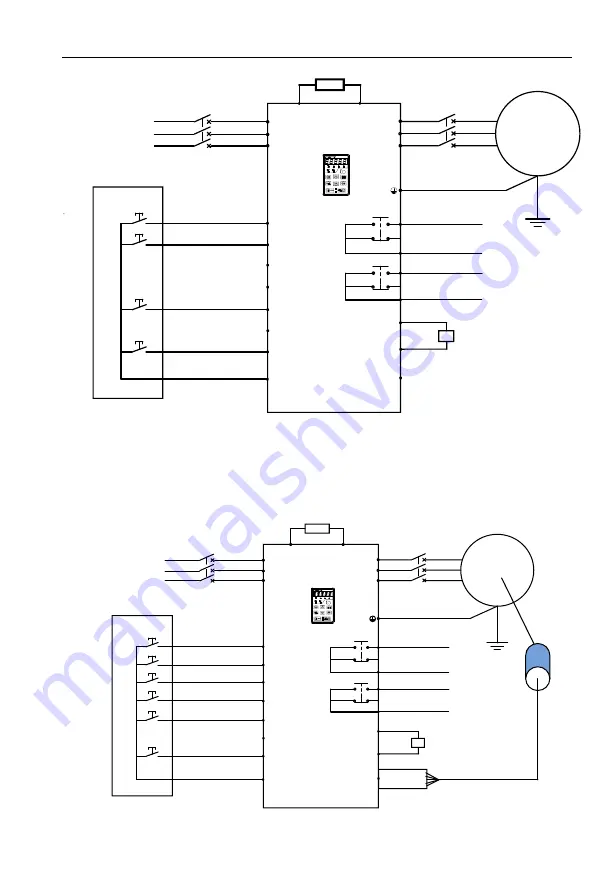
FR500D Series Special Purpose Inverter for Elevator
- 13 -
R
T
U
V
W
M
R1A
R1B
R1C
DI1
Up
Brake
FR500D
S
3-Phase 380VAC
DI2
Down
DI3
DI4
DI5
Inspection
R2A
R2B
R2C
KM2
KM2
DI6
Base Block
+
PB
Resistance
24V
Y1
DI7
COM
COM
Fault
Elevator
Controller
KM1
Fig. 2-3 Inspection mode
2.5 Closed Loop Vector Control
FR500D series supports closed vector control, providing kinds of PG card to different encoder,
please refer to Chapter 5 for PG card details. And please refer to the wiring as below:
R
T
U
V
W
M
R1A
R1B
R1C
DI1
Up
Brake
FR500D
S
3-Phase 380VAC
DI2
Down
DI3
High Speed
DI4
DI5
Inspection
R
2
A
R
2
B
R
2
C
KM2
KM2
DI6
Base Block
+
PB
Resistance
24V
Y1
DI7
COM
Fault
Elevator
Controller
KM1
Leveling Speed
Encoder
PG Card
Fig. 2-5 Wiring of inverter with closed loop vector control