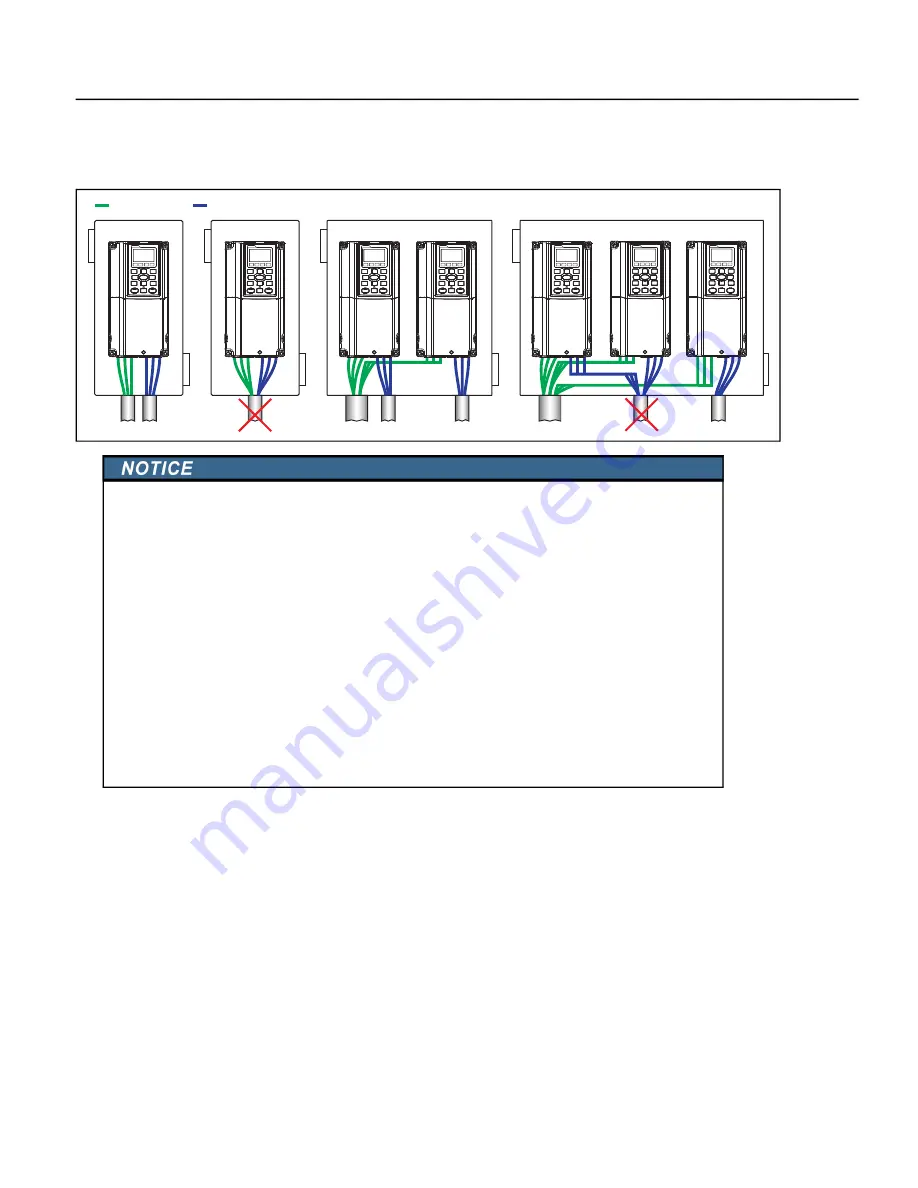
ELECTRICAL INSTALLATION
Wiring Guidelines
35
ELECTRICAL INSTALLATION
Wiring Guidelines
1.
Mount the drive as close as possible to the service entrance panel. Connect directly to the service
entrance, not to a sub-panel.
2. Use a dedicated branch circuit for the drive. Verify that the circuit is equipped with a properly-sized cir
-
cuit breaker or fuse.
3. Separate input power and motor wiring by at least 8 in. (20.3 cm).
4. Cross over other branch circuits and facility wiring at a 90
angle. If necessary to run wires in parallel,
separate by at least 8 in. (20.3 cm).
5. All control wiring—sensors, switches, transducers, etc.—should be in a separate conduit routed individ
-
ually, not parallel, from high voltage wiring. In addition, any shielded cables should be properly
grounded.
6. Treat Open-Delta power configuration (two-transformer utility bank) as single-phase power and size
VFD and power wiring accordingly.
7. Install a line reactor for VFDs in pump systems with dedicated service transformer to protect VFD from
transient power surges and provide some degree of harmonics distortion mitigation.
Power Wires
Motor Wires
ض
ض
ض
ض
ض
Risk of damage to VFD
,
or malfunction can occur.
Follow all wire routing and grounding instructions carefully. Inductive currents caused by parallel wiring,
or close proximity between high voltage and control wiring can cause unexpected behaviors.
•
Do not run input power and motor wires in the same conduit.
•
Do not run motor wires from multiple VFDs in common conduit.
•
Do not run control wiring parallel with high voltage wiring.
•
Do not run VFD wiring parallel with building or facility wiring.
•
Do not use aluminum wires for VFD connections.
•
Do not install power factor correction capacitors, surge suppressors, or RFI filters on the VFD output.
•
Do not install a magnetic contactor or disconnect in the motor circuit.
•
Do not leave wire fragments, metal shavings or other metal objects inside the VFD.
•
Improper splicing or damage to motor cable insulation may expose the conductor(s) to moisture and
can produce motor cable failure.
•
For retrofit application, check the integrity of power and motor leads. This requires measuring the
insulation resistance with a suitable megohm-meter.
Summary of Contents for CERUS X-DRIVE CXD-003A-4V
Page 2: ......
Page 3: ...CERUS X DRIVE INSTALLATION AND OPERATION MANUAL Firmware Version 1 2 Franklin Electric Co Inc ...
Page 96: ...OPERATION Protection Features 96 ...
Page 112: ...ADVANCED APPLICATION OPTIONS Multi Drive Configurations 112 ...
Page 124: ...COMMUNICATIONS BACnet Communication 124 ...
Page 128: ...ACCESSORIES Optional Extension Cards 128 Frame D Frame E Frame F ...
Page 129: ...ACCESSORIES Optional Extension Cards 129 Frame G Frame H ...
Page 132: ...ACCESSORIES Optional Extension Cards 132 ...
Page 234: ...PARAMETER REFERENCE TABLES Parameter Descriptions Motor Menu 234 ...
Page 250: ...GLOSSARY 250 ...