be ascertained using and oscilloscope and
the problem fits this description exactly, replace the Vyper
™
Logic board to see if this corrects the problem.