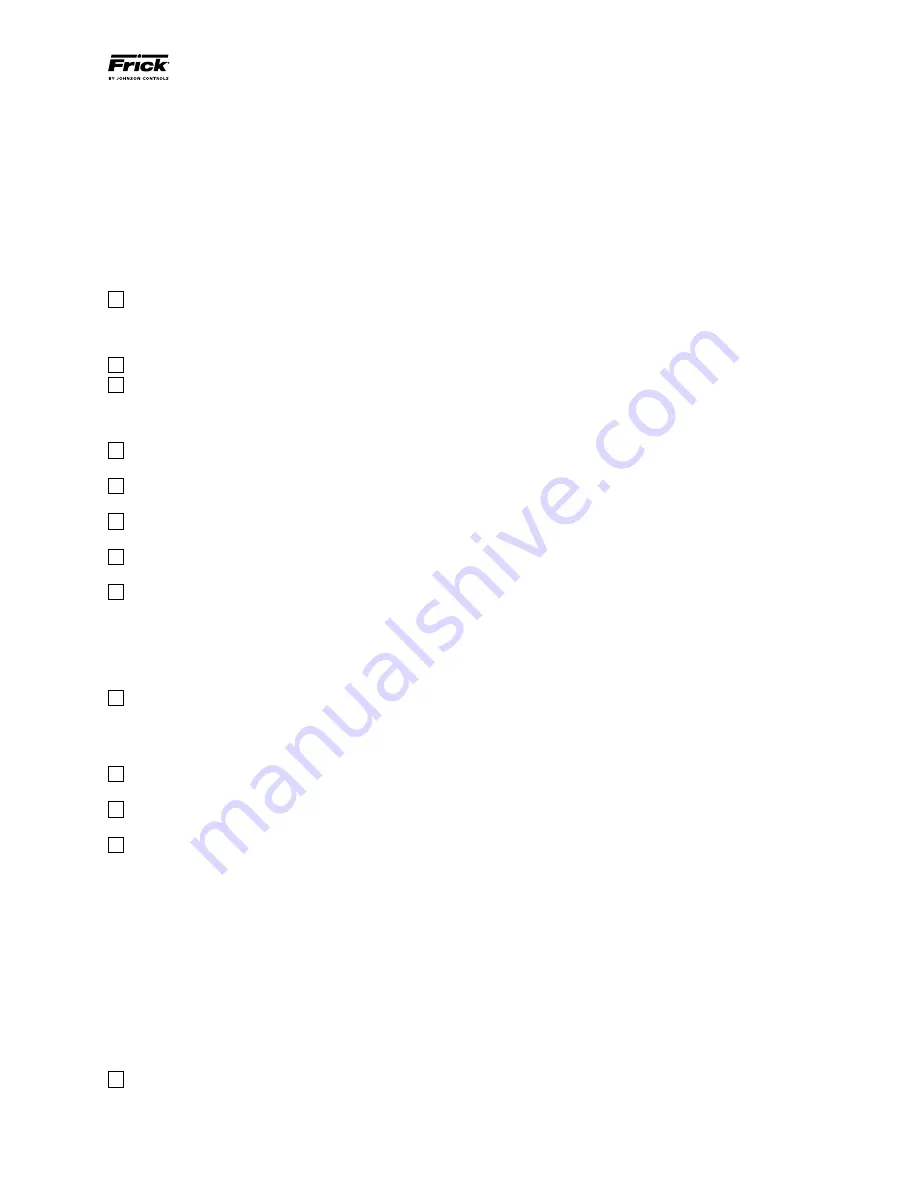
VYPER
™
VARIABLE SPEED DRIVE
INSTALLATION
100-200 IOM (FEB 09)
Page 5
Read This First
Vyper Pre-Installation and Pre-Operation Checklist
The following items MUST be checked and completed by the installer prior to the arrival of the Frick Field Service Supervisor.
