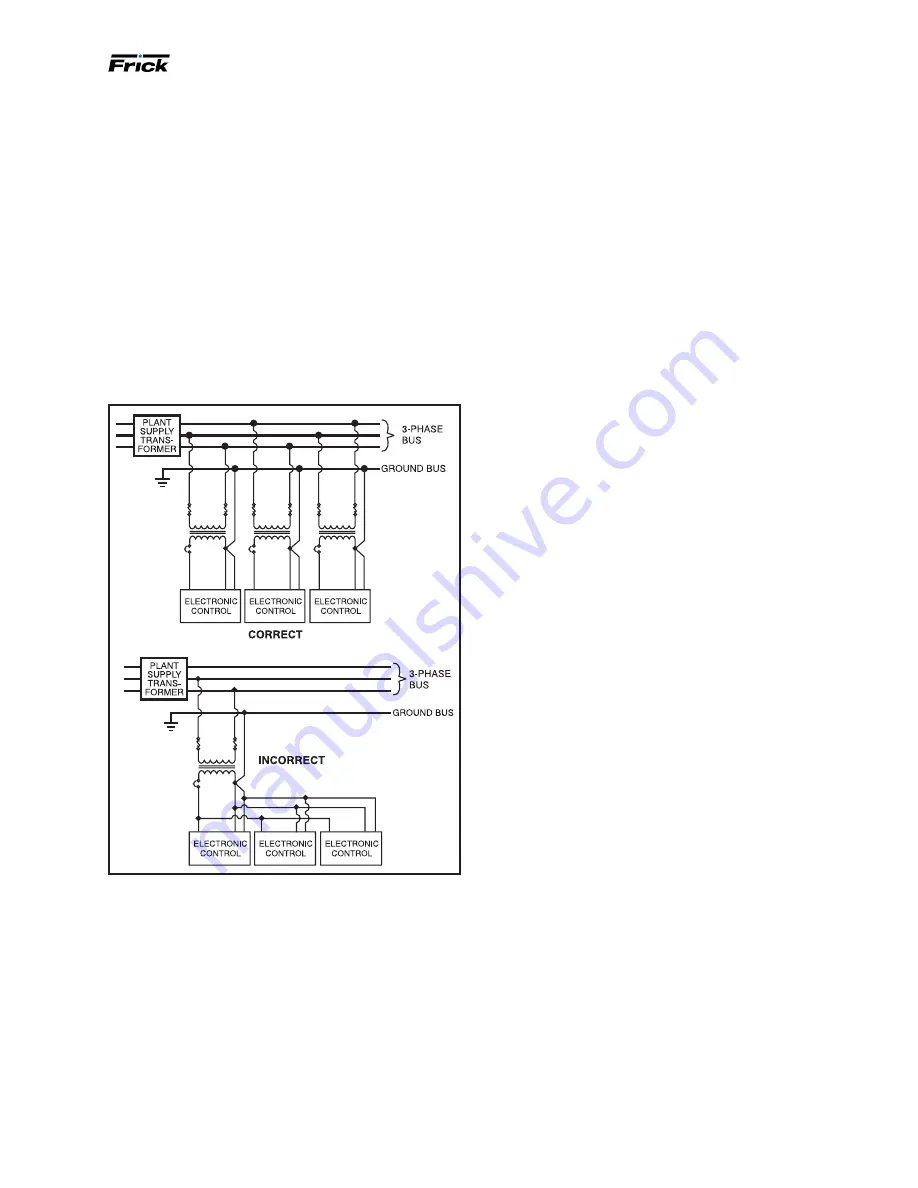
HPS Rotary Screw Compressor Units
070.700-IOM (MAR 21)
Page 19
Installation
If the electronic control panel has a starter built into
the same panel, be sure to run the higher voltage wires
where indicated by the manufacturer.
EMI from the
wires can interfere with the electronics if run too close to
the circuitry.
Never daisy-chain or parallel-connect power or ground
wires to electronic control panels.
Each electronic
control panel must have its own control power supply and
ground wires back to the power source (Plant Transform
-
er). Multiple electronic control panels on the same power
wires create current surges in the supply wires, which
may cause controller malfunctions. Daisy-chaining ground
wires, taking them to ground at each device, allows
ground loop currents to flow between electronic control
panels which also causes malfunctions. See the following
figure.
Figure 24: Daisy-chain wiring example
Communications
The use of communications such as serial and ethernet
in industrial environments are commonplace. The cor-
rect installation of these networks is as important to the
operation of the communications as all of the preceding
practices are to the equipment.
Serial communications cable needs to be the appropri-
ate gauge based on the total cable distance of the run.
Daisy-chaining is the only acceptable style of running the
communications cable. While Star Networks may use less
cable, they more often than not cause problems and inter-
ruptions in communications, due to varying impedances
over the varying lengths of cable. Ground or drain wires of
the communications cable are to be tied together at each
daisy-chain connection and only taken to ground in the
central control system panel.
It is important to carefully consider the type of cable to be
used. Just because a cable has the correct number of con-
ductors and is shielded does not mean it is an acceptable
cable. Johnson Controls-Frick suggests the use of Belden
#9829 for RS-422 communications and Belden # 9841 for
RS-485 up to 2000 ft (609.6 m) total cable length. Refer to
Frick drawing
649D4743
for more detail.
Comm Port Protection:
Surge suppression for the comm
ports may not be the best method, because suppression
is required to divert excess voltage/current to ground. The
success of these devices is dependent on a good ground
(covered earlier in this section). This excess energy can be
quite high and without a suitable ground, can access and
damage the port.
Isolation or Optical Isolation is the preferred comm port
protection method. With optical isolation, there is no con-
tinuity between the communications cable and the comm
port. There is no dependence on the quality of the ground.
Be sure to know what the
voltage isolation value of the
optical isolator is before selecting it. These may range
from 500 V to 4000 V.
Frick Optical Isolation Kits are available, part number
639C0133G01. One kit is required for each comm port.
UPS power and Quantum
™
HD
panels
Johnson Controls, Inc. does not advise nor support the
use of uninterrupted power supply systems for use with
the Quantum
™
HD panel. With a
UPS system providing
shutdown protection for a Frick Quantum panel, the panel
may not see the loss of the 3-phase voltage on the motor
because the UPS may prevent the motor starter contac-
tor from dropping out. With the starter contactor still
energized, the compressor auxiliary continues to feed an
“okay” signal to the
Quantum
™
HD panel. This may allow
the motor to be subjected to the fault condition on the
3-phase bus.
A couple of fault scenarios are: 1. The 3-phase bus has
power “on” and “off” in a continuous cycle manner which
may cause the motor to overheat due to repeated exces-
sive in-rush current experiences. 2. The motor cycling may
damage the coupling or cause other mechanical damage
due to the repeated high torque from rapid sequential
motor “bumps.” 3. Prolonged low voltage may cause the
motor to stall and possibly overheat before the motor
contactor is manually turned off.
Under normal conditions, the loss of 3-phase power shuts
down the Quantum
™
HD panel, restarting upon power
return.
•
Auto
– The
compressor motor starts running as pro
-
grammed.
•
Remote
– The external controller would reinitialize the
panel and proceed to run as required.