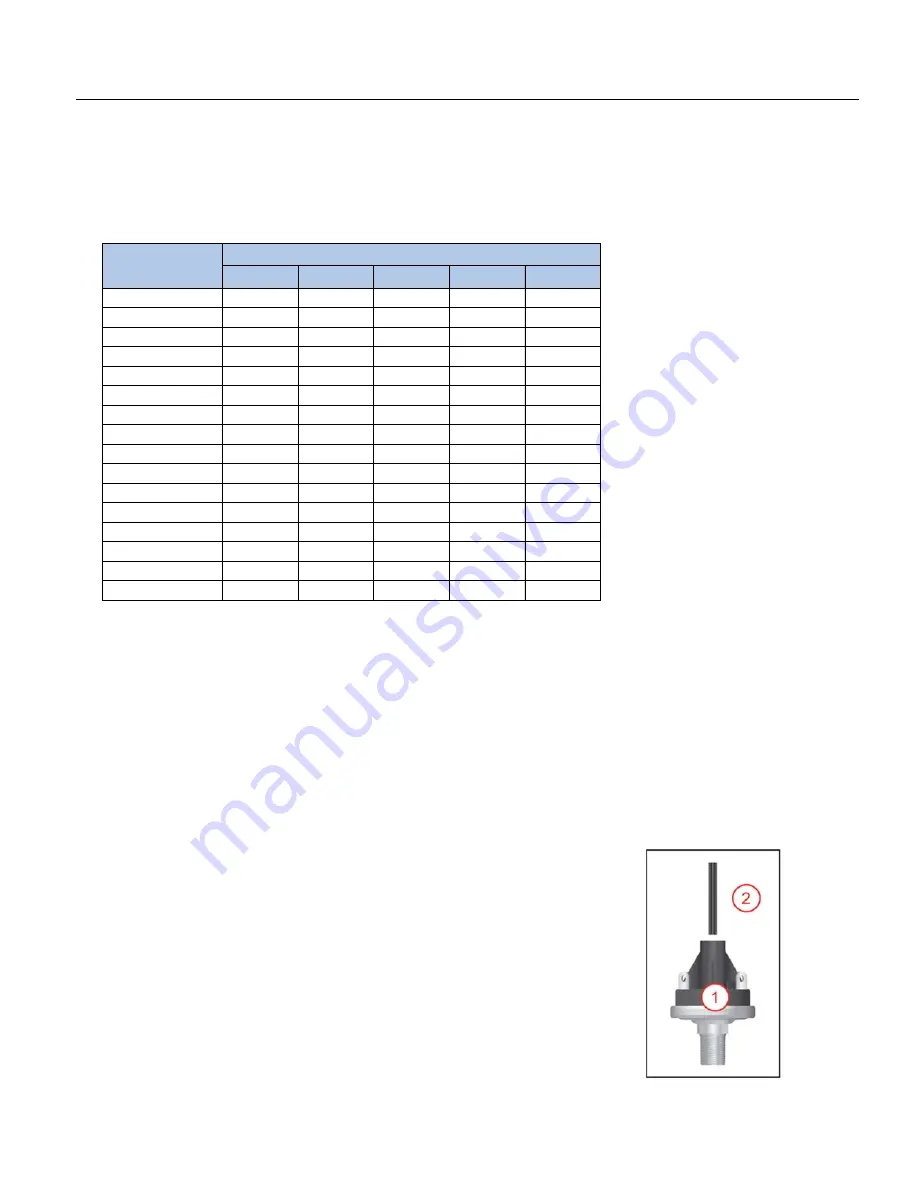
INSTALLATION AND SETUP
Drive Configuration
25
Maximum Amps (DIP SW1 – Positions 1–5)
If either SW1 – Position 6 or 7 is in the
UP
position, switches 1–5 are re-purposed to configure maxi-
mum amp settings for surface or PSC motors.
Use the following table to select the combination of DIP switches that corresponds to an overload
current value equal to or less than the motor nameplate current rating.
Pressure Input Selection (DIP SW2 – Position 1)
Ensure that the drive is configured for the type of pressure sensor or transducer being used:
•
If using a standard pressure sensor (included), DIP SW2 Position 1 must be in the
PS
(down)
position.
•
If using a 4-20 mA pressure transducer (optional), DIP SW1 Position 5 must be in the
XDCR
(up)
position.
Adjusting Pressure Setting
IMPORTANT:
Monitor pressure gauge during initial startup to ensure system does not over-pres-
surize.
Pressure Sensor:
The sensor (1) is preset at the factory to 50 psi (3.4 bar), but
can be adjusted by the installer using the following procedure:
•
Remove the rubber end-cap.
•
Using a 7/32” Allen-wrench (2), turn the adjusting screw clockwise to
increase pressure and counter-clockwise to decrease pressure. The adjust-
ment range is between 25 and 80 psi (1.7 and 5.5 bar). Note: 1/4 turn =
approximately 3 psi (0.2 bar).
•
Replace the rubber end cap.
•
Cover the pressure sensor terminals with the rubber boot provided. Do not
place boot in direct sunlight.
IMPORTANT:
Do not exceed the mechanical stop on the pressure sensor.
Max Amps
SW1
1
2
3
4
5
4.6 A
4.7 A
5.0 A
6.0 A
6.2 A
6.4 A
8.1
8.4
9.1
9.5
9.8
10.0
10.4
11.0
12.0
13.1
Summary of Contents for SUBDRIVE UTILITY
Page 1: ......
Page 42: ...SPECIFICATIONS Notes 42 Notes ...
Page 45: ...Manuel d utilisation ...
Page 89: ...Manual del propietario ...