Details on the checklist can be found in the I.O.M. Certain items on this checklist will be re-verified by the Frick Field Service
Supervisor prior to the actual start-up.
Vyper Pre-Installation Site Check list
Before attempting to install a Vyper Drive system, please perform a site inspection to assure that the following requirements
are met. (Where Applicable)
-- Verify that the coolant (water or glycol) is available for the Vyper heat exchanger connections. Hard-pipe the coolant sup-
ply in accordance to all local and national piping codes. Sufficient coolant flow and temperature levels must be available to
the Vyper VSD at installation. When hard-piping the coolant supply, take into consideration that room is required in order to
add coolant to the system.
-- Verify that the compressor package temperature sensors are RFI suppression type (639A0151G01).
-- Incoming power cables must enter through the access plate supplied on the top left side of the unit. This access plate
MUST BE removed, entry holes made in the plate, and then reinstalled. Power cables MUST BE in accordance with local
and national electrical codes and current safety standards. See the Power Wiring section of the S100-200 or S100-210
IOM.
-- Verify that the power cable lengths from the Vyper to the compressor motor do not exceed 50 feet (15 meters) and the
location of the Vyper is suitable for mounting.
-- Verify that the motor is suitable for Inverter duty service: 20-100% Speed (12-60 hZ) or 50-100% (30-60 hZ) The motor
must have thermal protection per NEC 2005. (RTD, Thermostat, Thermistor).
-- Verify that the ambient temperature remains within the recommended operating range of 40-135°F (4-57°C). If the drive is
to operate below 40°F (4°C), provide enclosure ambient space heating.
-- Verify that all wiring is contained in metallic conduit. Use of PVC or other materials is not acceptable UNLESS shielded UL
rated power cable is used. Follow recommendations in this manual and Frick publication
S90-400 SB.
-- Verify that all control power (120 VAC), communications / analog wiring, and 460 VAC power are in separate metallic con-
duits. Properly shielded and grounded analog cables are not required to be in EMT.
Vyper Pre-Operation Site Check list
Prior to Quantum
™
LX setup and starting operation of the Vyper Drive system, review the following checklist to ensure all instal-
lation requirements are met. (Where Applicable)
-- Environmental:
A: Cleanliness – Keep panel doors closed and ensure that construction debris is kept out of the cabinet.
B: Use the conduit knockouts provided. Avoid metal shavings in the drive enclosure.
C: Clean out all debris with a low power magnet or a vacuum cleaner.
-- Mounting: Verify that the Vyper Drive is properly mounted: to the floor or wall for remote mounts or to the package for
package mounted units.
-- Verify that the primary water or glycol coolant supply is connected to the heat exchanger at the recommended flow and
temperature recommendations.
-- Wiring (use Frick publicaton S90-400 SB as a guideline):
A: Wiring from the drive to the motor must be enclosed in a grounded metal conduit even if poured in a concrete floor.
Use of PVC or other materials is not acceptable UNLESS shielded UL rated power cable is used.
B: Separate grounded metal conduits must be provided for input power, output power, and control wiring. Failure to provide
separate conduits could result in disruption of other electrical devices due to harmonics and RFI / EMI generated in the
drive.
C: Bond all conduit to the cabinet.
D: Protect control wires (analog and digital) from noise. Use properly shielded and grounded analog control wires. Digital
and analog control wiring must be separate from each other as well as separate from 3 phase control and power wiring.
Noisy input signals will cause erratic drive operation.
E: Verify control wiring has been connected from the Quantum
™
LX panel to the Vyper in accordance with the engineering
drawings for the specific installation.
F: Verify power wiring has been connected at the correct connection points and properly seated in accordance with the
provided engineering drawings for the specific installation.
-- Drain the shipping coolant from the Vyper and properly dispose. Replace with running coolant (pink) and purge air from
the cooling system. Refer to the “Adding and Replacing Coolant” portion of the S100-200 or S100-210 IOM.